- Impact Resistance
Electrical & Industrial Enclosures
Electrical & Industrial Enclosures are engineered from 10-14 gauge or 316L stainless steel, with FEA validation to withstand impact, vibration, and torsional loads. Hinge assemblies and multi-point latches maintain door integrity under dynamic stress. All units meet IEC 62262 IK10 for impact resistance in mechanical risk zones.

Our Clients
Trusted by Engineers and Purchasing Leaders
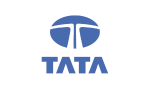
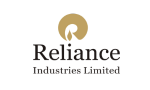


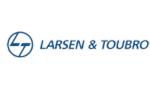
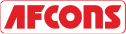


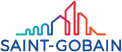

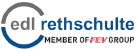

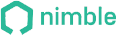
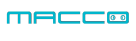









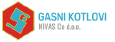
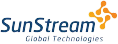

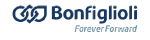


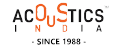
- Versatile Offerings
Our Electrical & Industrial Enclosures Products
Explore our range of high-quality Electrical & Industrial Enclosures today.
- Real Impact
Words from Clients
See how global OEMs and sourcing heads describe their experience with our scalable execution.
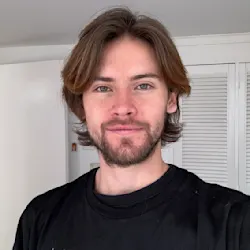
“Quick turnaround and solid quality.”
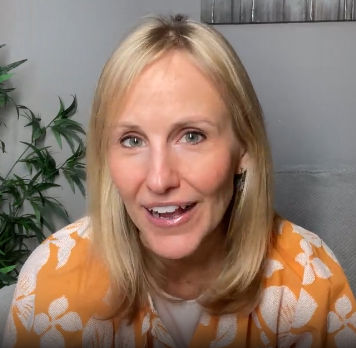
“The instant quote tool saved us time, and the parts were spot-on. Highly recommend Frigate!”
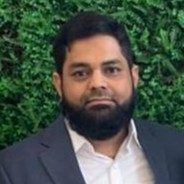
“I would strongly recommend Frigate to anyone who wants to do Rapid Prototyping, and take their ideas to manufacturing. One firm doing all kinds of Product Development!”
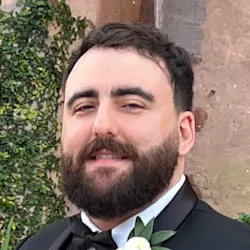
“Great service, fair price, and the parts worked perfectly in our assembly.”
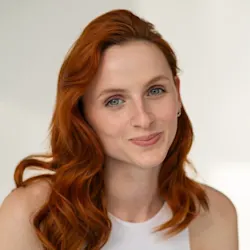
“Top-notch machining and fast shipping. Very satisfied with the results.”
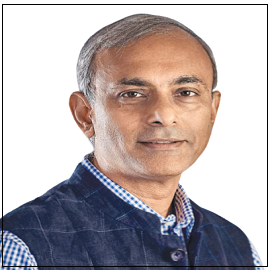
“The next disruption is happening in Prototyping & Manufacturing on-demand and Frigate is leading the way! I personally believe the Frigate's way of IIOT enabled cloud platform with Al.”
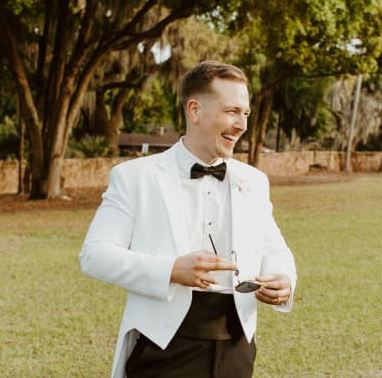
“Frigate delivered high-quality parts at a competitive price. The instant quote tool is a huge plus for us!”

