Sheet Metal Fabrication Services
Frigate utilizes CNC punching, laser cutting, and bending for precise sheet metal fabrication services. Our team applies high-tolerance methods, including MIG and TIG welding, for durable, custom parts.

What We Do
Precision Cutting Methods
We ensure precision in sheet metal parts with our integrated end-to-end process, utilizing advanced cutting technologies like laser, plasma, and waterjet for superior accuracy and material optimization.
Get Your Quote Now
- Instant Quotation
- On-Time Delivery
- Affordable Cost
Empowering Industries with Precision Engineering
Innovative Sheet Metal Techniques for Aerospace Components
Lightweight design, strength, and exacting standards are crucial in aerospace components. Sheet metal fabrication is the solution with high-accuracy processes like CNC punching, laser cutting, and bending. These techniques create complex geometries with tight tolerances, ensuring reliable quality and performance. Advanced welding methods like TIG and MIG welding improve strength and durability. Lightweight metals such as aluminum and titanium are used to optimize weight without sacrificing structural integrity. Customization allows for producing specialized parts that meet strict aerospace requirements, enhancing manufacturing efficiency and part performance.
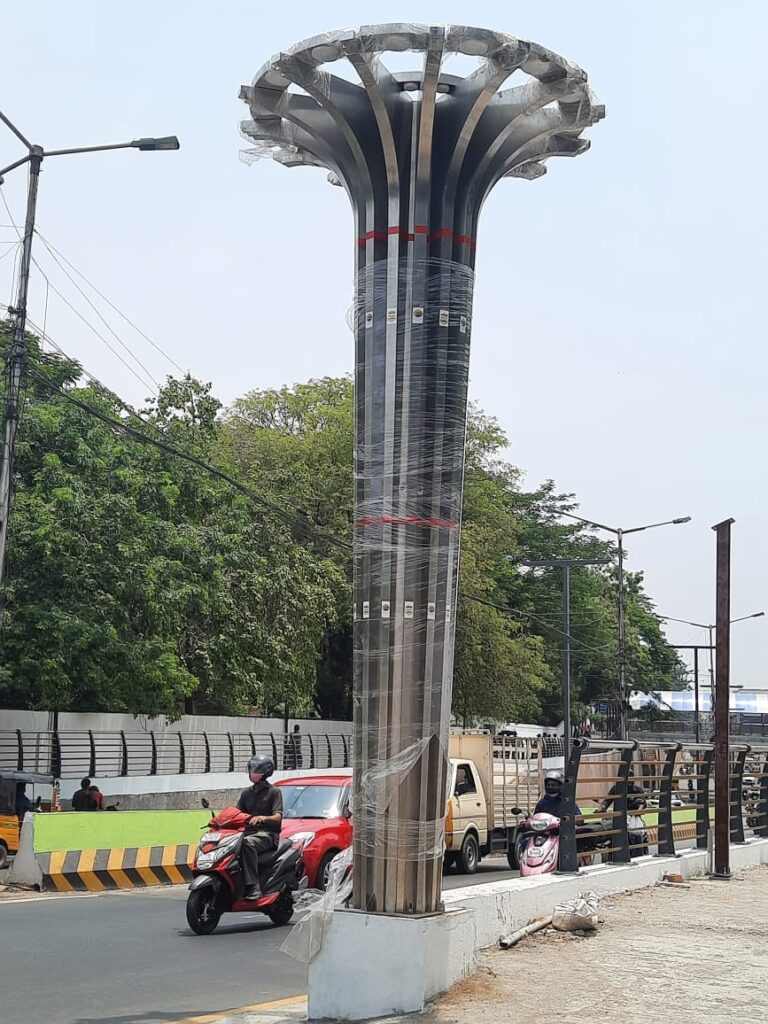

Sheet metal fabrication uses laser cutting, punching, and bending for precision.
Our Clients
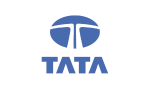
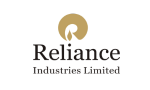


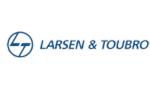
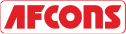


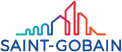

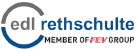

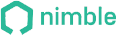
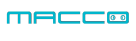









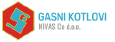
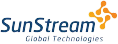

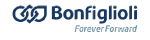


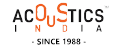
Our Business Verticals
Automotive
Aerospace
Energy Sector
Defense
Electrical
Healthcare
Construction
Agricultural
Maximizing Performance and Efficiency with Advanced Metallurgical Process Integration
Frigate integrates advanced metallurgical processes like powder metallurgy and electron beam welding into sheet metal fabrication for high-performance components. These processes are precisely controlled to ensure consistent material properties and mechanical integrity. Real-time process monitoring and automation help minimize energy use and optimize cycle times, enabling efficient aerospace and defense parts production. The integration of these technologies ensures that performance standards are met without compromising production efficiency.
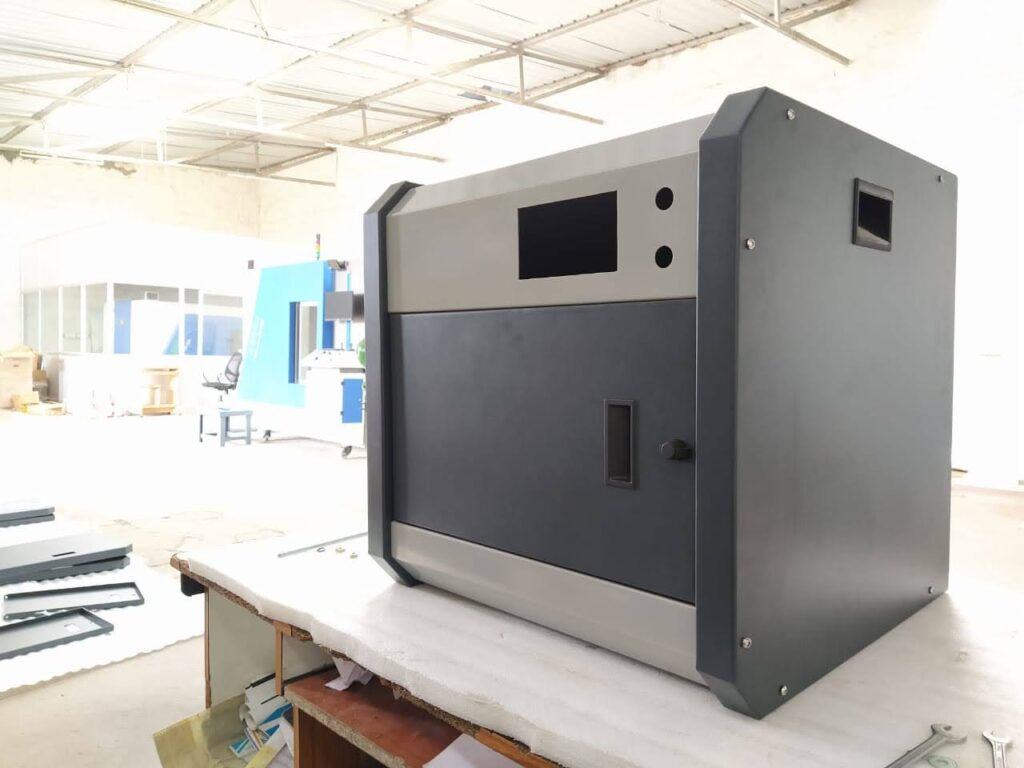
Ensuring Precision and Reliability in Complex, Multi-Material Assemblies
Frigate achieves sub-micron tolerances in multi-material assemblies through advanced manufacturing systems. Techniques like AI-driven quality control and micro-milling ensure precise fabrication across complex geometries and materials. These methods maintain the required material integrity and structural performance. The seamless integration of these technologies allows for producing complex aerospace and automotive components with exacting precision and reliability.
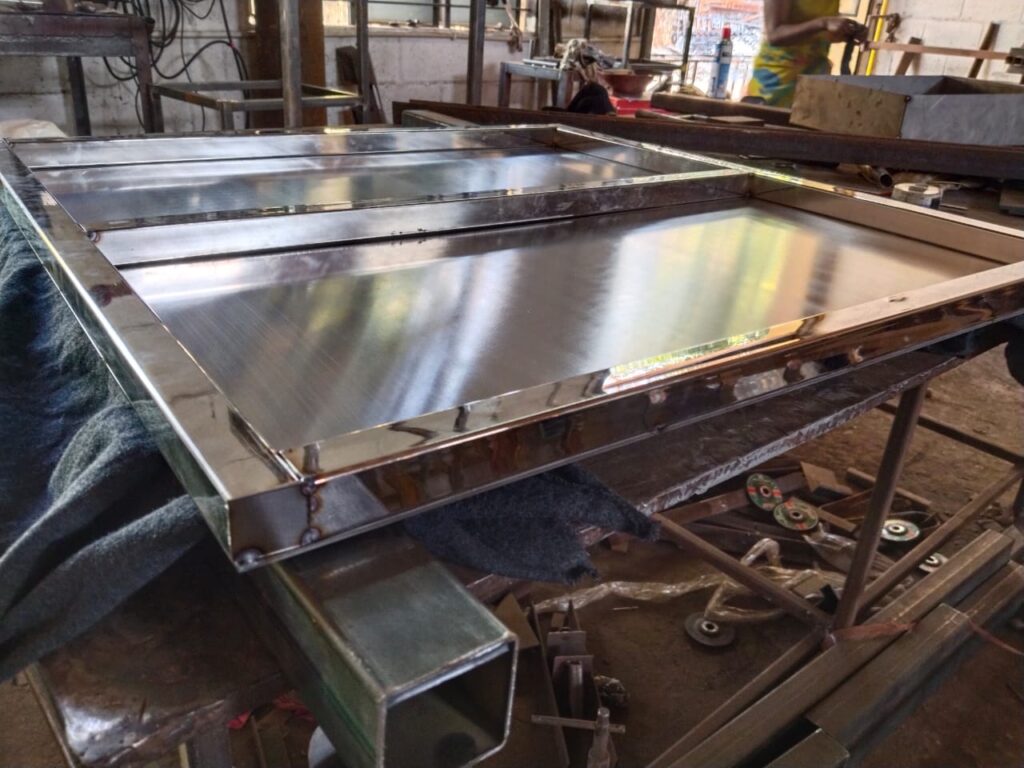
Improving Production Efficiency with Predictive Analytics in Multi-Technology Environments
Frigate utilizes predictive analytics and machine learning to manage multi-stage, multi-technology sheet metal fabrication processes. By optimizing throughput and reducing downtime, these technologies improve production efficiency. Predictive tools help anticipate and address potential issues, ensuring the smooth integration of techniques like additive manufacturing, subtractive machining, and hybrid welding. This results in enhanced production timelines and consistent, high-quality output.

Our Sheet Metal Fabrication Process






High-precision laser or waterjet cutting is used for intricate designs, providing tight tolerances and complex shapes while minimizing material wastage.
Advanced CNC punching machines or stamping presses produce high-volume parts with intricate hole patterns or embossments, achieving consistent repeatability and accuracy.
Advanced 3D forming processes, such as hydroforming or deep drawing, shape sheet metal into deep, complex geometries that cannot be achieved by traditional bending or stamping alone.
Robotics-driven welding, such as MIG or TIG, ensures consistent weld quality, reduces labor costs, and speeds up production, particularly for large runs or intricate assemblies.
Computer-controlled press brakes calibrated for material-specific bending parameters help achieve precise bends with minimal springback, ensuring accurate part dimensions.
Post-fabrication processes like electropolishing or Physical Vapor Deposition (PVD) coating enhance the surface finish, improve corrosion resistance, and increase the part's aesthetic appeal without compromising its functionality.
Sheet Metal Fabrication Materials
Sheet metal fabrication uses various materials, each with unique properties suited for specific applications. Selecting the right material is crucial for ensuring performance, durability, and cost-effectiveness, from lightweight aluminum alloys in aerospace to high-strength titanium in military applications.
Aluminum alloys like 5052 and 6061 are lightweight, corrosion-resistant, and offer a high strength-to-weight ratio. They provide excellent formability and weldability, making them ideal for aerospace, automotive, and marine applications. These alloys also perform well under high and low temperatures and can be anodized for enhanced durability.
Stainless steel alloys like 304 and 316 offer superior resistance to corrosion and high temperatures. 304 provides balanced strength and workability, while 316, with its molybdenum content, excels in harsh environments like marine and chemical processing. This material is ideal for high-performance applications requiring durability and hygiene.
Mild steel, such as ASTM A36, is easy to fabricate and offers good weldability and formability. It is widely used in construction and automotive industries. While less corrosion-resistant than stainless steel, it can be treated with galvanized coatings for enhanced durability in exposed environments.
Copper is an excellent conductor of heat and electricity, ideal for electrical components and heat exchangers. Copper alloys like C110 are used for power transmission, while C17200 (beryllium copper) is known for its high strength and fatigue resistance, which makes it ideal for precision mechanical parts.
Brass, a copper-zinc alloy, is highly machinable and offers good corrosion resistance. C36000 brass is commonly used for electrical connectors and fittings. It also provides excellent low-friction properties, making it suitable for gears, valves, and pumps.
Titanium alloys, such as Ti-6Al-4V, are known for their low weight and strength and exceptional corrosion resistance. Due to their performance at high temperatures and extreme conditions, these alloys are ideal for aerospace and military applications. Titanium is also biocompatible, making it suitable for medical implants.
Coated with zinc, galvanized steel offers excellent corrosion resistance, making it suitable for outdoor and marine applications. The G90 specification indicates a robust zinc coating, ensuring durability in harsh environments. It is commonly used in automotive parts, HVAC systems, and agricultural machinery.
Nickel alloys like Inconel 625 and Monel 400 offer exceptional heat and corrosion resistance. Inconel 625 is used in high-temperature applications such as turbines, while Monel 400 resists seawater corrosion, making it ideal for marine propulsion systems and oil drilling equipment.
Tool steel, such as D2 and O1, is used for manufacturing cutting tools, dies, and molds. D2 provides high wear resistance, which is ideal for precision cutting. At the same time, O1 is valued for its toughness and ease of heat treatment, making it suitable for mold and die production in sheet metal fabrication.
Frigate Approach
Efficient Compliance with Regulatory and Certification Standards
Frigate ensures compliance with AS9100 and ISO 9001 by integrating streamlined quality control processes. These processes provide real-time traceability and material validation throughout production. Automated tracking systems monitor every stage, ensuring adherence to certification requirements. Comprehensive documentation practices support transparency and maintain accuracy across all stages. This approach enables Frigate to swiftly adapt to regulatory changes while preserving fast production timelines and consistent quality.
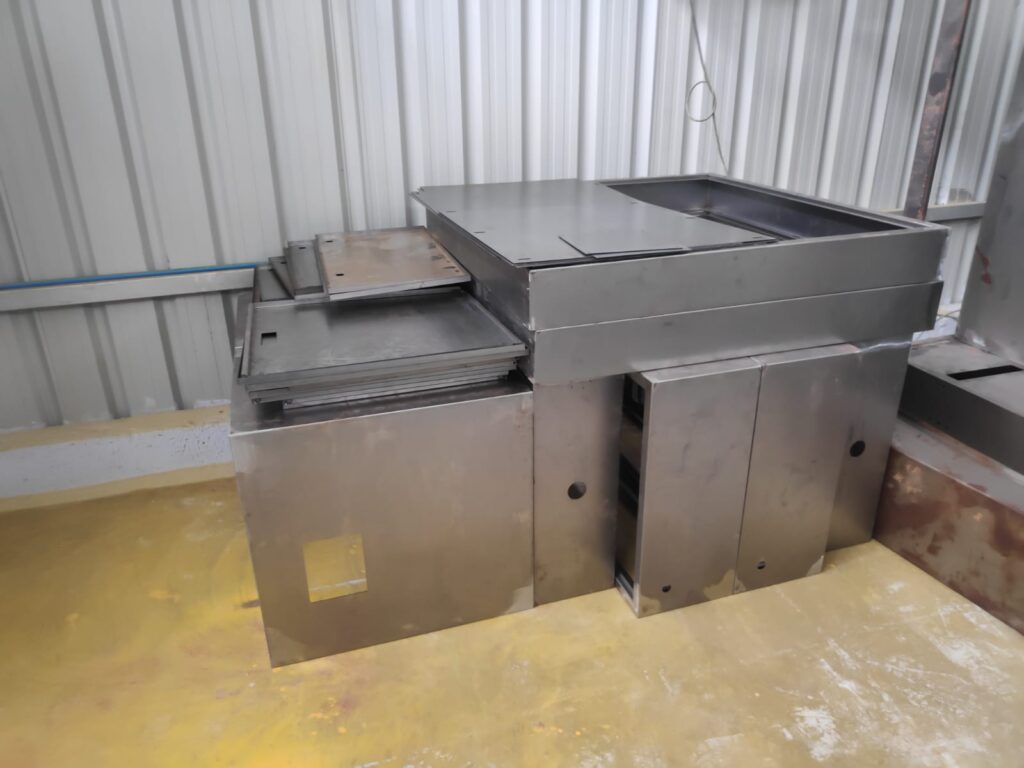
Compliance for Sheet Metal Fabrication Services
Compliance with industry standards is essential for delivering high-quality sheet metal fabrication services. We adhere to stringent regulations and certifications to maintain operational excellence and meet the specific requirements of each project. Our processes are designed to meet safety, environmental, and material-specific standards, ensuring the integrity and performance of every fabricated component.
Key Compliance for Sheet Metal Fabrication Services
Quality management systems ensuring consistent product quality and continuous improvement.
Environmental management standards aimed at reducing waste and energy consumption.
American Welding Society standards for welding quality and procedures, ensuring precise and reliable welds.
Restriction of Hazardous Substances compliance, ensuring products are free of harmful materials.
Standard specifications for carbon structural steel, ensuring structural integrity and reliability.
Underwriters Laboratories certification for flammability of plastic materials used in electrical and electronic components.

Tolerance for Sheet Metal Fabrication Services
Variations in thickness depending on the material and processing method.
Precision for small holes, typically achieved via laser cutting or punching.
Tolerances for larger holes can vary based on the cutting method.
Precision for slots cut in sheet metal, dependent on the cutting method.
Accurate location of holes along the X and Y axes for assembly fit.
Tolerance for edges after shearing, ensuring no burrs or defects.
The allowance for material stretching during bending, influencing final dimensions.
Control over bend angles to ensure correct fitment during assembly.
Tolerance on the overall twist of the part, usually a result of thermal processes.
Flatness measured after forming, ensuring part stability during assembly.
The tolerance in parallelism between two surfaces for assembly precision.
Tolerance for surface finish affecting appearance and performance.
Consistency in material thickness across the sheet, influencing strength and precision.
Precision of corner radii, particularly important for stress distribution.

