The art of forging, shaping metal through heat and compressive force, has been around for many years. From the swords of ancient warriors to the crankshafts of modern engines, forged components have a reputation for unparalleled strength and durability. But the success of any forging project hinges on one crucial decision- selecting the right materials for forging.
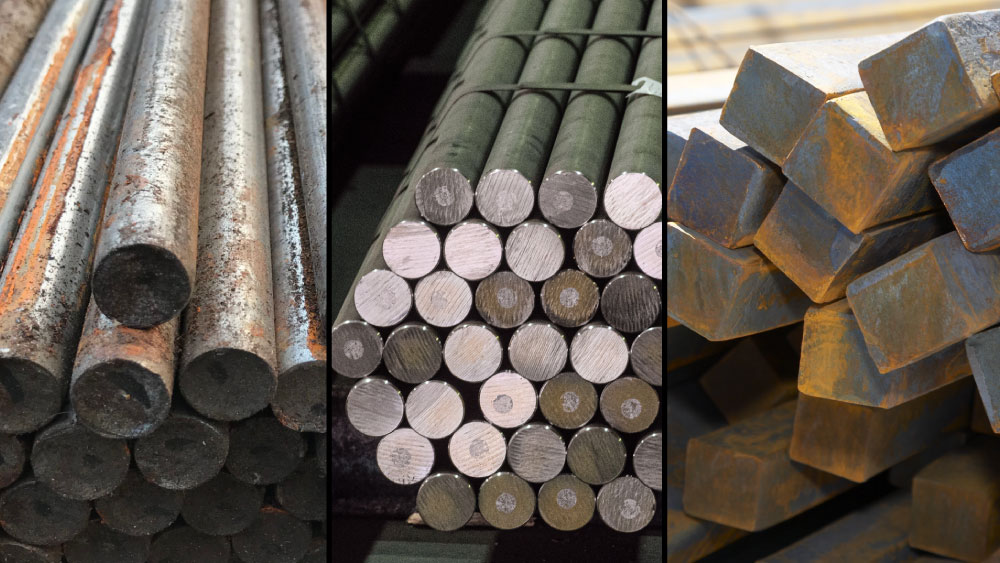
Choosing the ideal forging material requires careful consideration of several factors. This guide will equip you with the knowledge to navigate this critical step, ensuring your forged parts perform flawlessly in their intended application.
Understanding Key Material Properties
Before diving into specific materials, let’s explore some fundamental properties that influence forging material selection-
- Workability- This refers to a material’s ability to deform plastically under force without cracking or tearing. Good workability is essential for shaping the metal during the forging process.
- Strength- The ability of the material to resist deformation under load. Forged components often experience significant stress, so adequate strength is paramount.
- Ductility- A measure of how much a material can elongate before breaking. Ductile materials are ideal for forging complex shapes without compromising integrity.
- Malleability- Like ductility, but specific to the ability to flatten the material into thin sheets without fracturing.
- Formability- A combination of workability, ductility, and malleability, indicating how easily a material can be shaped into a desired form.
- Heat Resistance- The ability of the material to withstand high temperatures without losing its strength or undergoing significant changes in grain structure. Forging often involves heating the metal to high temperatures.
- Corrosion Resistance- How well the material resists rust and other forms of environmental degradation. This is crucial for parts exposed to harsh environments.
Popular Materials For Forging and their Applications
Now that we understand the key properties, let’s explore some of the most common forging materials and their ideal applications-
- Steel- The undisputed champion of forging, steel offers a fantastic balance of strength, workability, and affordability. Different steel grades cater to specific needs. Low-carbon steel prioritizes workability for intricate shapes like gears and levers. Medium-carbon steel strikes a balance between workability and strength, making it suitable for crankshafts and connecting rods. High-carbon steel prioritizes strength for tools and machine components like chisels and punches.
- Alloy Steel- By adding elements like chromium, nickel, or molybdenum, steel’s properties can be further enhanced. Alloy steels offer superior strength, heat resistance, and corrosion resistance, making them ideal for demanding applications like gears, crankshafts, and aerospace components. Nickel-chromium alloys, for instance, are known for their exceptional strength at high temperatures, making them ideal for turbine blades and discs in jet engines.
Source – https://iqsdirectory.com/
- Aluminum- Lightweight and boasting excellent corrosion resistance, aluminum is a popular choice for applications where weight reduction is critical, such as aircraft parts and automotive components. However, aluminum’s lower strength necessitates careful design considerations and often necessitates alloying with other elements like copper or magnesium to improve its mechanical properties.
- Copper- Highly malleable and ductile, copper finds use in applications requiring good electrical conductivity and formability, such as electrical conductors, heat sinks, and decorative elements. Its excellent corrosion resistance makes it a popular choice for plumbing components and marine applications.
- Brass- An alloy of copper and zinc, brass offers a good balance of strength, workability, and corrosion resistance. It’s commonly used for plumbing fixtures, valves, and decorative hardware. Brass can also be formulated to prioritize specific properties; for instance, adding lead to brass enhances its machinability, making it ideal for complex parts.
Matching Material Selection to Application
When selecting a forging material, consider the following factors specific to your application-
- Required Strength- How much stress will the forged component experience?
- Weight Considerations- Is minimizing weight a priority?
- Formability Needs- How complex is the desired shape?
- Heat Exposure- Will the component be subjected to high temperatures?
- Corrosion Resistance Requirements- Will the party be exposed to a corrosive environment?
By carefully evaluating these factors alongside the material properties discussed earlier (workability, strength, ductility, etc.), you can make an informed decision. Remember, there’s no single “best” forging material. The ideal choice depends on the unique needs of your application.
Frigate – Your Partner in Forging Excellence
Selecting the right forging material is just the first step in the forging journey. Even the best material choice can be compromised by a lack of expertise in the forging process itself. Here at Frigate, we offer comprehensive forging services that go beyond material selection.
Our team of experienced professionals doesn’t just possess in-depth knowledge of various forging materials; they are experts in the entire forging process. We can assist you with-
- Material Selection and Design Consultation- We’ll work closely with you to understand your application’s requirements and recommend the optimal forging material based on factors like strength, weight, and formability needs. Our team can also provide valuable insights during the design phase, helping you optimize your component for the forging process.
- Expert Forging- With state-of-the-art forging equipment and a team of skilled technicians, Frigate ensures your components are forged to precise tolerances and meet the highest quality standards.
- Precision Machining- Forging often creates a near-net shape, but sometimes, additional machining is required to achieve the final dimensions and features. Our in-house machining capabilities allow for seamless integration of forging and machining processes, ensuring your forged components meet exact specifications.
Frigate’s commitment goes beyond just the technical aspects. We understand that exceptional customer service is equally important. Our team is dedicated to clear communication, keeping you informed throughout the entire forging process.
For superior forging solutions that deliver exceptional results, contact Frigate today. Let us transform your vision into a forged component that exceeds expectations. We are your partner in forging excellence.