Choosing Injection Molding Materials
Injection molding is a versatile and cost-effective manufacturing process for creating a wide range of plastic parts. But with a vast array of injection molding materials available, selecting the right one can feel overwhelming. Choosing the ideal material goes beyond just aesthetics; it’s about finding the perfect match for your product’s desired properties and the demands of your application.
This will guide you through the key considerations for selecting injection molding materials. We’ll explore different material types, their properties, and how they can impact your final product.
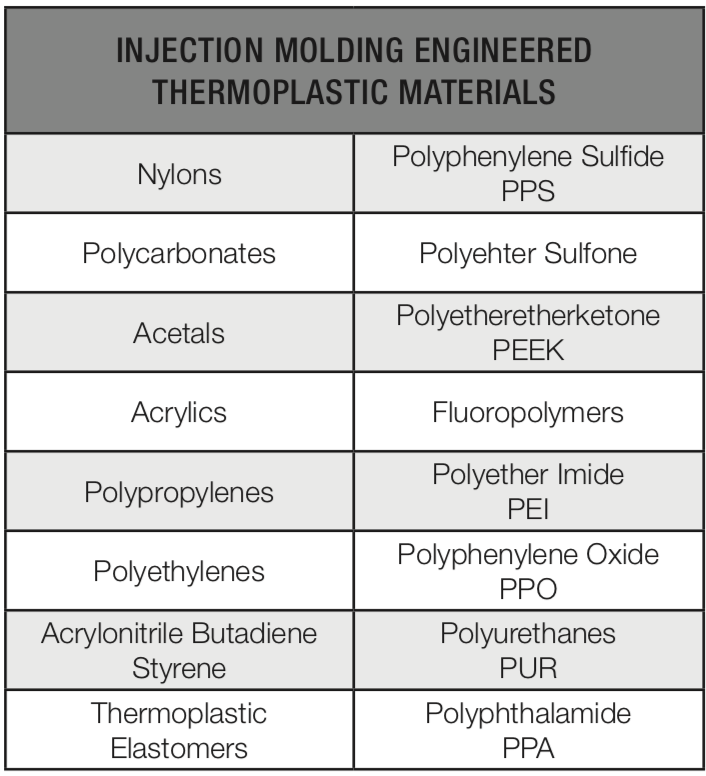
Understanding Your Needs – Desired Properties
Before diving into material options, identify the desired properties for your plastic parts. Here are some key factors to consider:
- Mechanical Strength and Durability – Will your parts experience high stress, impact, or wear? Materials like nylon or acetal offer excellent strength and durability.
- Heat Resistance – Will your parts be exposed to high temperatures during use? Thermoplastics like Polycarbonate (PC) can withstand high heat without deformation.
- Chemical Resistance – Will your parts come into contact with chemicals, solvents, or oils? Consider materials with strong chemical resistance, like polypropylene (PP) or polyethylene (PE).
- Weight – Is lightweight construction a priority? Polystyrene (PS) is an excellent choice for parts where weight reduction is crucial.
- Flexibility – Do your parts require some degree of bend or give? Thermoplastics like TPE (thermoplastic elastomer) offer flexibility while maintaining good form.
- Aesthetics – Do your parts require a clear or transparent finish? Polymethyl methacrylate (PMMA), also known as acrylic, offers excellent clarity. On the other hand, if color is a major factor, many injection molding materials can be pigmented to achieve your desired aesthetic.

Exploring Injection Molding Material Types
The world of injection molding materials is vast, offering a variety of options to suit the specific needs of your project. Here’s a deeper dive into some of the most common and versatile choices:
Popular Material Properties
- Acrylonitrile Butadiene Styrene (ABS) – This workhorse material provides a well-rounded combination of strength, toughness, and affordability. ABS is commonly used for:
- Electronic components (housings, cases)
- Toys (building blocks, figurines)
- Appliance parts (knobs, handles)
- Polycarbonate (PC) – Known for its exceptional trifecta of strength, heat resistance, and clarity. PC finds applications in:
- Medical devices (syringes, housings)
- Safety equipment (visors, helmets)
- Automotive parts (instrument panels, lenses)
- Polyamide (Nylon) – This versatile material offers a combination of strength, wear resistance, and good chemical resistance. Nylon is used in various applications, including:
- Gears and bearings (due to low friction)
- Industrial components (pipes, valves)
- Textiles (fibers for clothing and carpets)
- Polypropylene (PP) – A lightweight and cost-effective option with good chemical resistance. PP is commonly used for:
- Packaging (food containers, bottles)
- Living hinge applications (flexible closures in containers)
- Textiles (non-woven fabrics)
- Polyethylene (PE) – Available in various densities (high-density PE or HDPE, low-density PE or LDPE), PE offers a good balance of flexibility, durability, and chemical resistance. PE has widespread applications in:
- Films (plastic wrap, bags)
- Containers (bottles, tubs)
- Pipes and tubing

Beyond the Basic Materials
While desired properties and material types are crucial, other factors also play a significant role in injection molding material selection:
- Mold Design – The complexity of your mold design can influence material selection. Some materials, like ABS, flow more readily and might be better suited for intricate features or tight tolerances.
- Cost-Effectiveness – Consider not just the material cost, but also processing requirements (energy consumption, cycle times) and potential for scrap or rework. Finding a balance between desired properties and overall project cost is essential.
- Processing Considerations – Different materials have varying melting points, flow characteristics (how easily they flow in the mold), and shrinkage rates (how much they shrink after cooling). These factors must be considered during the injection molding process to ensure parts meet dimensional requirements and avoid warping or cracking.
A Look at Advanced Materials
While we have focused on common injection molding materials, there’s a whole world of specialty options available for specific needs. Here’s a brief look at some advanced materials:
- Liquid Crystal Polymers (LCPs) – Offering exceptional dimensional stability, heat resistance, and chemical resistance, LCPs are ideal for electronic components and aerospace applications.
- Polyether Ether Ketone (PEEK) – Known for its outstanding high-temperature performance, chemical resistance, and biocompatibility, PEEK is used in demanding applications like medical implants and industrial components.
- Thermoplastic Polyurethanes (TPUs) – These versatile materials offer a unique combination of flexibility, durability, and chemical resistance. TPUs are commonly used for footwear, hoses, and seals.
The Importance of Material Testing
Once you’ve narrowed down your material selection, material testing is crucial. Testing can help verify a material’s suitability for your application by evaluating its mechanical properties, chemical resistance, and heat deflection temperature. This step ensures your final parts perform as expected in real-world conditions.
Partnering for Injection Molding Success
Choosing the right injection molding material is a critical step in the manufacturing process. By understanding your desired properties, exploring different material options, and consulting with an experienced injection molding partner like Frigate, you can ensure your plastic parts achieve optimal performance and cost-efficiency.
Contact Frigate Today
At Frigate, we are committed to helping you bring your ideas to life. Our team of experts can guide you through every step of the injection molding process, from material selection and mold design to high-volume production. We offer a wide range of services and capabilities to meet your specific needs.
Contact Frigate today to discuss your project and discover how we can help you achieve success with injection molding. Let’s work together to turn your vision into a reality.