Quality Testing Standards for Sheet Metal Fabrication Services
Measures the tendency of the material to return to its original shape after bending, affecting final part geometry.
Evaluates the material's ability to deform under tensile stress without breaking, essential for forming operations.
Assesses the material's resistance to tearing under stress, ensuring durability during manufacturing processes.
Measures the material's ability to resist forces that can cause shearing, crucial for cutting operations.
Tests material's resistance to catching fire and how it burns, particularly important for safety compliance.
Tests the material’s ability to resist chemical corrosion or degradation, especially for parts exposed to harsh environments.
Evaluates the material's susceptibility to cracking under stress in corrosive environments, important for ensuring long-term durability.
Checks the perpendicularity between surfaces to ensure parts fit accurately during assembly, crucial for assembly tolerance.
Measures the concentricity of holes or circular features relative to the axis of the part, ensuring precision during assembly.
Measures internal stresses in the material caused by manufacturing processes like welding or forming, which can affect performance and part stability.
Determines the material’s resistance to crack growth under cyclic loading, ensuring the part performs well under fatigue conditions.
Measures the strength of welded joints, ensuring the welded areas can withstand the applied loads without failure.
Inspects the edges for burrs or sharp protrusions that could affect part assembly or operator safety.
Assesses any distortion or elongation of holes post-cutting, ensuring proper dimensions and alignment.
Examines the heat-affected zone around welded areas to evaluate changes in material properties, ensuring proper heat treatment.
Tests the material's electromagnetic characteristics for applications requiring specific magnetic properties, such as for electrical components.
Evaluates the material’s stability under temperature variations, important for components exposed to extreme temperature changes.
- Real Impact
Words from Clients
See how global OEMs and sourcing heads describe their experience with our scalable execution.
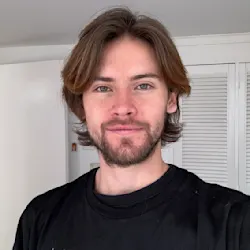
“Quick turnaround and solid quality.”
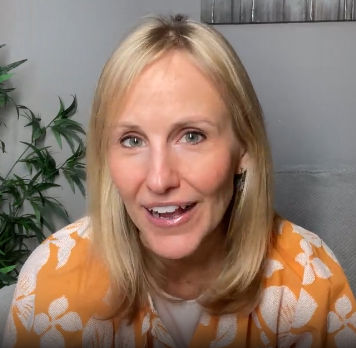
“The instant quote tool saved us time, and the parts were spot-on. Highly recommend Frigate!”
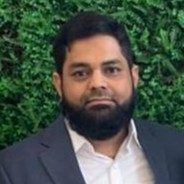
“I would strongly recommend Frigate to anyone who wants to do Rapid Prototyping, and take their ideas to manufacturing. One firm doing all kinds of Product Development!”
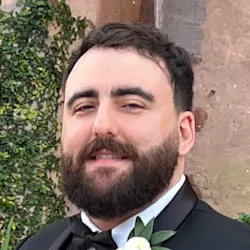
“Great service, fair price, and the parts worked perfectly in our assembly.”
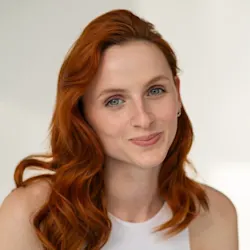
“Top-notch machining and fast shipping. Very satisfied with the results.”
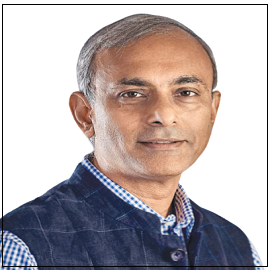
“The next disruption is happening in Prototyping & Manufacturing on-demand and Frigate is leading the way! I personally believe the Frigate's way of IIOT enabled cloud platform with Al.”
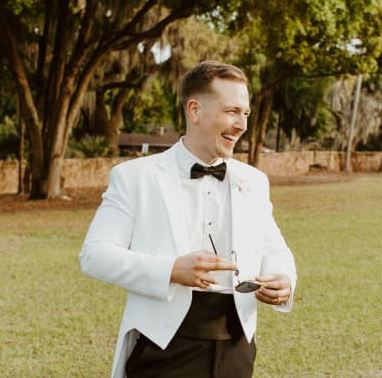
“Frigate delivered high-quality parts at a competitive price. The instant quote tool is a huge plus for us!”

“We appreciate the precision and quality of the machined components in the recent delivery—they meet our specifications perfectly and demonstrate Frigate’s capability for excellent workmanship.”
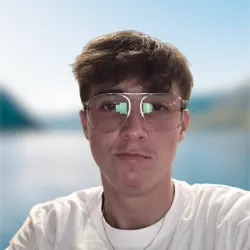
“Flawless execution from quote to delivery.”

“I am absolutely happy to work with supplier like Frigate who were quite proactive & result oriented . Frigate has high willingness team who has strong know how & their passion towards the products & process were absolutely thrilling.”
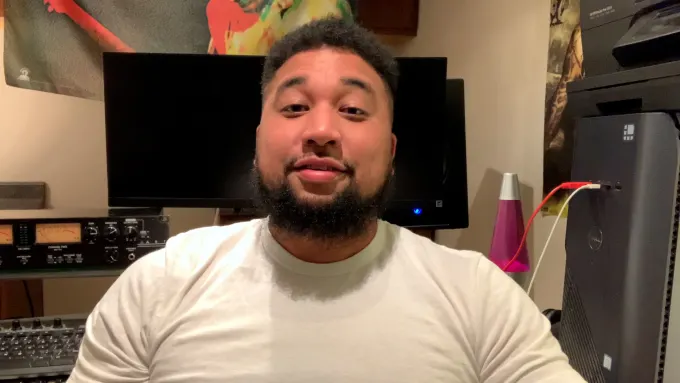
“The precision on these parts is impressive, and they arrived ahead of schedule. Frigate’s process really stands out!”
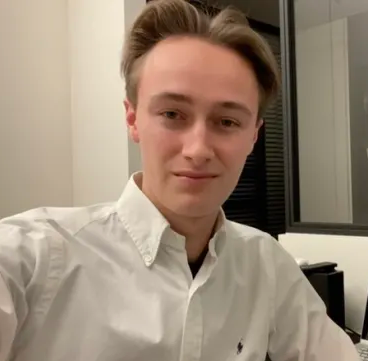
“Parts were exactly as spec’d, and the instant quote made budgeting a breeze.”
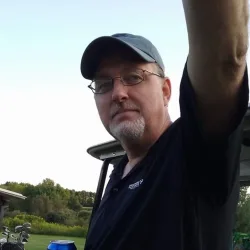
“Good value for the money.”
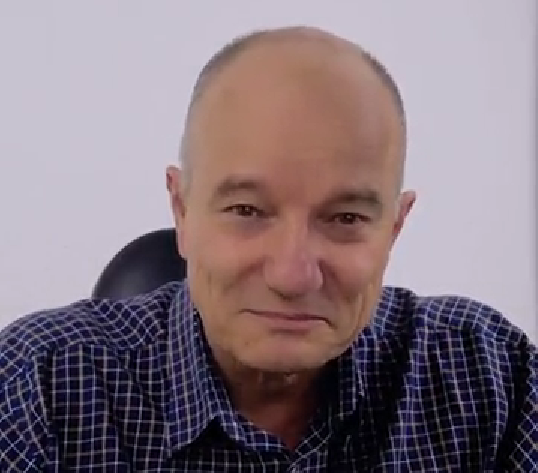
“The finish was perfect, and the team was easy to work with.”

“Working with Frigate has been great. Their proactive, results-driven approach and expertise shine through in every project. It's been a pleasure collaborating with them.”