“We appreciate the precision and quality of the machined components in the recent delivery—they meet our specifications perfectly and demonstrate Frigate’s capability for excellent workmanship.”
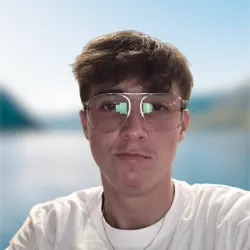
“Flawless execution from quote to delivery.”

“I am absolutely happy to work with supplier like Frigate who were quite proactive & result oriented . Frigate has high willingness team who has strong know how & their passion towards the products & process were absolutely thrilling.”
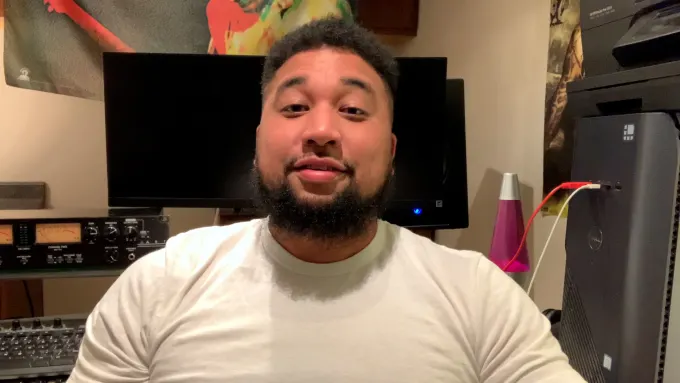
“The precision on these parts is impressive, and they arrived ahead of schedule. Frigate’s process really stands out!”
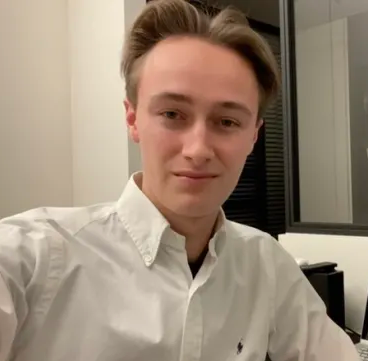
“Parts were exactly as spec’d, and the instant quote made budgeting a breeze.”
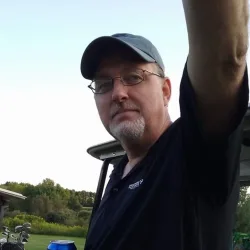
“Good value for the money.”
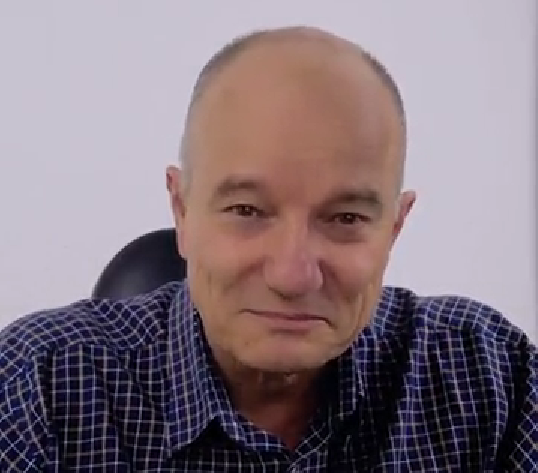
“The finish was perfect, and the team was easy to work with.”

“Working with Frigate has been great. Their proactive, results-driven approach and expertise shine through in every project. It's been a pleasure collaborating with them.”

"We are highly satisfied with the timely delivery and quality of the MIG Welding Cable from Frigate. Their attention to detail, secure packaging, and quick responsiveness stood out. We confidently recommend Frigate Engineering Services Pvt. Ltd. as a reliable manufacturing partner."
We export to 10+ countries
Frigate’s Global Presence
Frigate takes pride in facilitating “Make in India for the globe“. As our global network of Frigaters provides virtually limitless capacity, and through our IoT enabled platform your parts go directly into production. By digitally and technologically enabling “the silent pillars of the economy” MSME and SME manufacturing industries, we are able to tap the huge potential for manufacturing to bring the best results for our clients.