"We are highly satisfied with the timely delivery and quality of the MIG Welding Cable from Frigate. Their attention to detail, secure packaging, and quick responsiveness stood out. We confidently recommend Frigate Engineering Services Pvt. Ltd. as a reliable manufacturing partner."
Having Doubts? Our FAQ
Check all our Frequently Asked Question
Frigate utilizes advanced CNC punching, laser cutting, and precision bending techniques to maintain tight tolerances for complex geometries in thin sheet metals. These technologies enable high accuracy and repeatability while minimizing material distortion during fabrication, ensuring that intricate designs are produced consistently, even with thinner materials.
Frigate employs specialized tooling and advanced forming techniques to mitigate material deformation when working with high-strength alloys. By carefully controlling factors such as temperature, force, and speed during bending and stamping, Frigate ensures minimal springback. It maintains the structural integrity of the material, preventing any dimensional inaccuracies.
When fabricating with dissimilar metals, Frigate uses optimized techniques such as TIG and MIG welding and precise heat control to prevent issues like cracking or poor fusion. Correct filler material selection and controlled heat input ensure that welds maintain the integrity and performance required for both metals, even in complex assemblies.
Frigate combines advanced finishing techniques, including precision laser cutting, deburring, and automated polishing, to achieve consistent surface finishes across all parts. By integrating these methods into the production process, Frigate ensures that each part meets the required aesthetic and functional standards, regardless of batch size, maintaining uniformity in appearance and performance.
Frigate implements predictive maintenance and tool monitoring systems to track wear patterns and optimize tool usage. Tools are replaced or adjusted by using advanced sensors and real-time data before they degrade performance, minimizing downtime. This proactive approach enhances productivity, ensuring continuous high-volume output without compromising the quality of sheet metal components.
Manufacturing Capability/Capacity
Ferrous casting
Mold size(max): 1m X 1m
Weight Range: 1 KG ~ 30 KGS
Mold size(max): 1.5m X 1.5m
Weight Range: 30 KG ~ 150 KGS
Mold size(max): 3m X 3m
Weight Range: 100 KG ~ 1000 KGS
Mold size(max): 500 MM X 500 MM
Weight Range: 0.250 KG ~ 20 KGS
Mold size(max): 500 MM X 500 MM
Weight Range: 0.100 KG X 20 KGS
Non-ferrous casting
Capacity: 5000 MT/a
Range of weight: 100 gm to 20 KGS
Mold size(max): 1 M X 1 M
Weight Range: 0.5 KG X 50 KGS
Mold size(max): 1 M X 1 M
Weight Range: 0.5 KG X 50 KGS
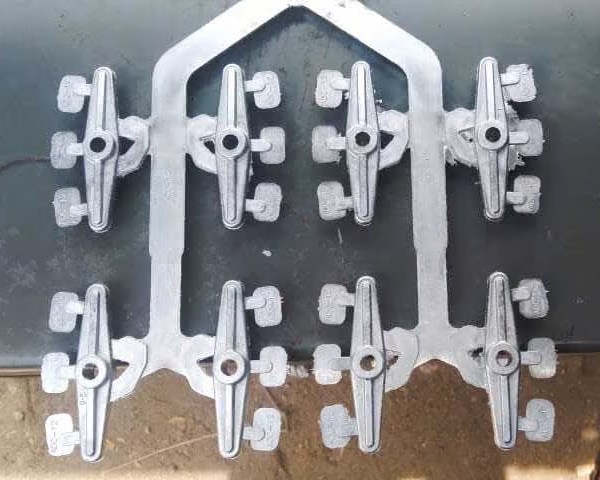
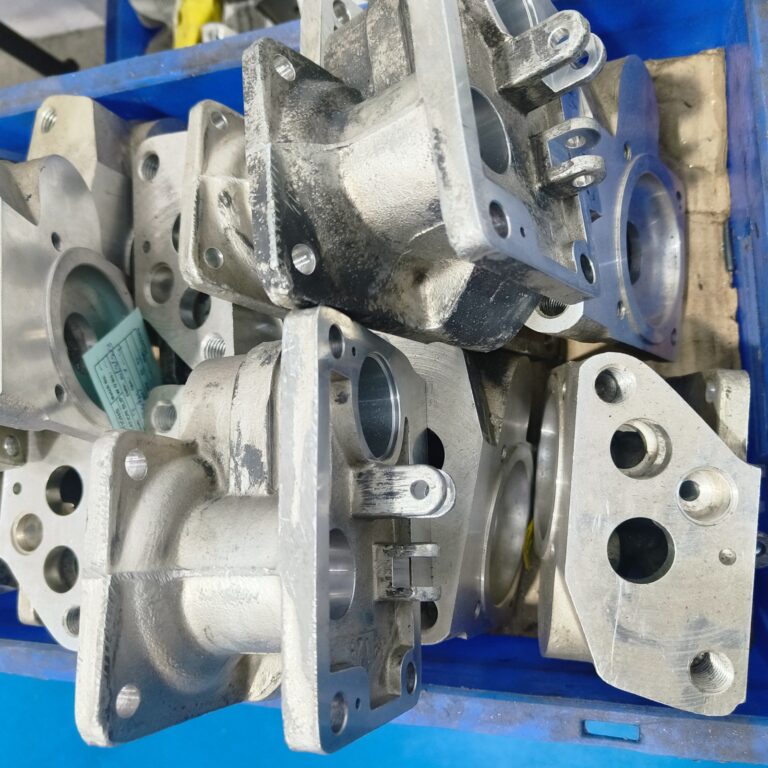
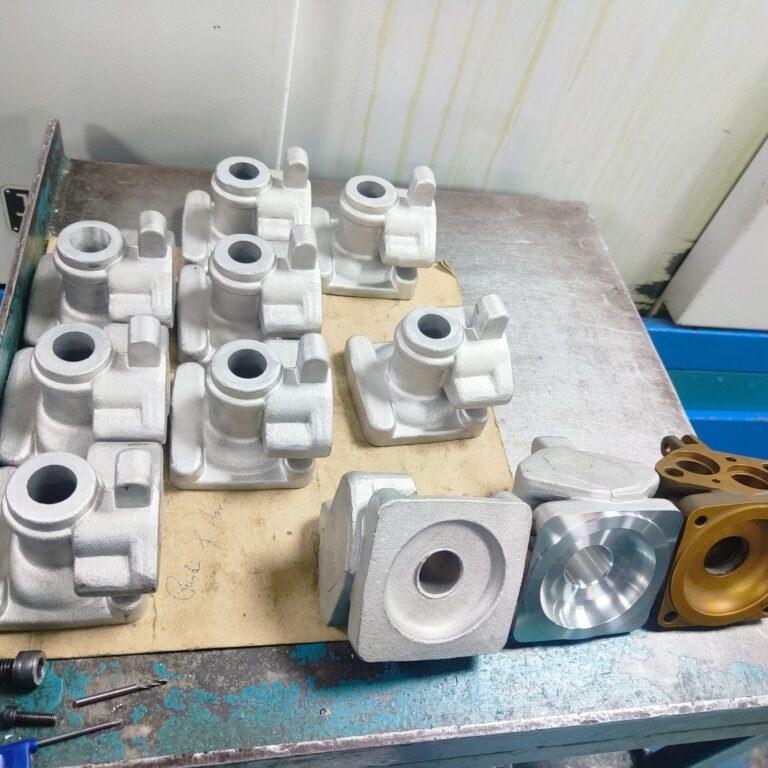
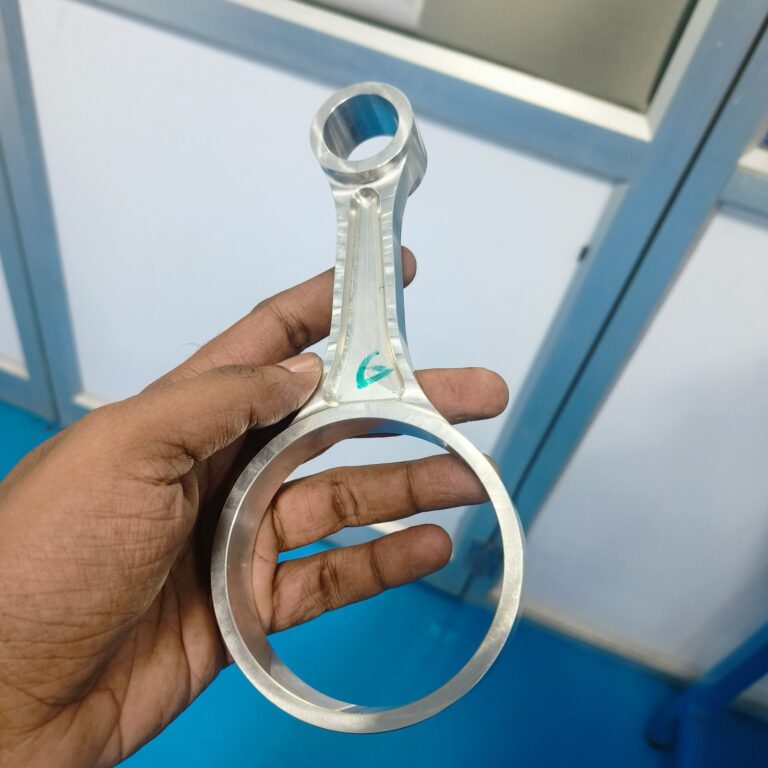
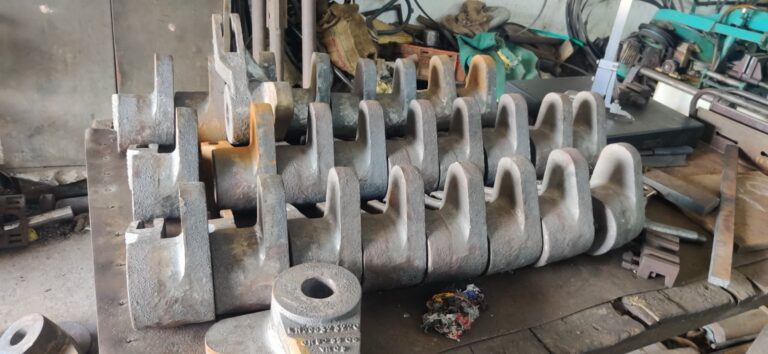
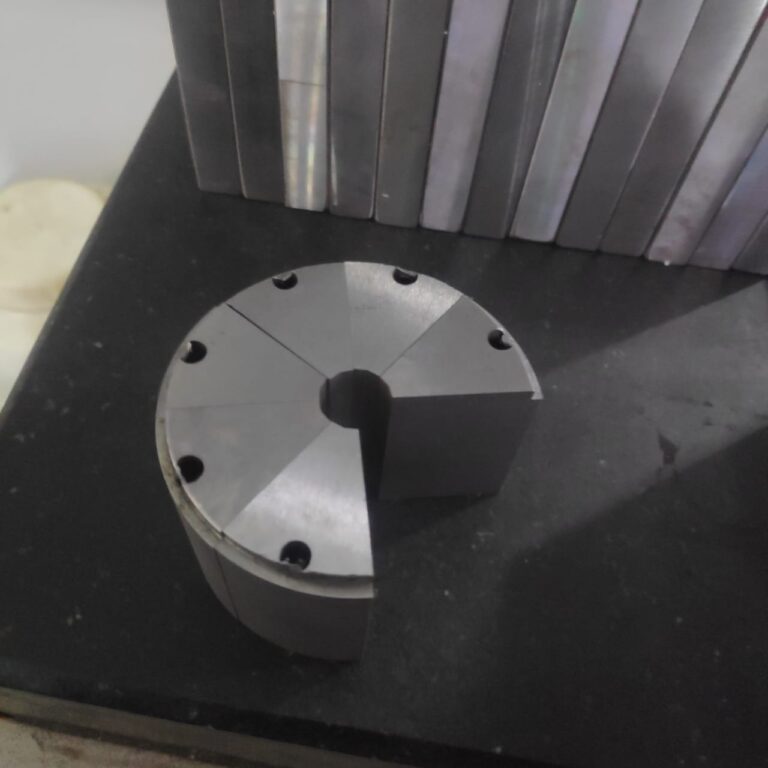
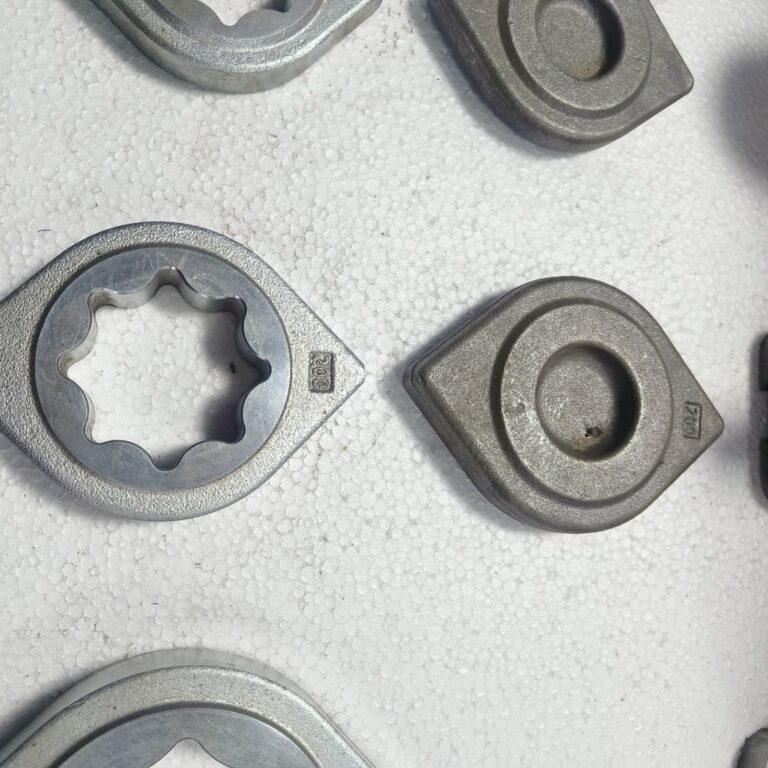
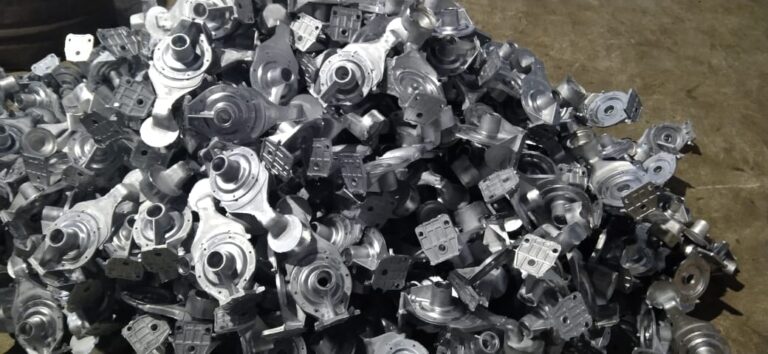
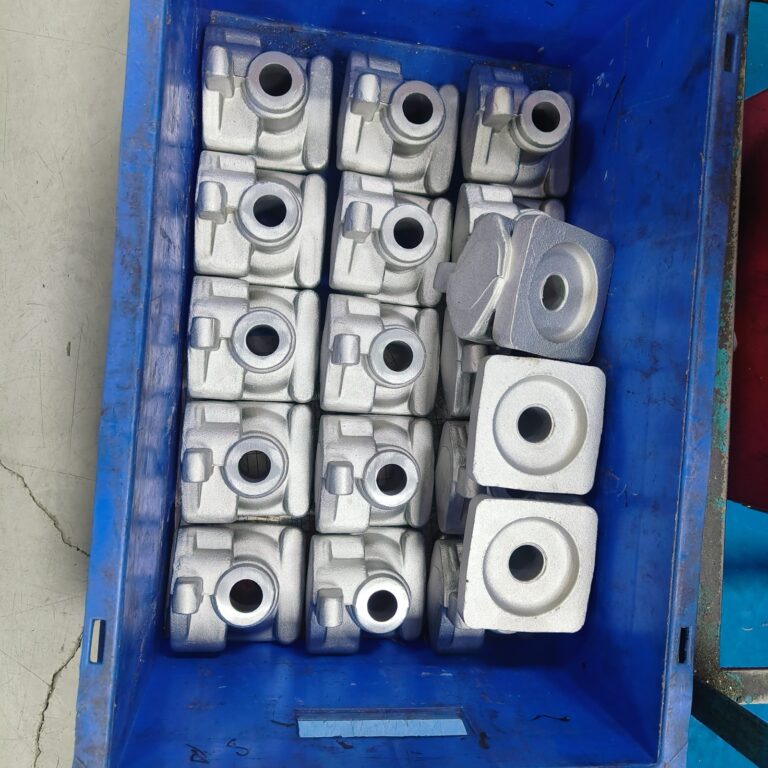
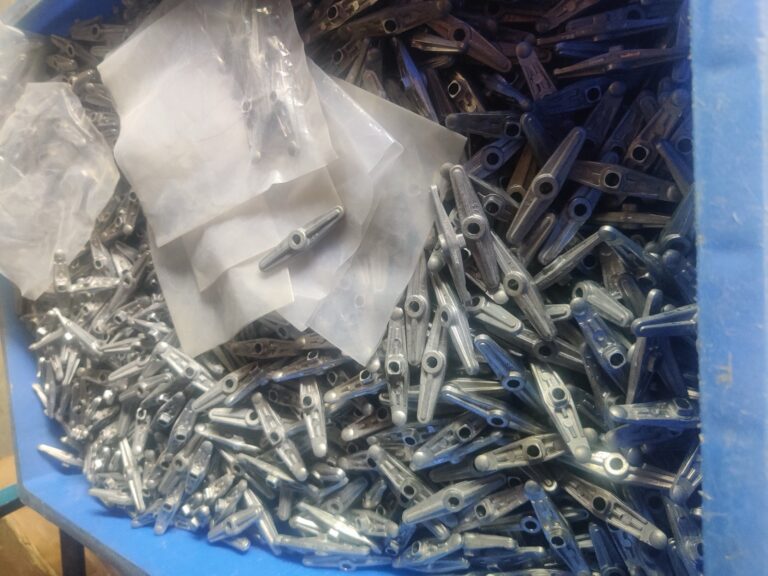
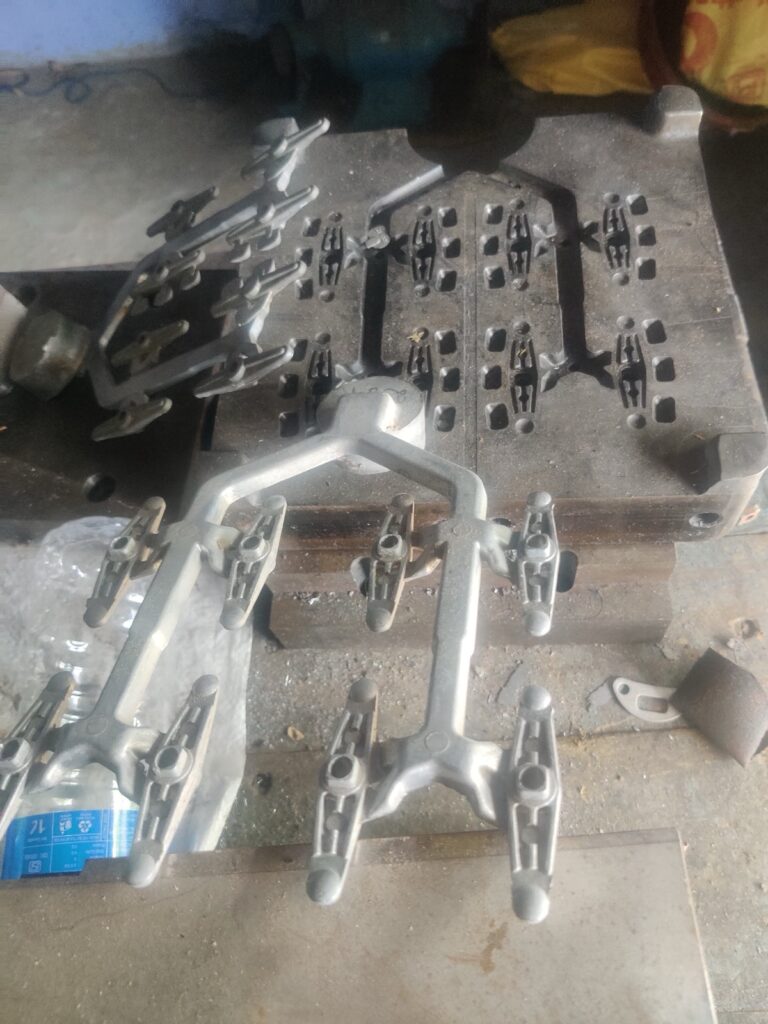
Forging
Capacity: 20,000 Tons per Annum
Range of weight: 300 KG to 1 Ton
Hammering: 5 Ton
Range of weight: 0.2 KG to 200 KGS
Hammering: 1600 Ton Hydraulic press
Ring size: 350 MM OD to 3000 MM OD
Range of weight: 15 KGS to 3200 KGS
Materials
Carbon Steel, Stainless Steel (AUSTENITE), Alloy Steel, Stainless Steel (MARTENSITE), etc.
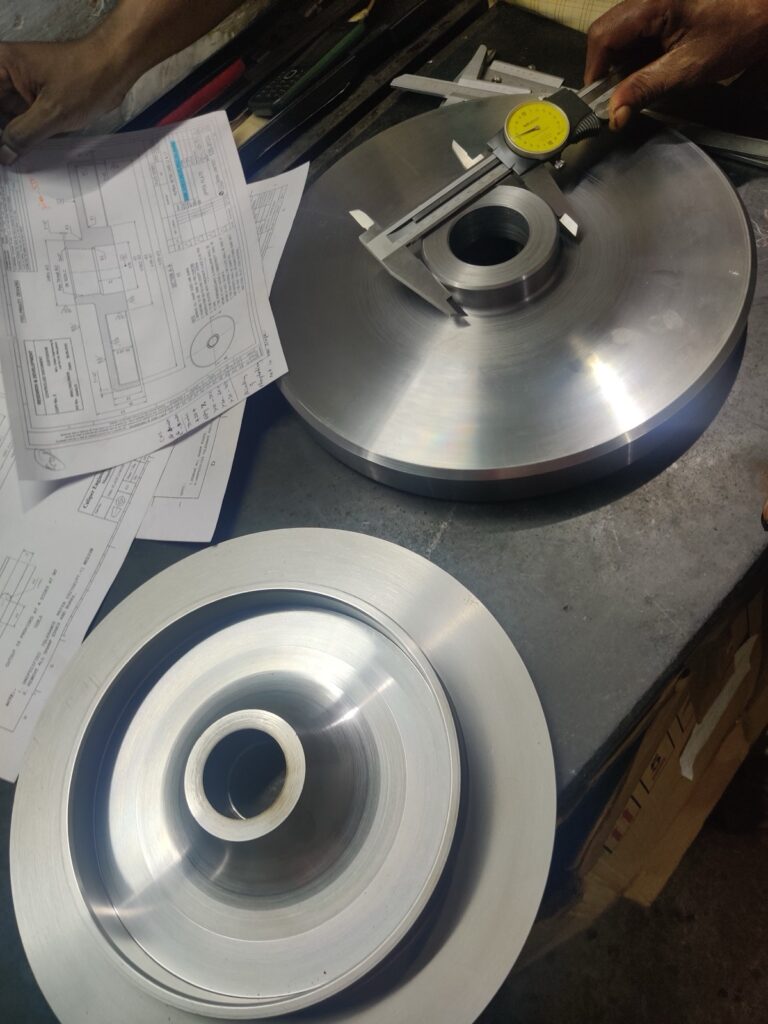
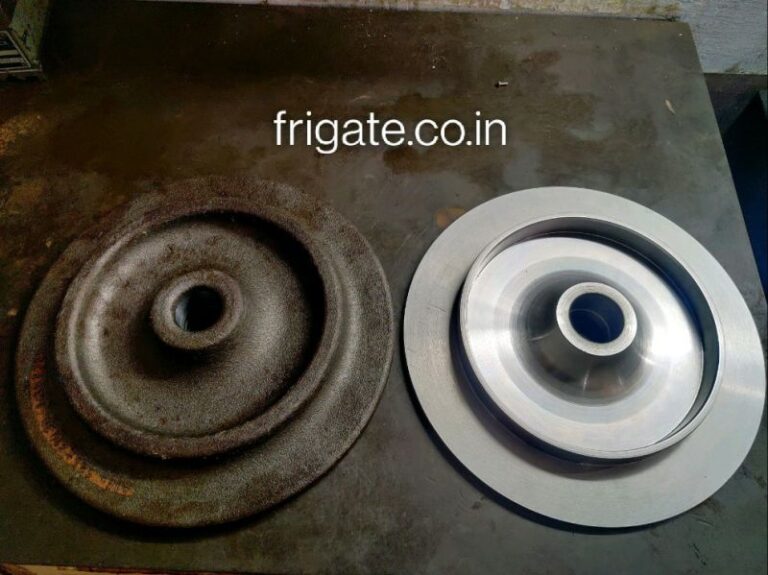