100,000+
Parts Manufactured
250+
Frigaters
2000+
Machines
450+
Materials
25+
Manufacturing Process
Industry Applications
Enclosures protect switchgear, transformers, relays, and SCADA systems in substations and power distribution nodes, ensuring IP-rated sealing, arc-flash containment, and isolation from weather, rodents, and unauthorized access.
Used to house PLCs, HMIs, VFDs, and terminal blocks in manufacturing environments, enclosures provide mechanical protection, EMI shielding, and thermal dissipation while maintaining required spacing per IEC 60204-1.
Enclosures in hazardous areas (Zone 1, Zone 2) must meet ATEX/IECEx certification, include flameproof joints, and resist chemical degradation from H₂S, hydrocarbons, and salt-laden air in onshore/offshore installations.
Enclosures are deployed for signal controllers, power modules, and communications equipment, requiring NEMA TS2 compliance, vibration resistance, and low-temperature operability in outdoor roadside and rail environments.
Installed in pump stations, control rooms, and chemical feed areas, these enclosures must provide corrosion resistance, ingress protection, and compatibility with corrosive atmospheres like chlorine and sulfur compounds.
Used for fiber distribution panels, UPS modules, and remote electronics, these enclosures require thermal regulation, EMI shielding, and IP/NEMA protection for both indoor equipment rooms and outdoor base stations.

- Signal Protection
EMI/RFI Shielding in Interference Zones
Conductive enclosure bodies with bonded seams and internal grounding paths ensure shield integrity against broadband interference and induced currents.
Conductive elastomeric gaskets or EMI fingerstock provide reliable attenuation across seams and access points, verified under IEEE 299 test standards.
Internal assemblies use isolated panels to decouple sensitive circuits from structural noise paths, maintaining signal integrity in mixed-signal environments.

Frigate uses FEA (Finite Element Analysis) to predict stress points under impact and vibration during enclosure design. High-load zones are reinforced using ribbing patterns and glass-filled resins for added strength. Snap-fit designs are tested for fatigue under repeated insertion cycles. All enclosures comply with IEC 62262 impact ratings based on application.
Plastic enclosures are exposed to salt fog, acidic vapors, and industrial solvent simulations based on ASTM D543. Frigate selects materials like PPO or PVDF that resist oxidation and hydrolysis. Long-term testing ensures no cracking, swelling, or embrittlement occurs. Results are logged as part of Frigate’s internal qualification protocol.
All Frigate enclosures for damp environments are designed with integrated gaskets and sealed joints rated up to IP67. Plastics are chosen with low water absorption rates, typically under 0.3% by weight. Ventilation options include hydrophobic membranes to equalize pressure without allowing moisture ingress. Internal spacings follow IEC 60664 to prevent arc tracking.
Frigate applies conductive EMI coatings inside the enclosure and integrates molded-in grounding points connected via stainless steel hardware. These points are tested for continuity and surface resistance below 10 ohms. Shielding effectiveness is validated under IEEE 299 or MIL-STD-285 standards. Ground lugs are installed to allow bonding with external systems.
Frigate uses materials with low thermal expansion coefficients and high dimensional stability, like glass-reinforced polycarbonate. Mold shrinkage is controlled using precision tooling and cooling profiles. Enclosures are inspected for warpage and tolerance shift using 3D metrology. Design allowances are made for long-term creep under constant mechanical load.
We'd love to Manufacture for you!
Submit the form below and our representative will be in touch shortly.
LOCATIONS
Registered Office
10-A, First Floor, V.V Complex, Prakash Nagar, Thiruverumbur, Trichy-620013, Tamil Nadu, India.
Operations Office
9/1, Poonthottam Nagar, Ramanandha Nagar, Saravanampatti, Coimbatore-641035, Tamil Nadu, India. ㅤ
Other Locations
- Bhilai
- Chennai
- USA
- Germany