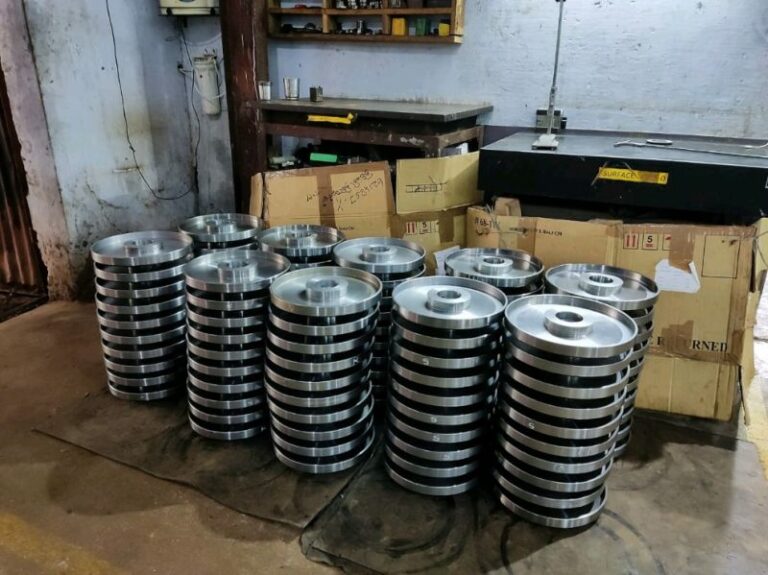
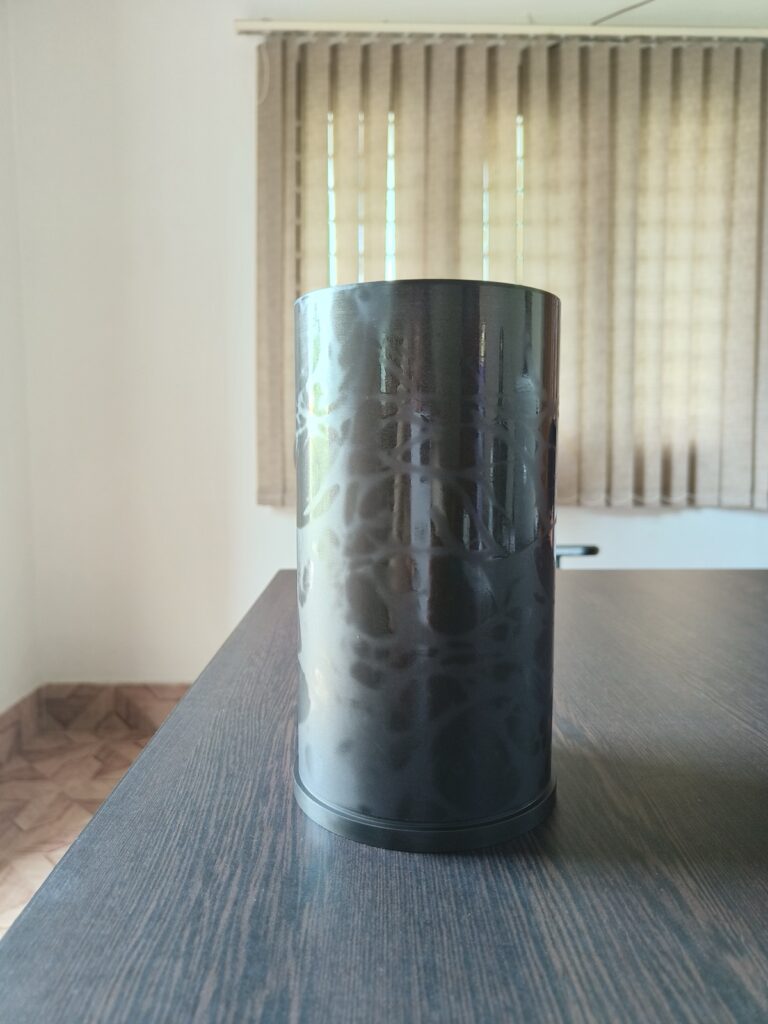
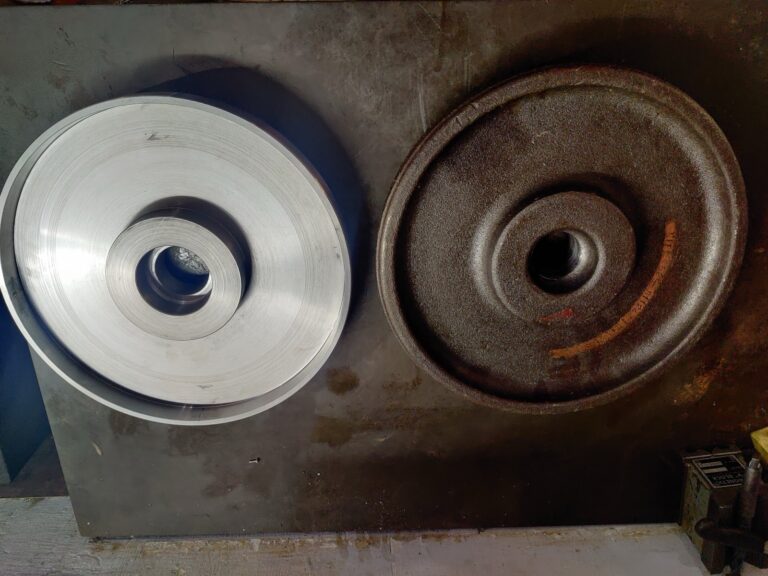
Machining
1 to 1000 MM
1 to 1000 MM
1 to 1000 MM
Materials
Steel, Aluminum, Brass, Copper, Titanium, Nickel Alloys, Tungsten Carbide, etc.
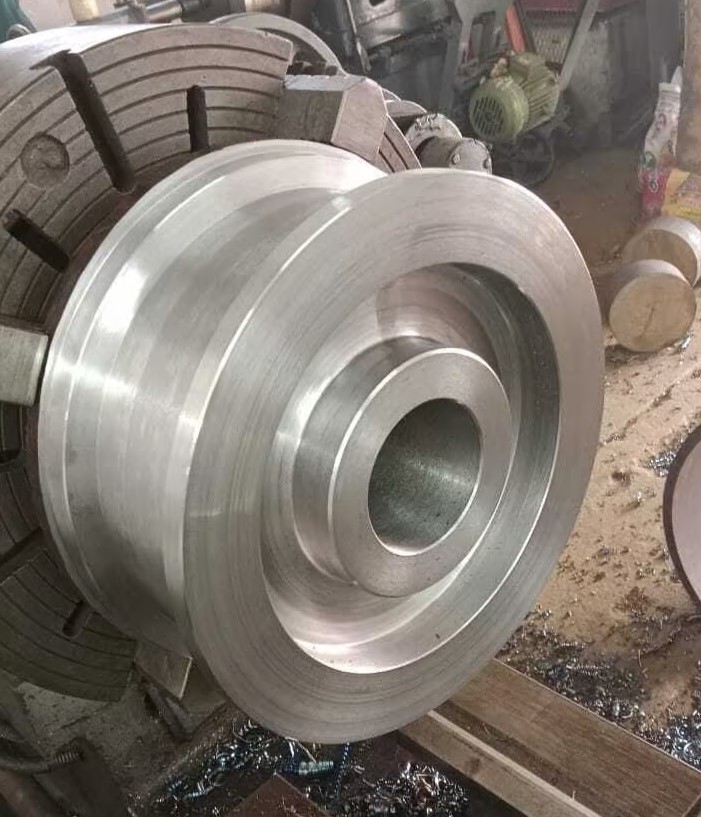
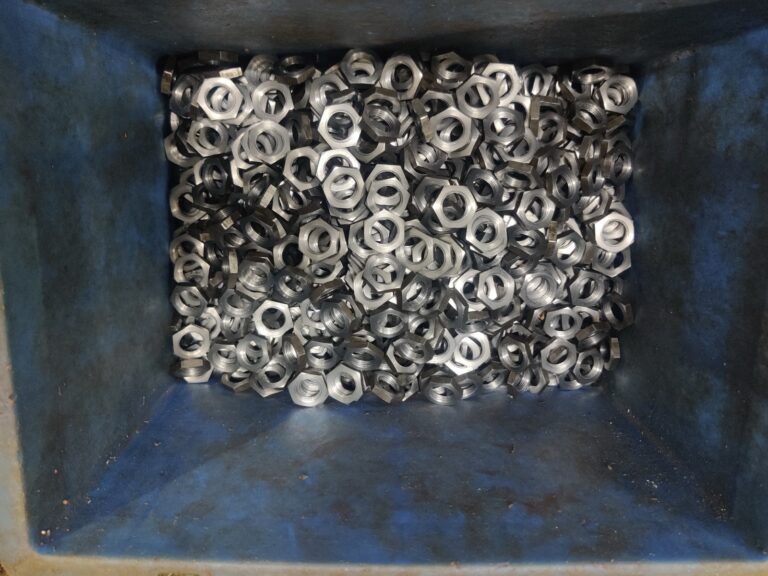
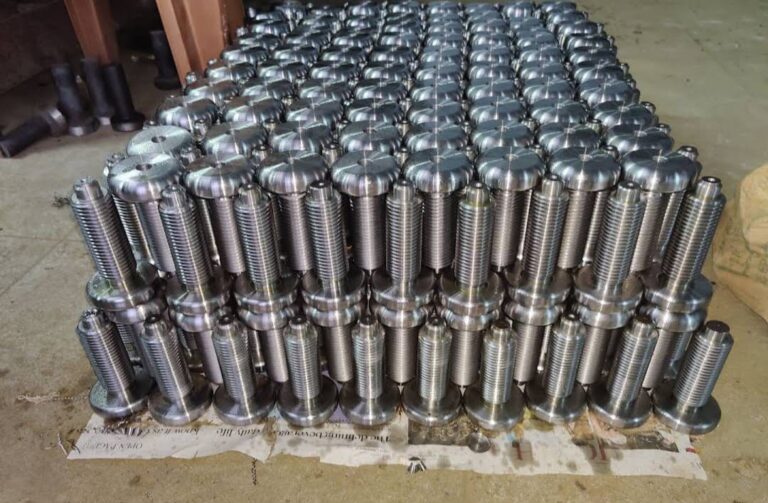
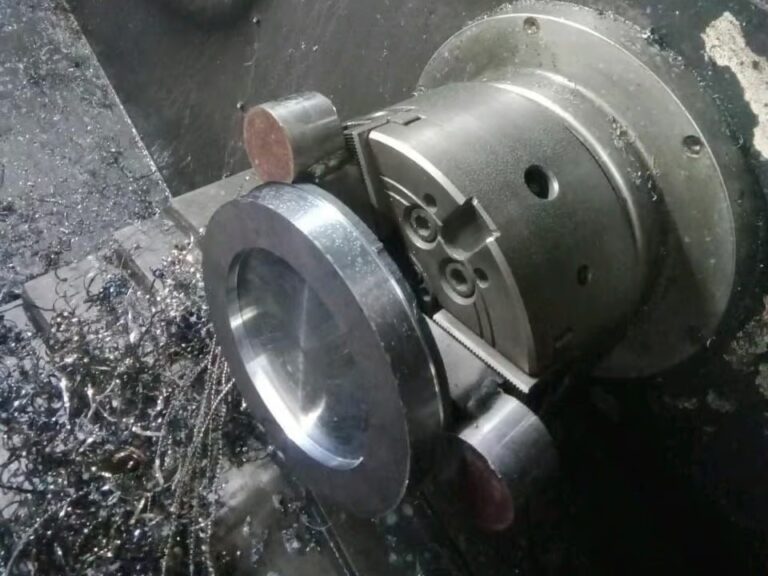
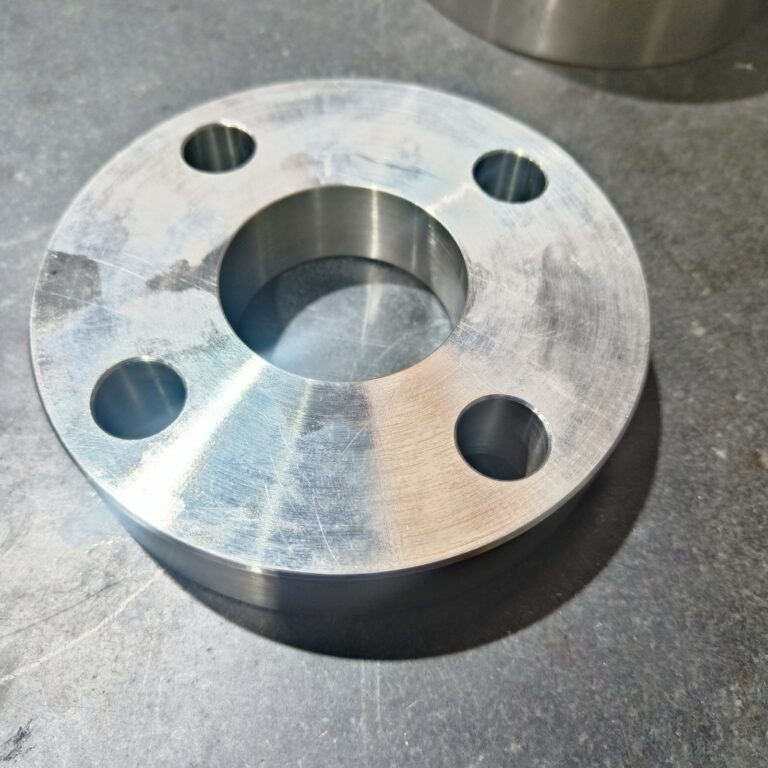
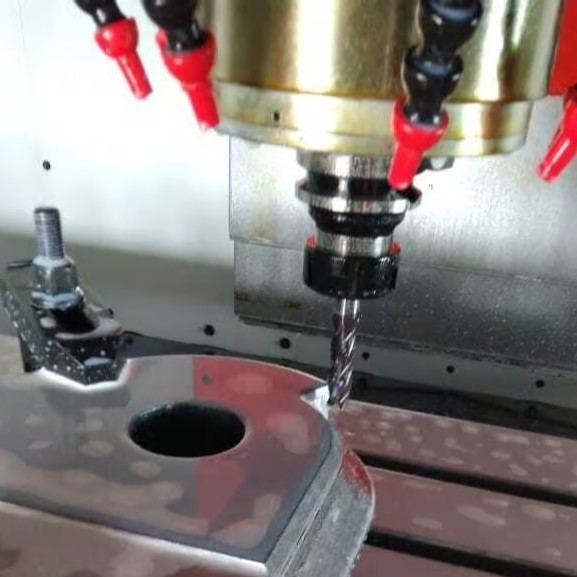
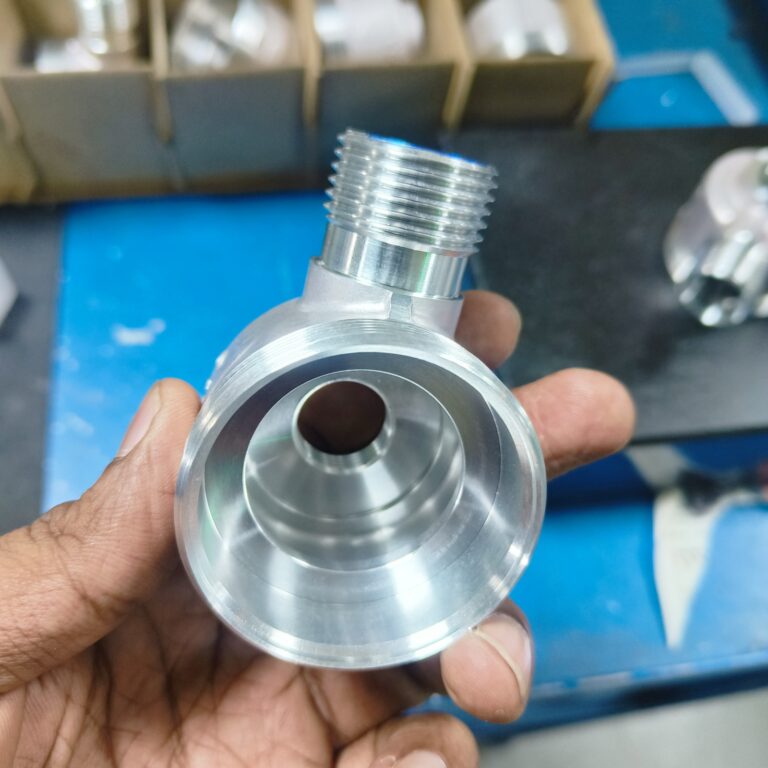
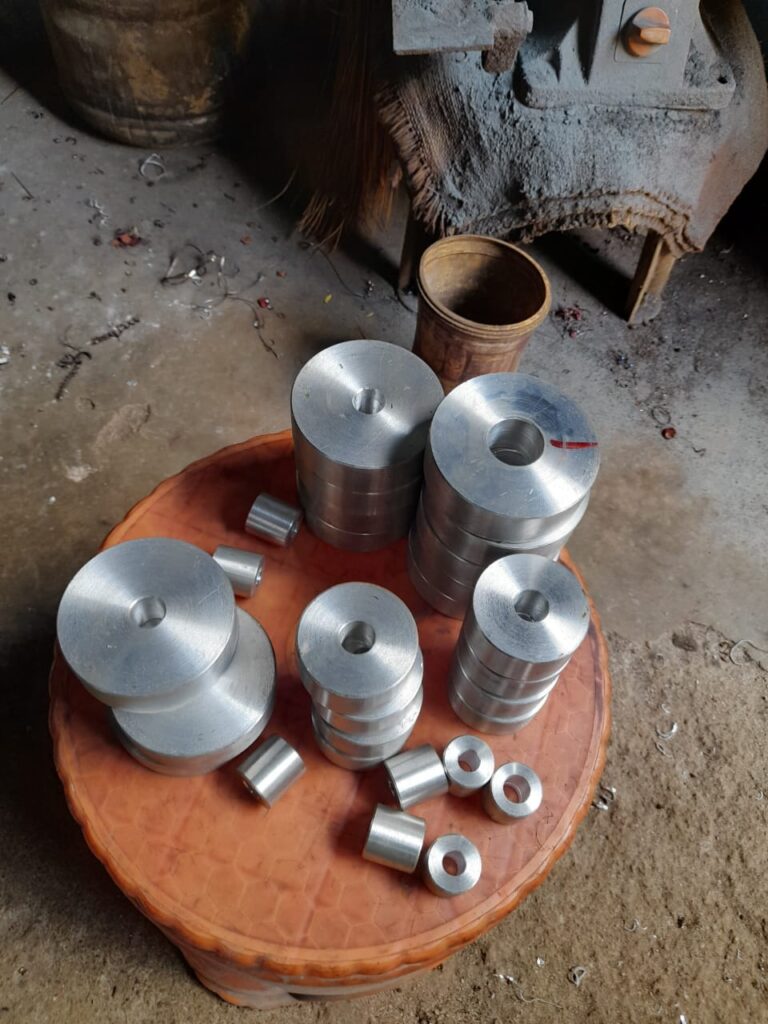
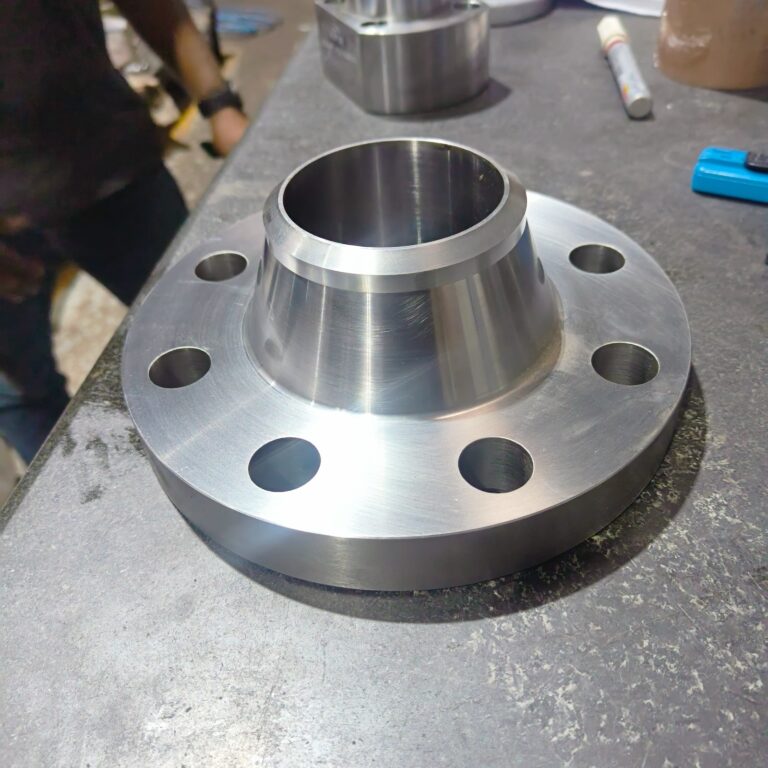
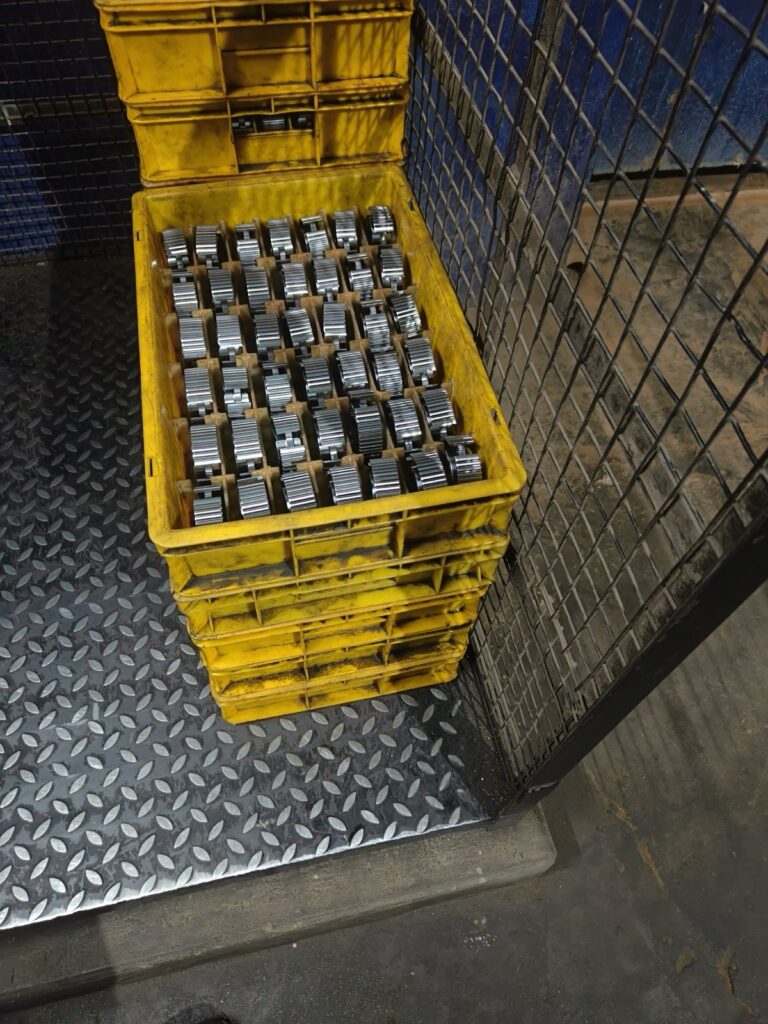
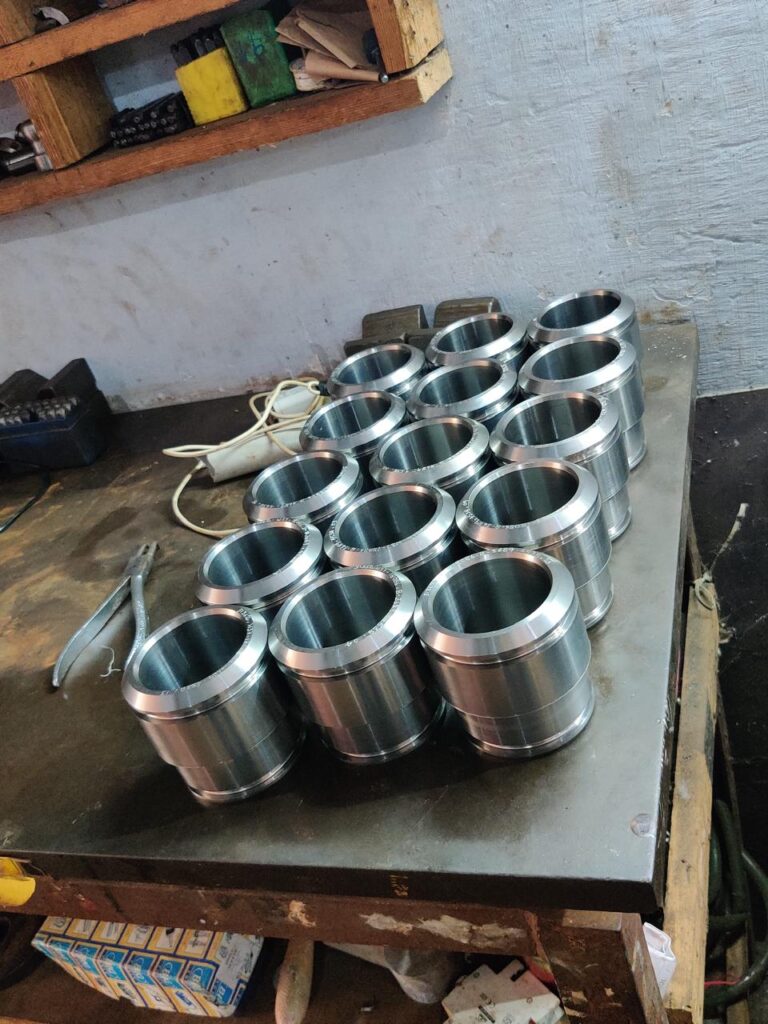
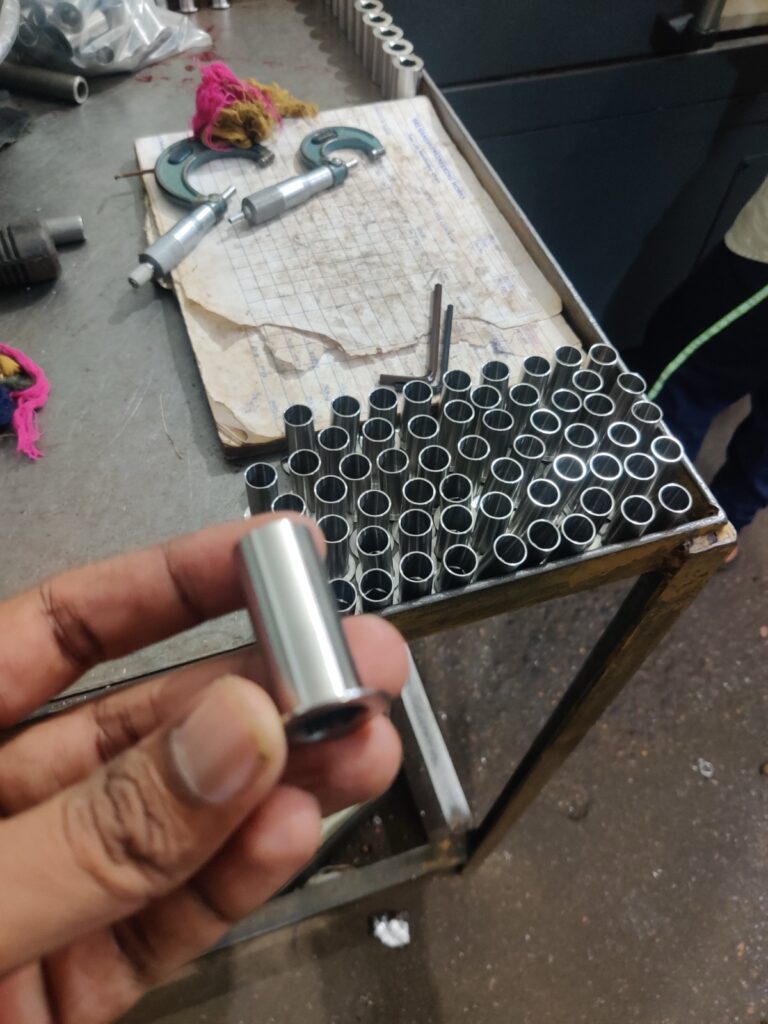
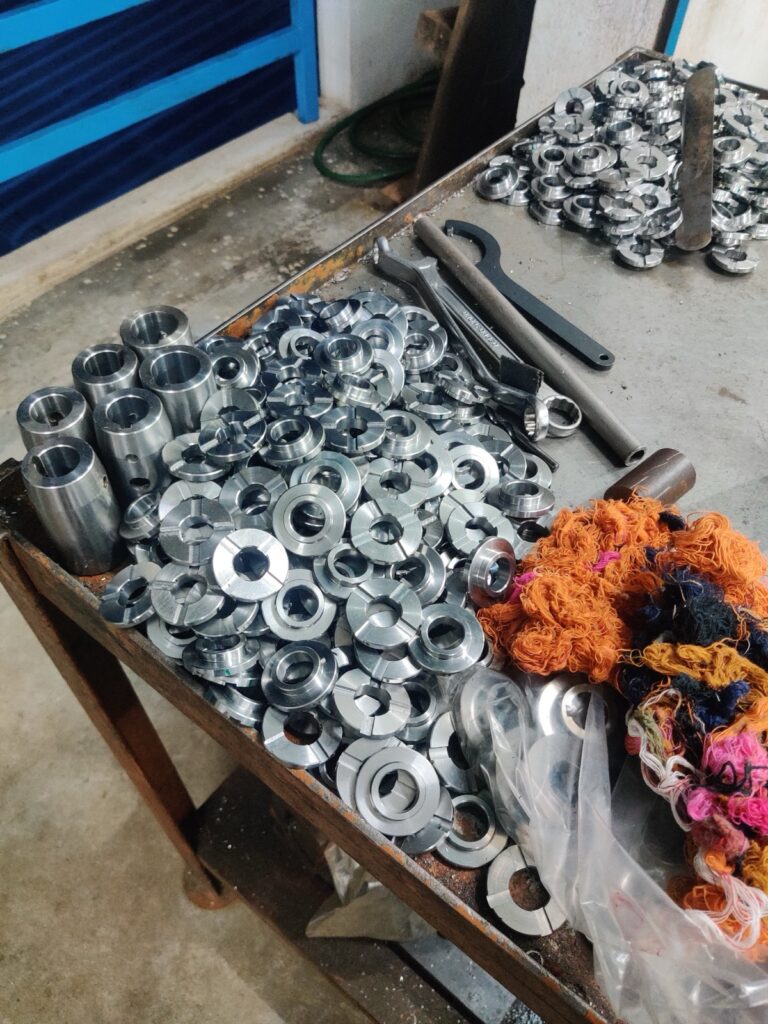
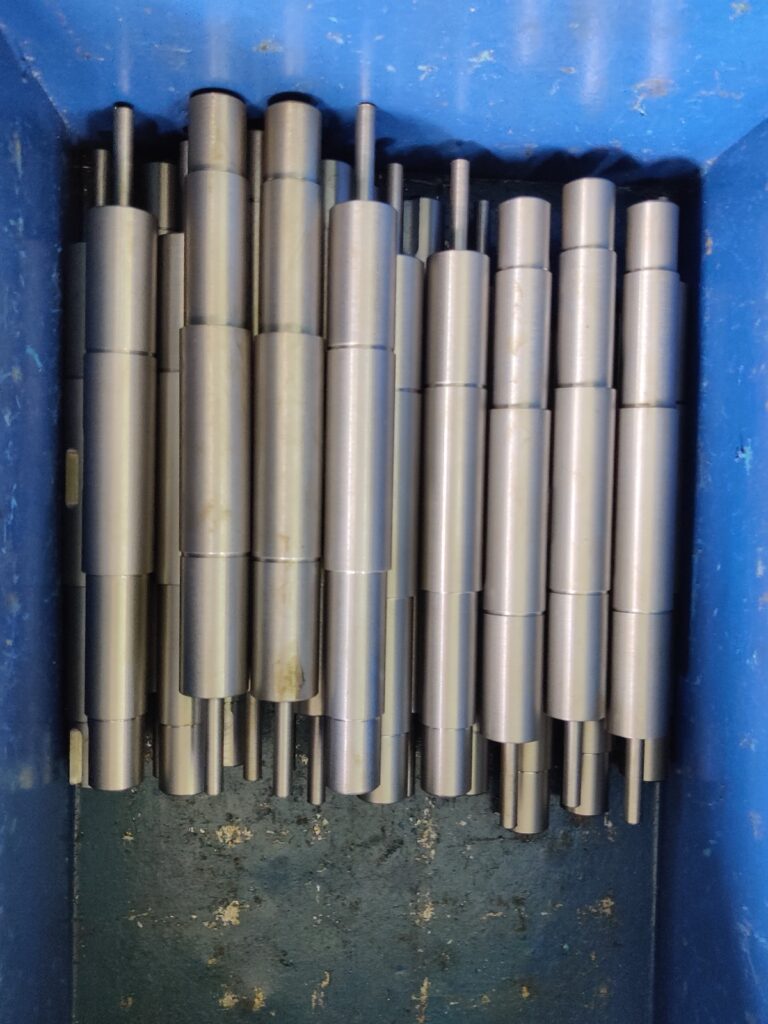
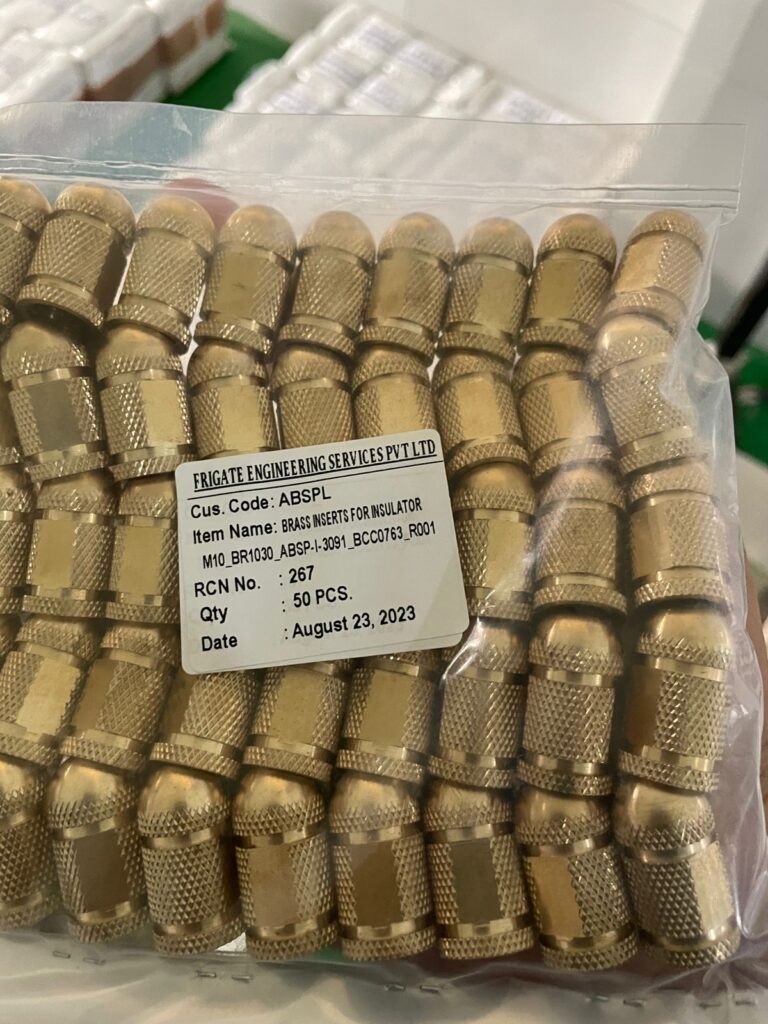
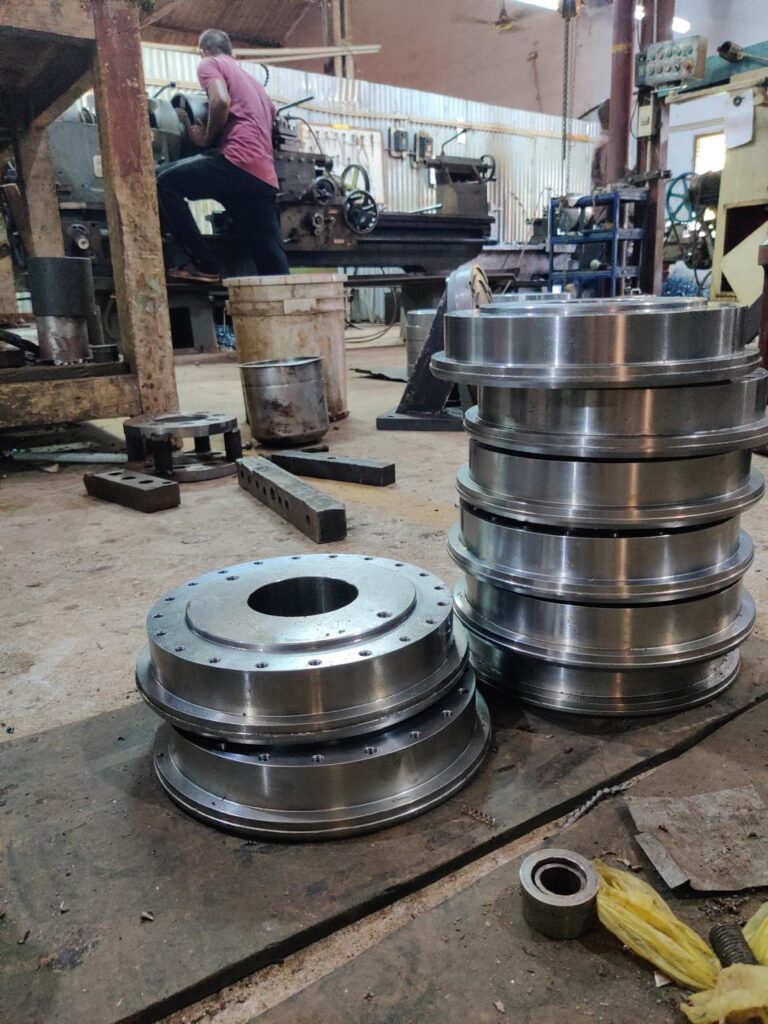
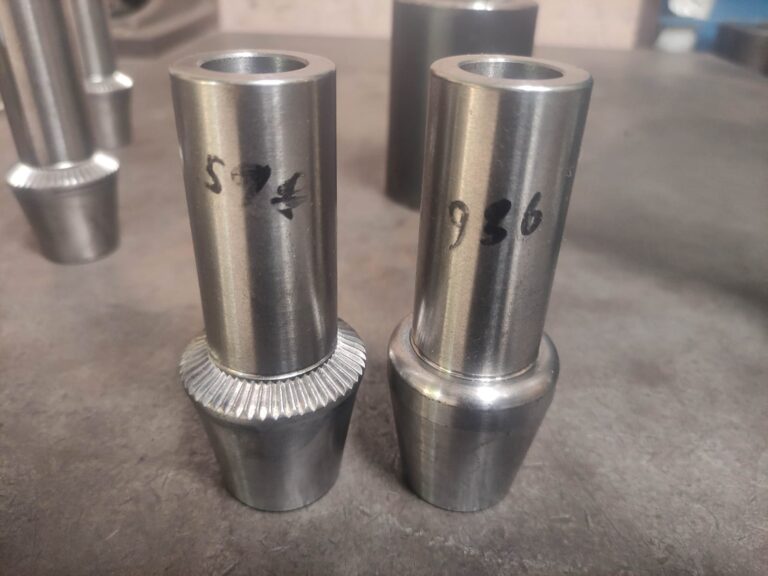
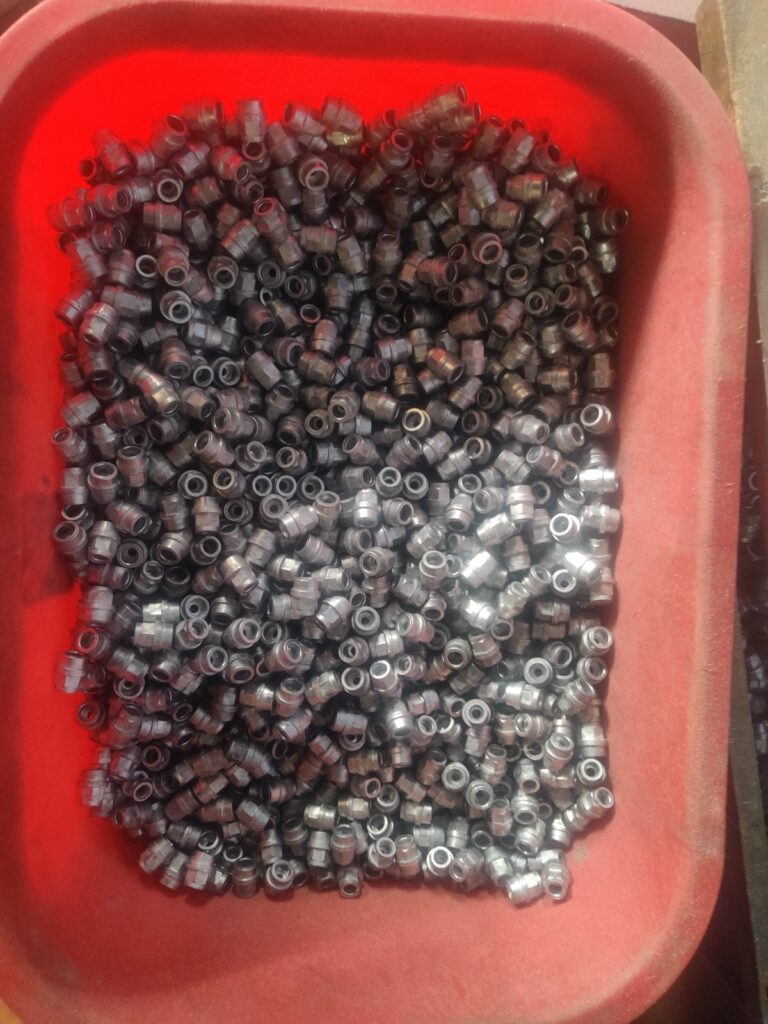
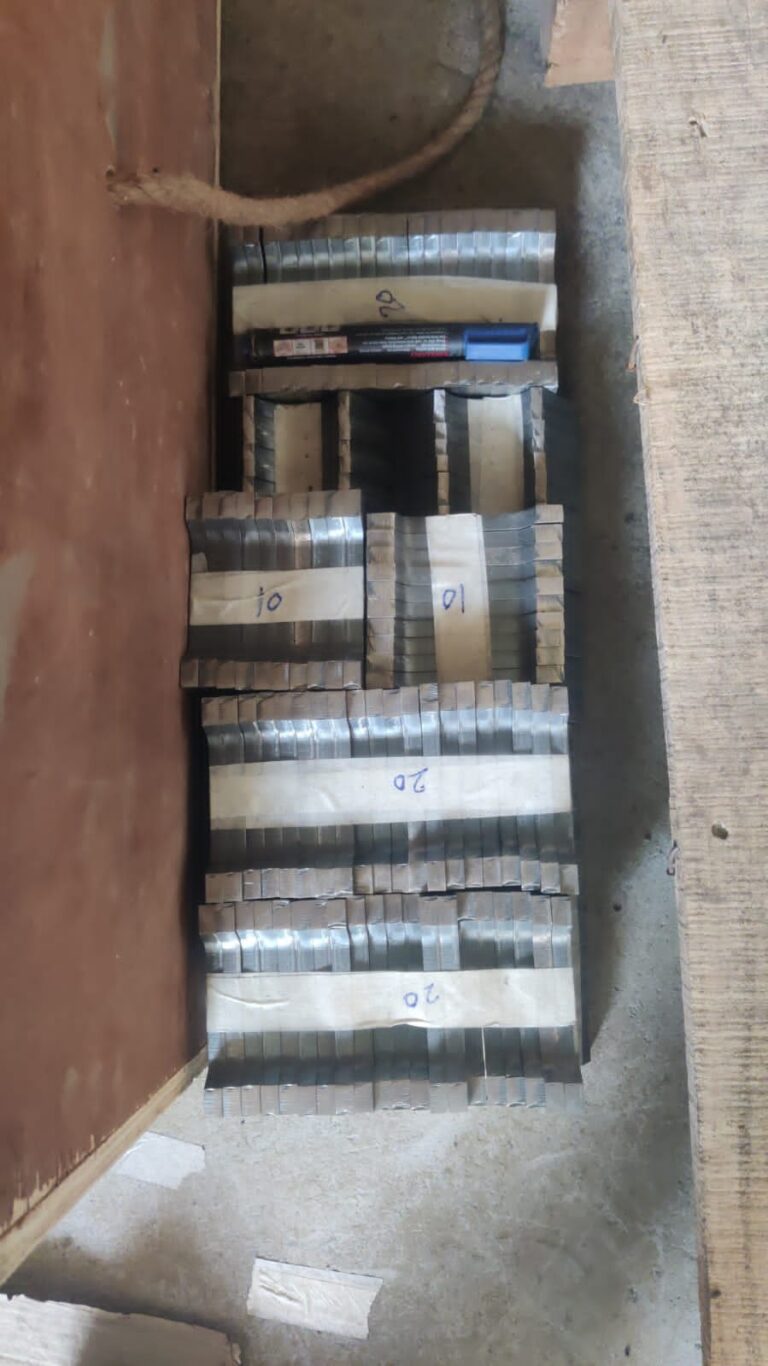
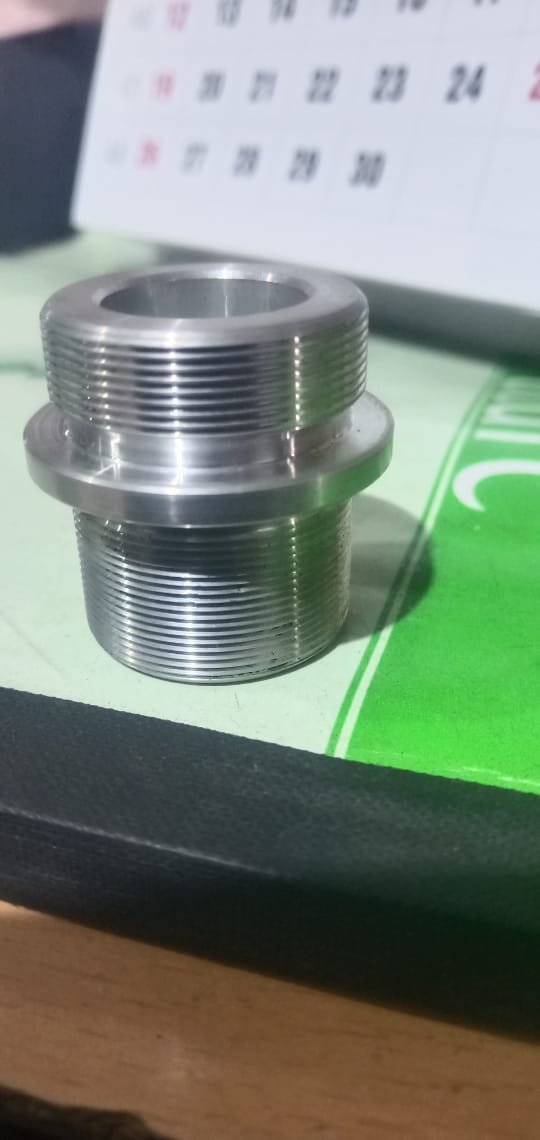
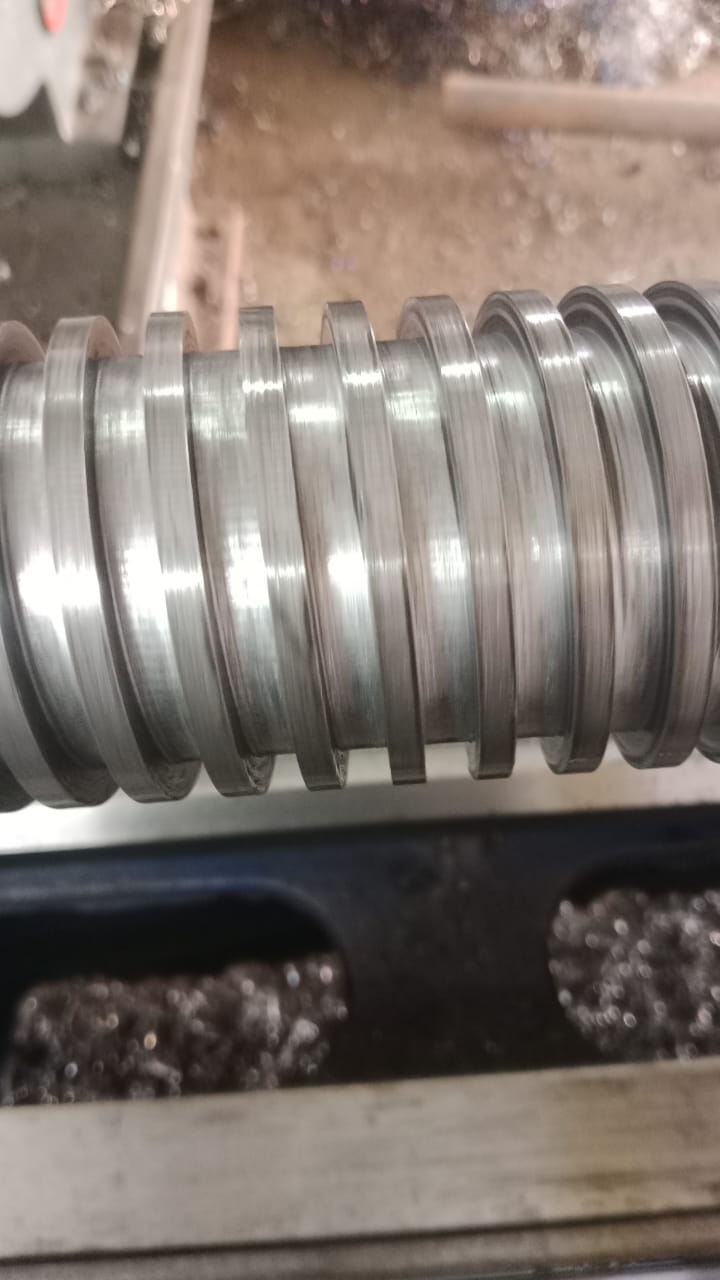
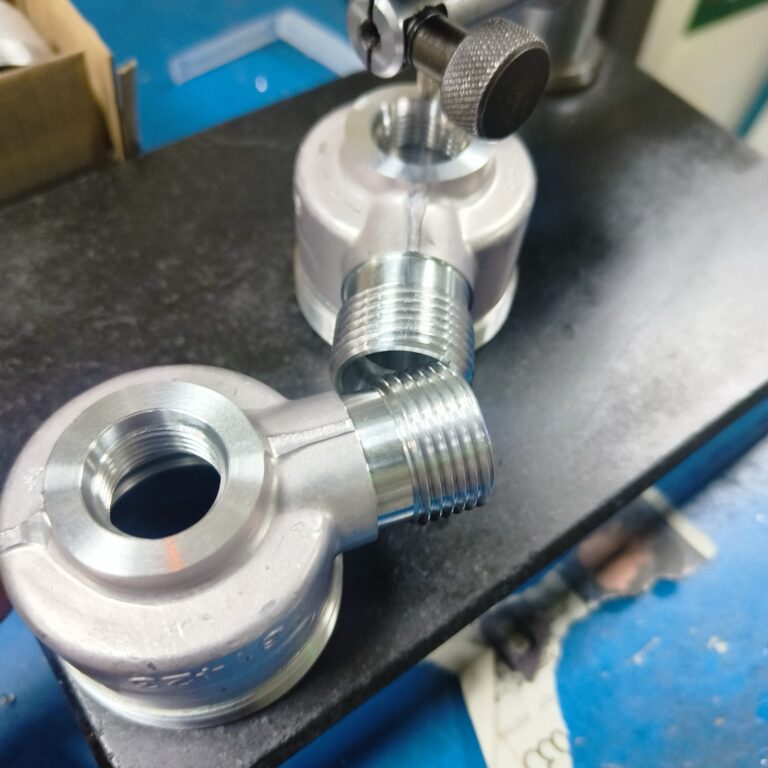
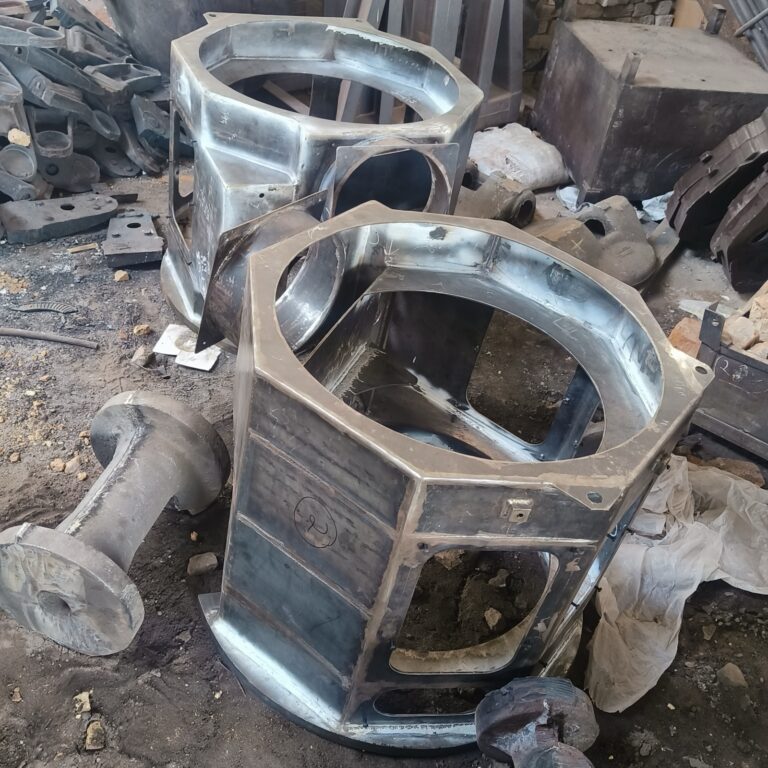
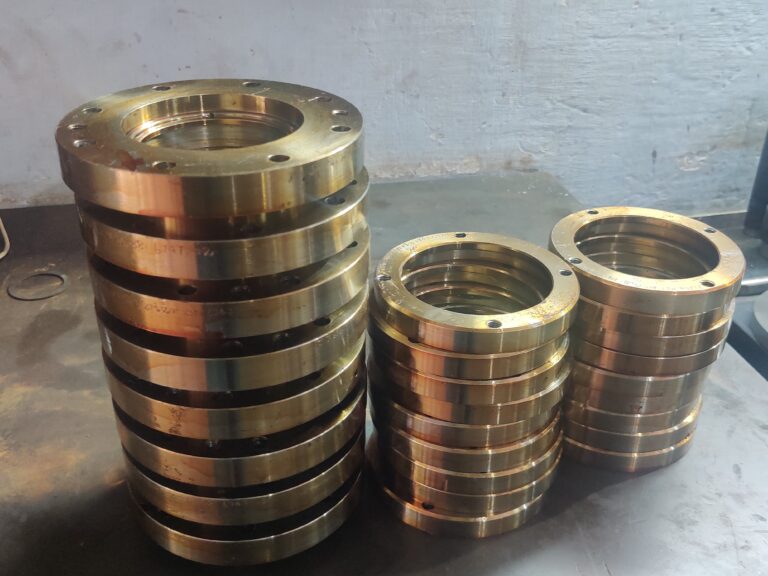
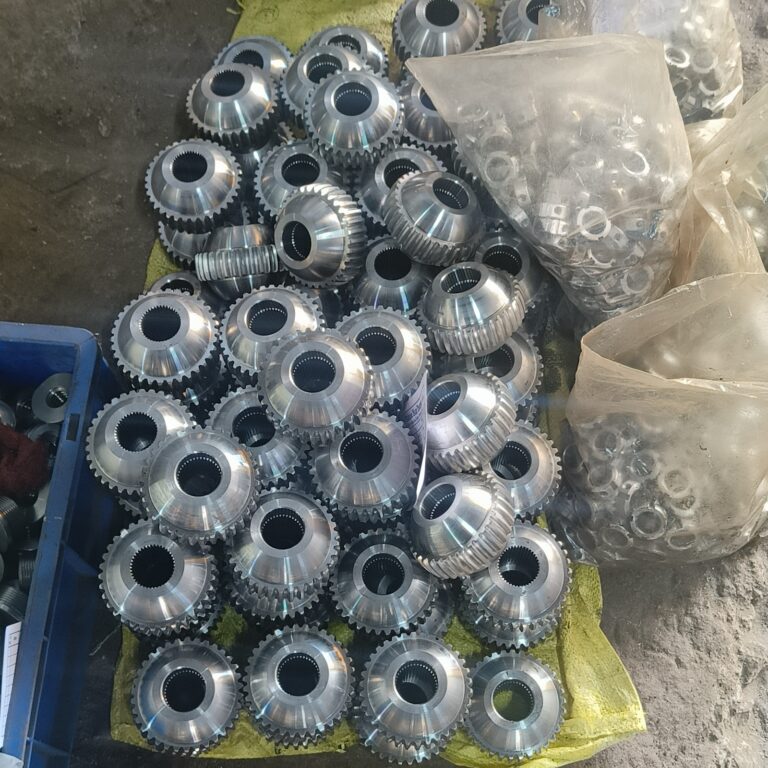
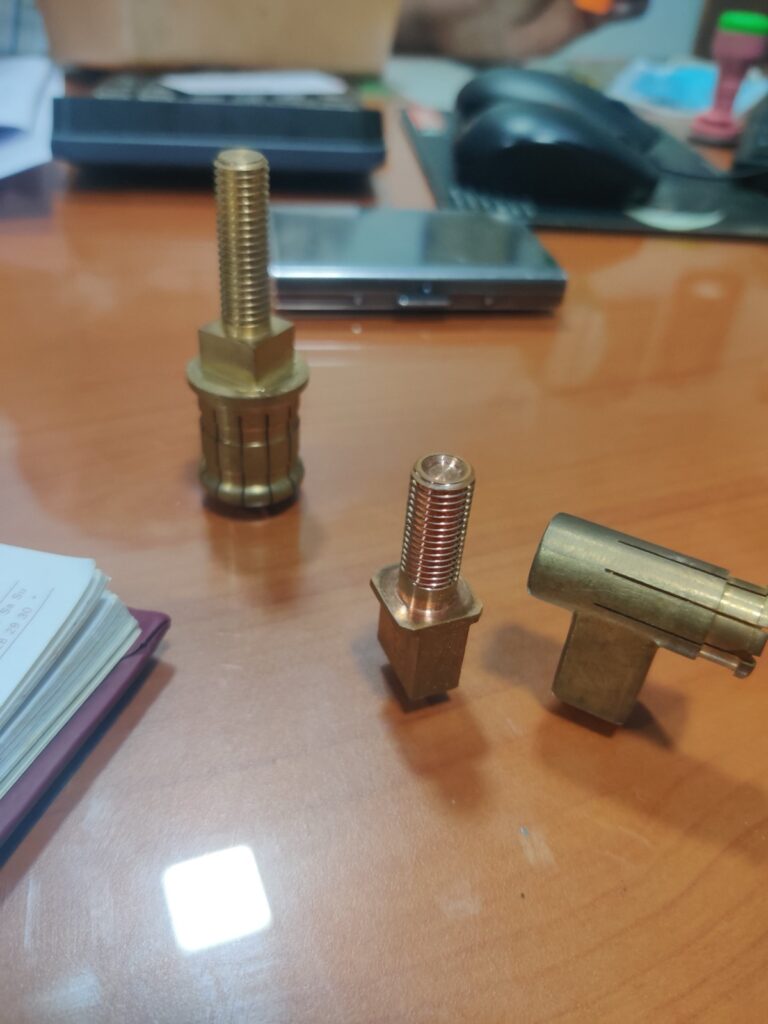
Plastics
Materials
1250 X 1250 MM
Within 10 microns
Engineering Plastics, Polyethylene, Polypropylene, Polyvinyl chloride, Polyethylene terephthalate, Bioplastics, etc.
Rubber
Materials
Natural rubber, Styrene-Butadiene Rubber, Nitrile Butadiene Rubber, Silicone Rubber, Fluorocarbon Rubber, Recycled Rubber, etc.
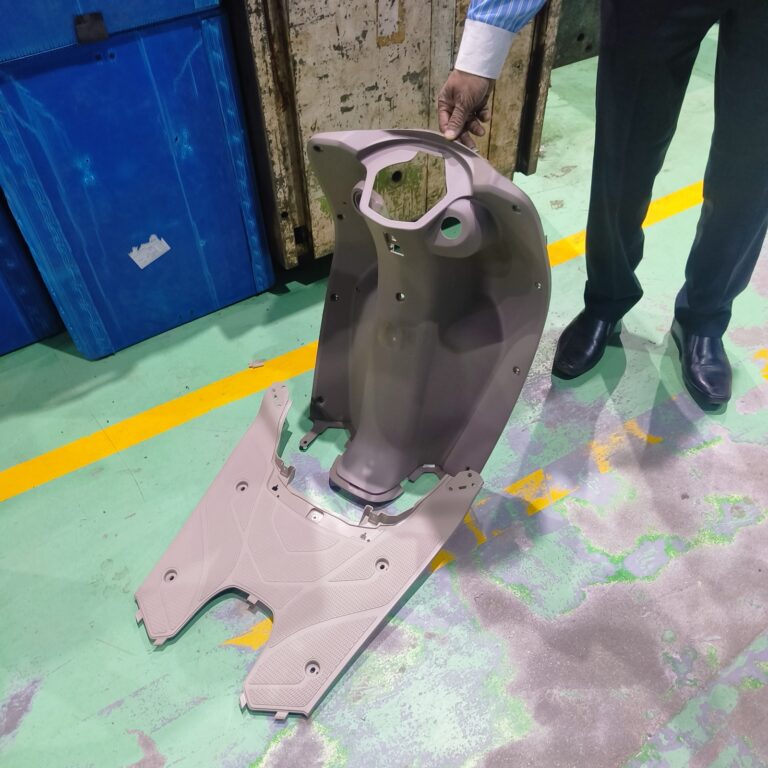
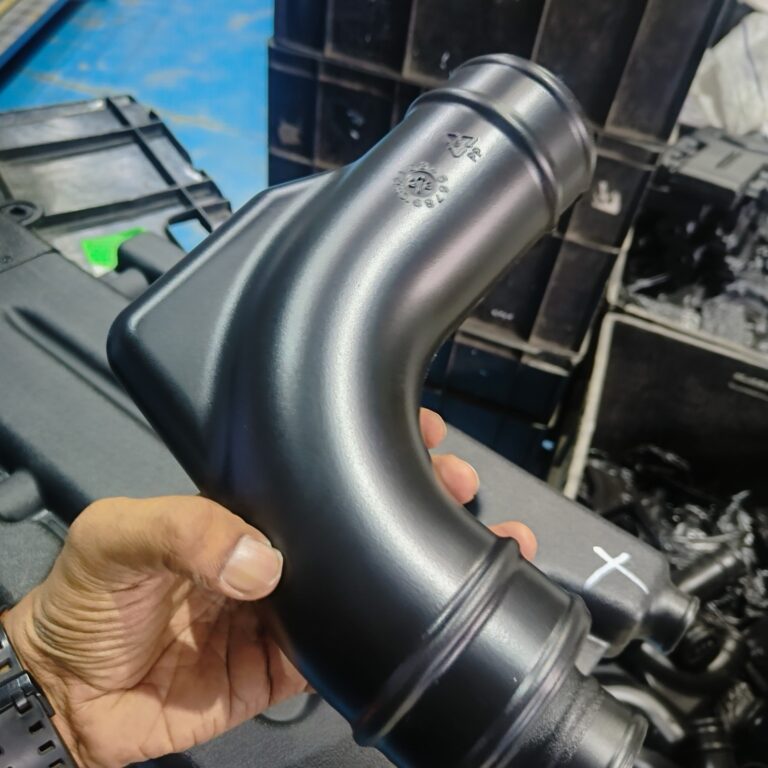
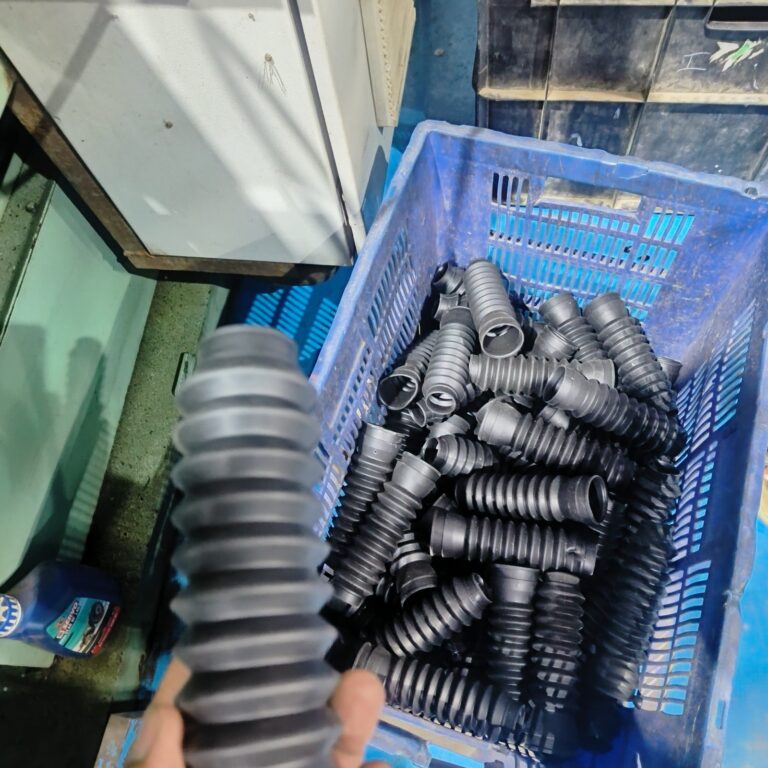
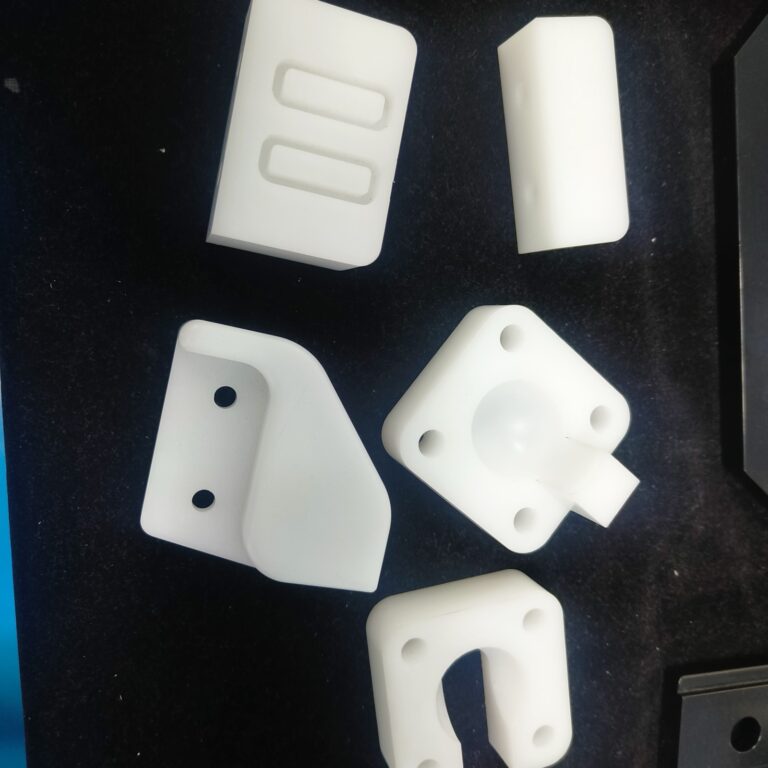
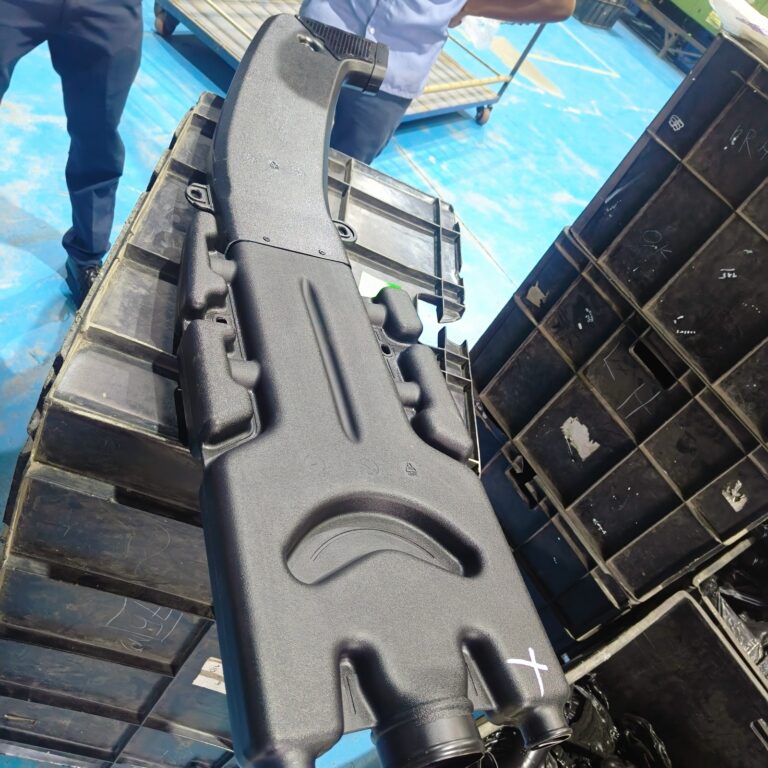
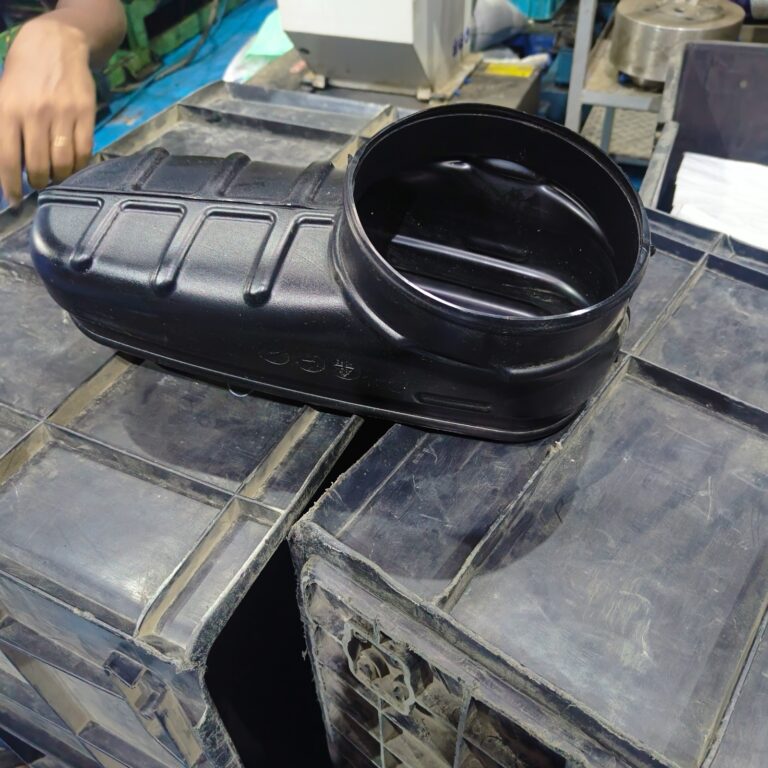
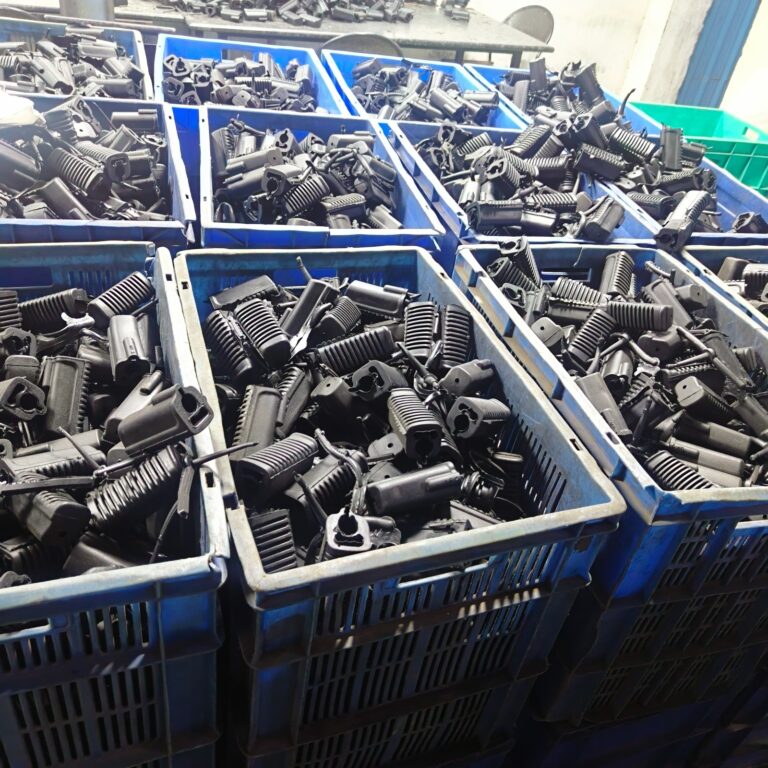
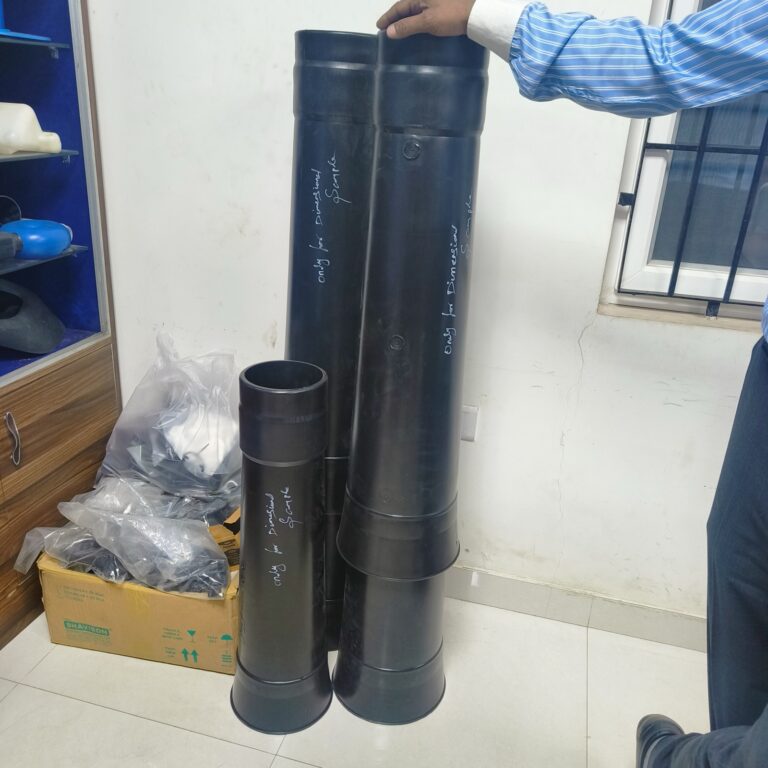
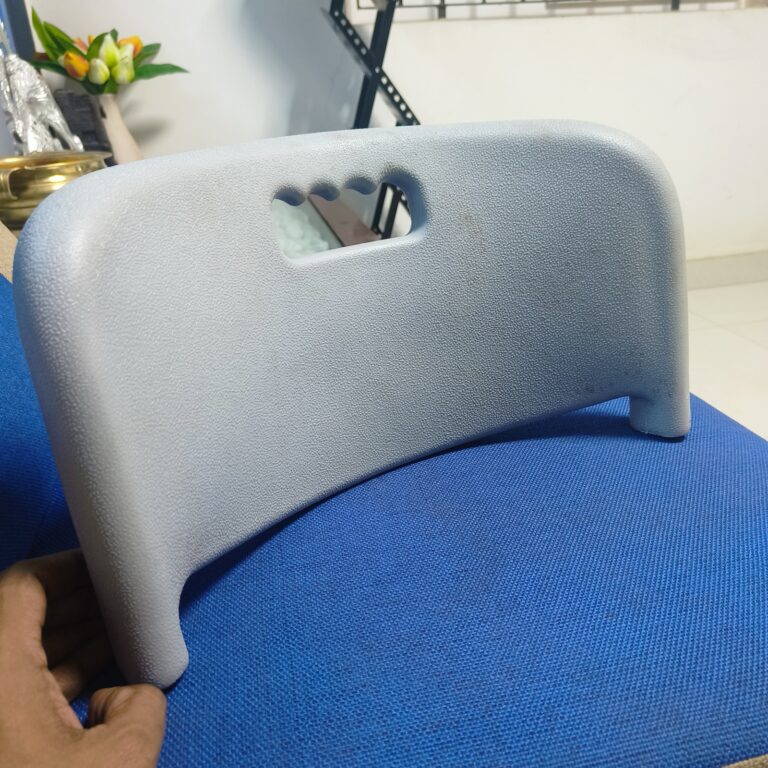
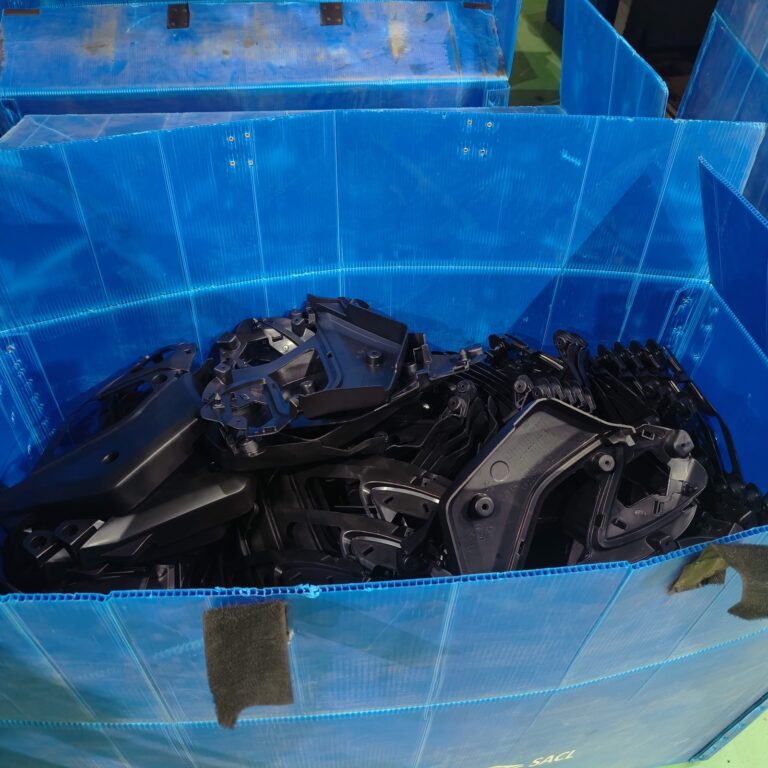
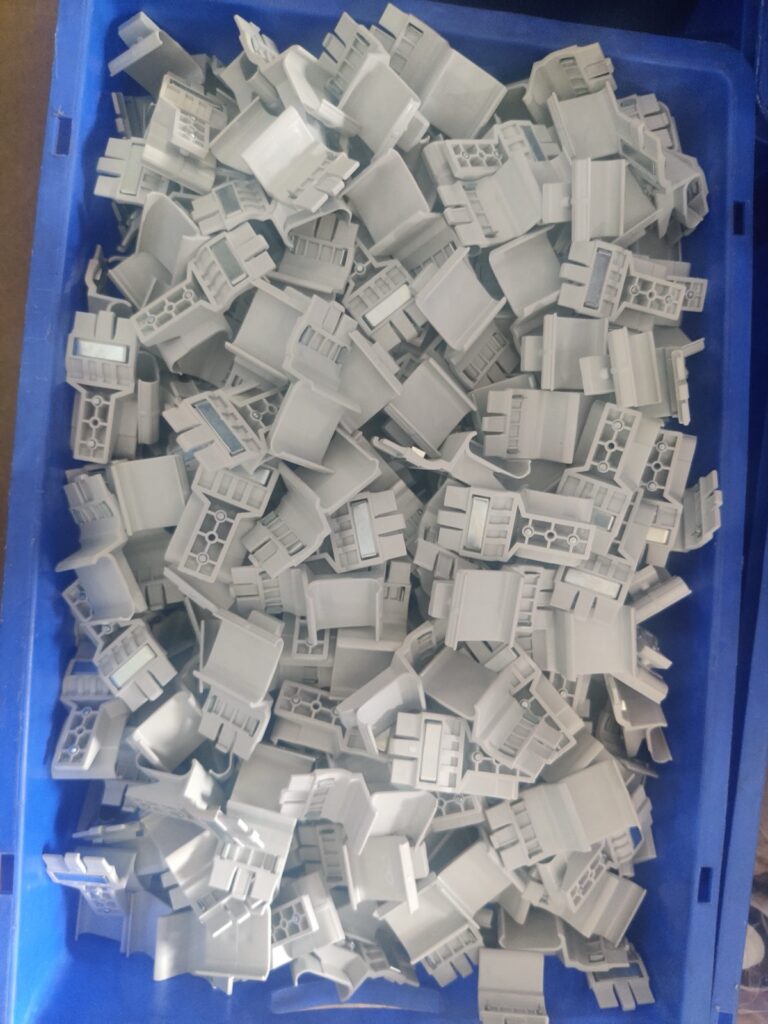
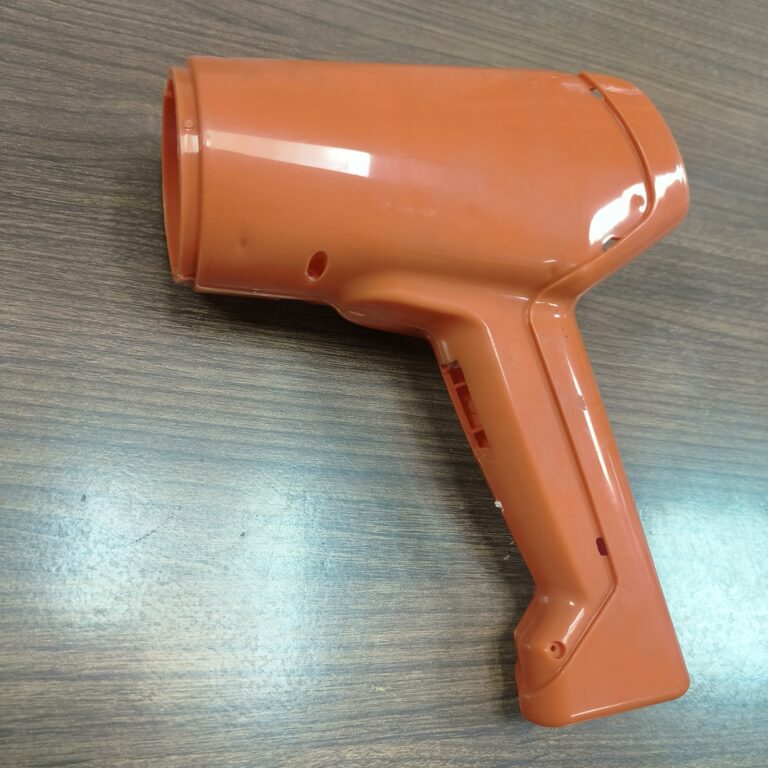
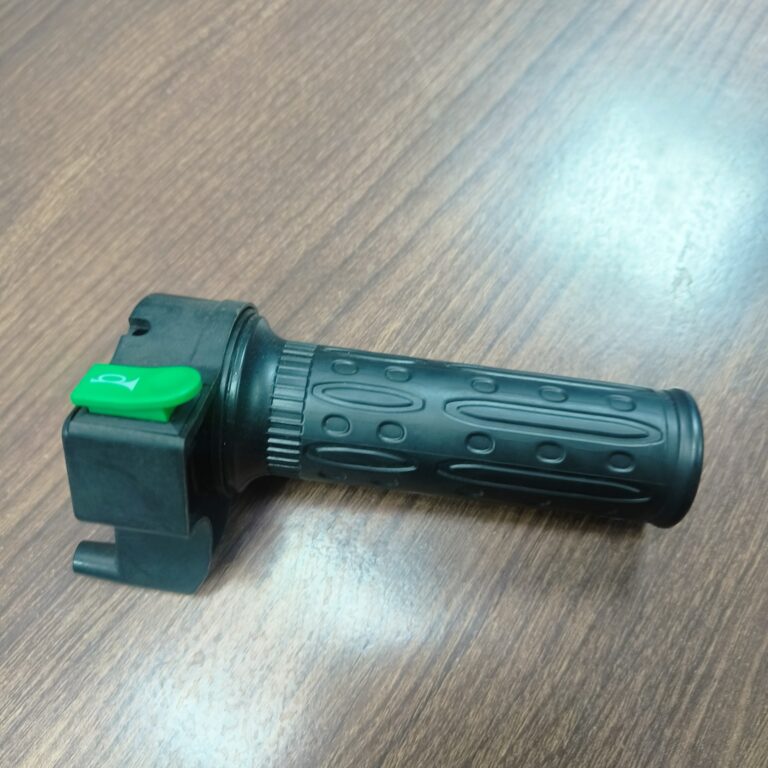
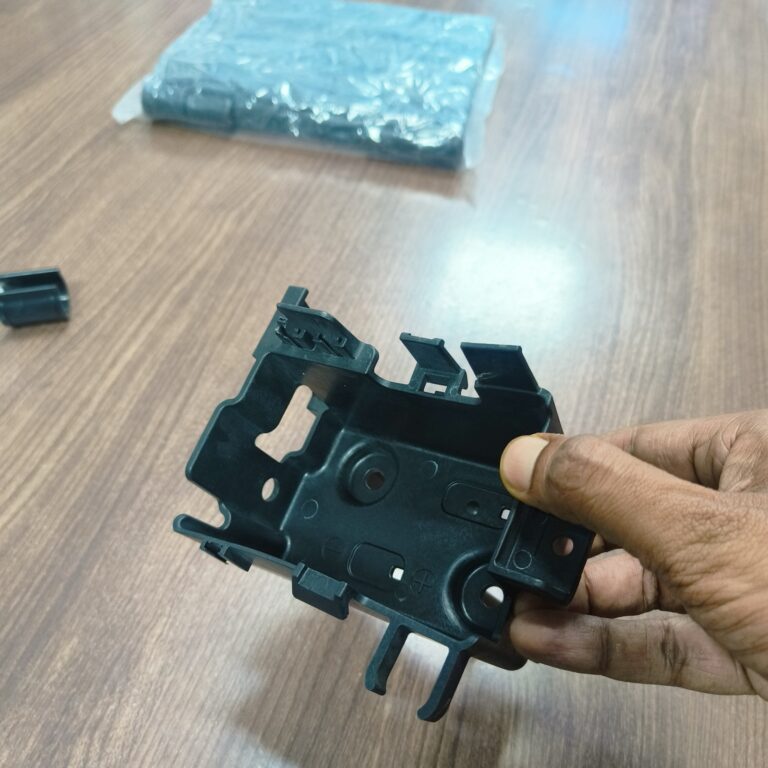
Heavy Fabrication
24000 MT/a
Materials
CS / MS, Alloy steel, Stainless Steel, etc.
Sheet Metal Fabrication
0.8 to 25 mm
Materials
Mild Steel, Stainless Steel, Aluminum, Brass, Copper, etc.


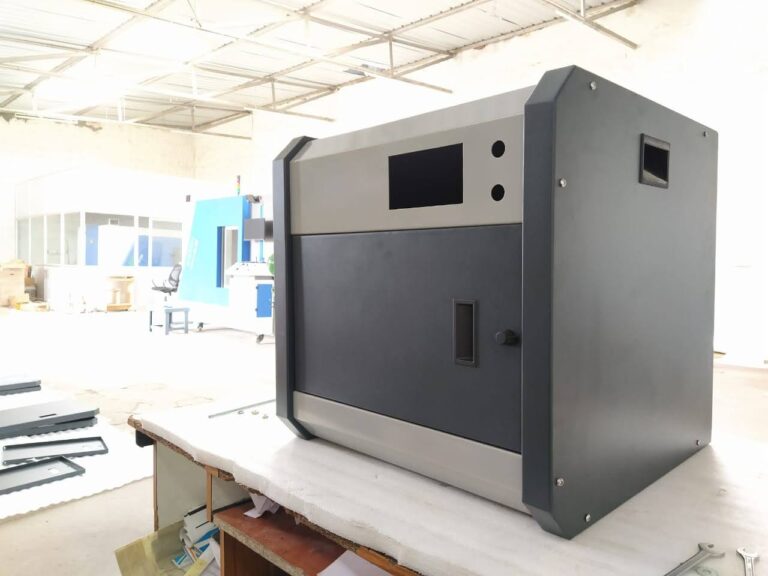


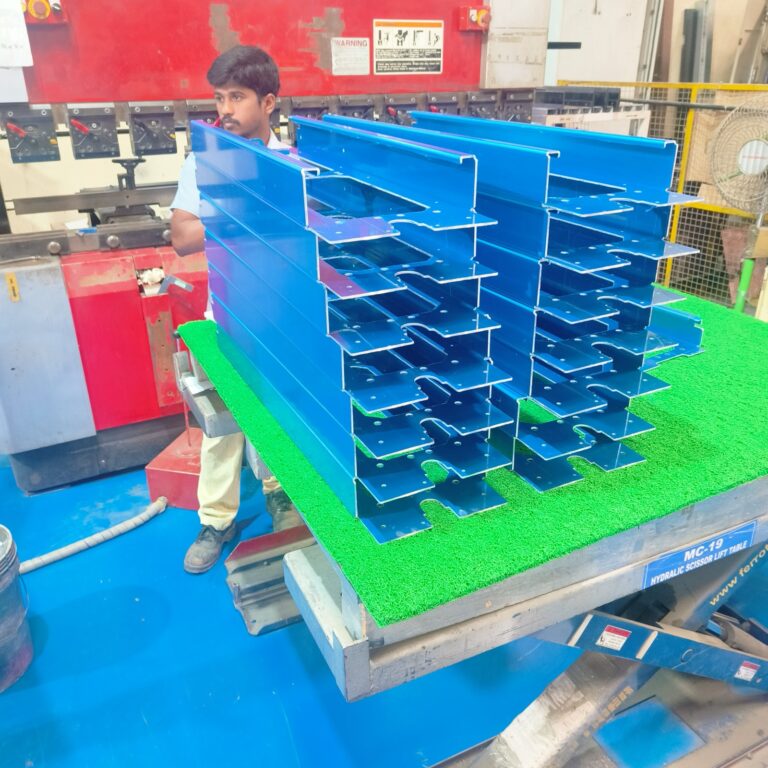
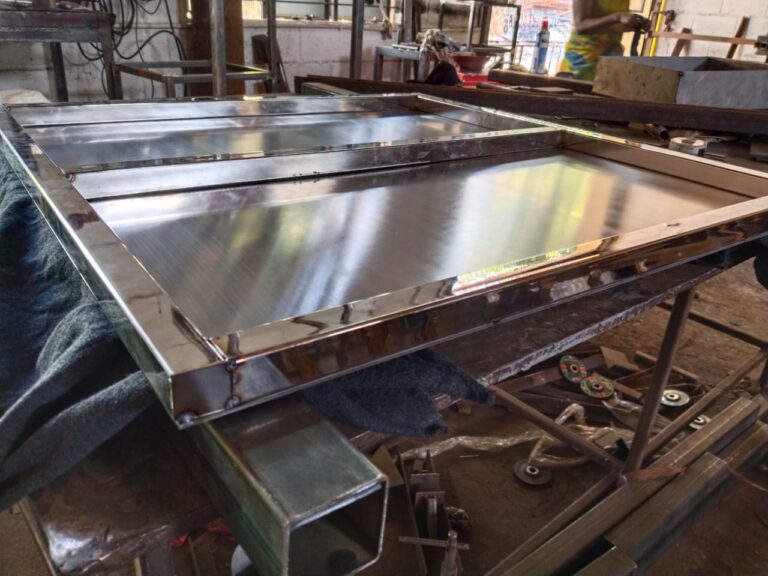
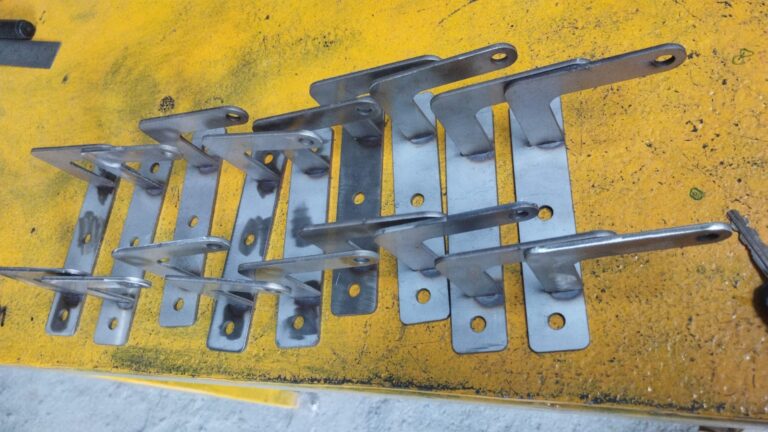
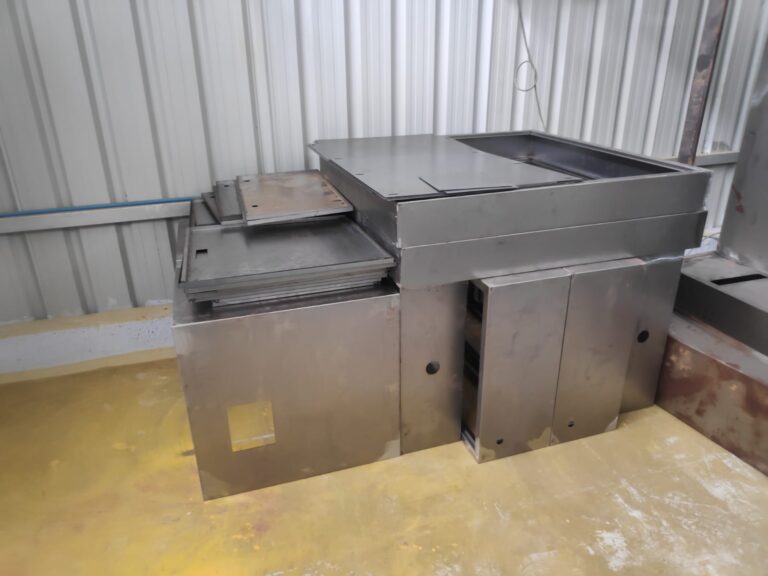
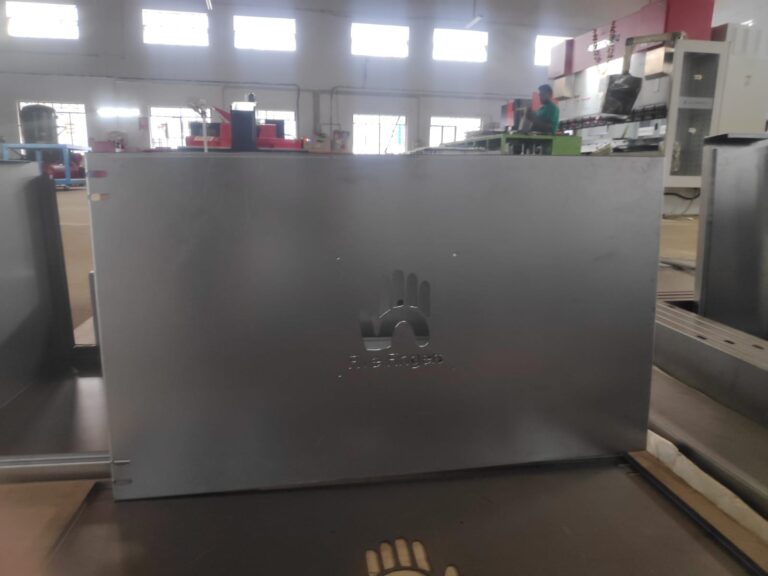
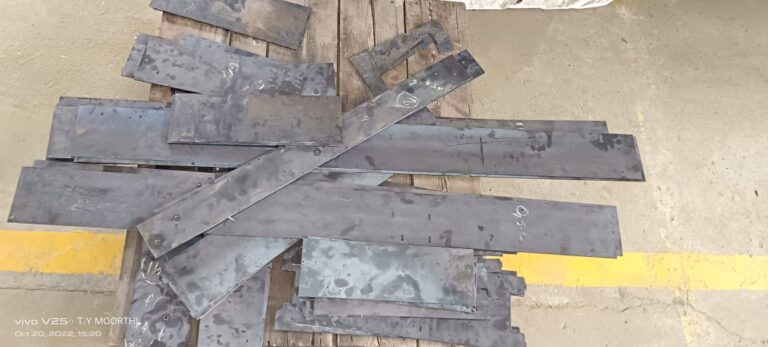
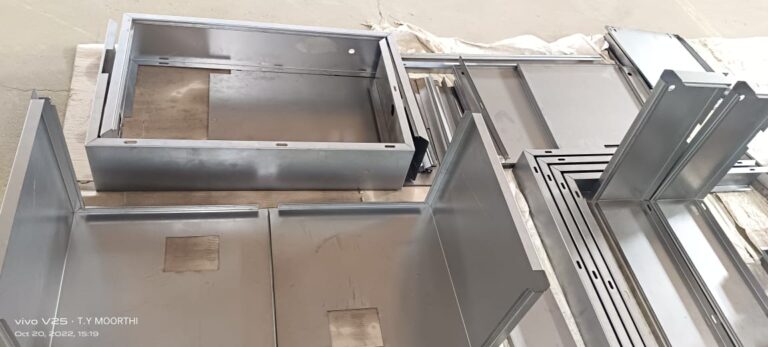
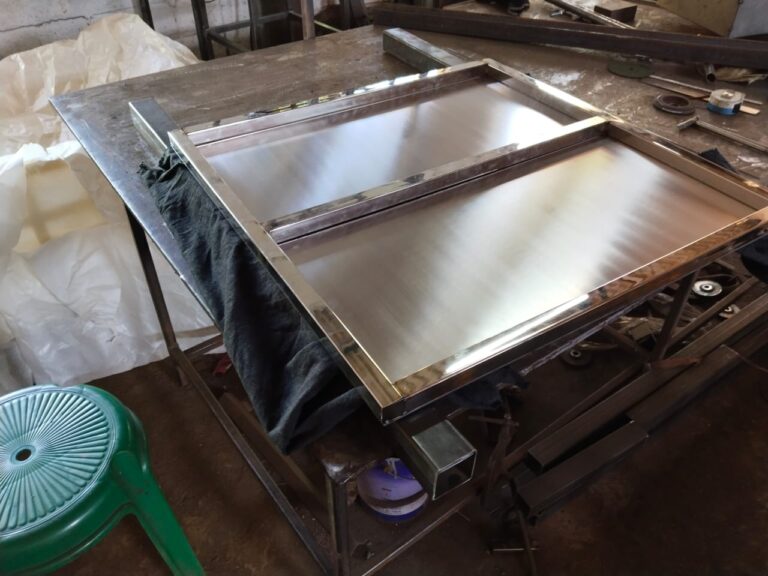
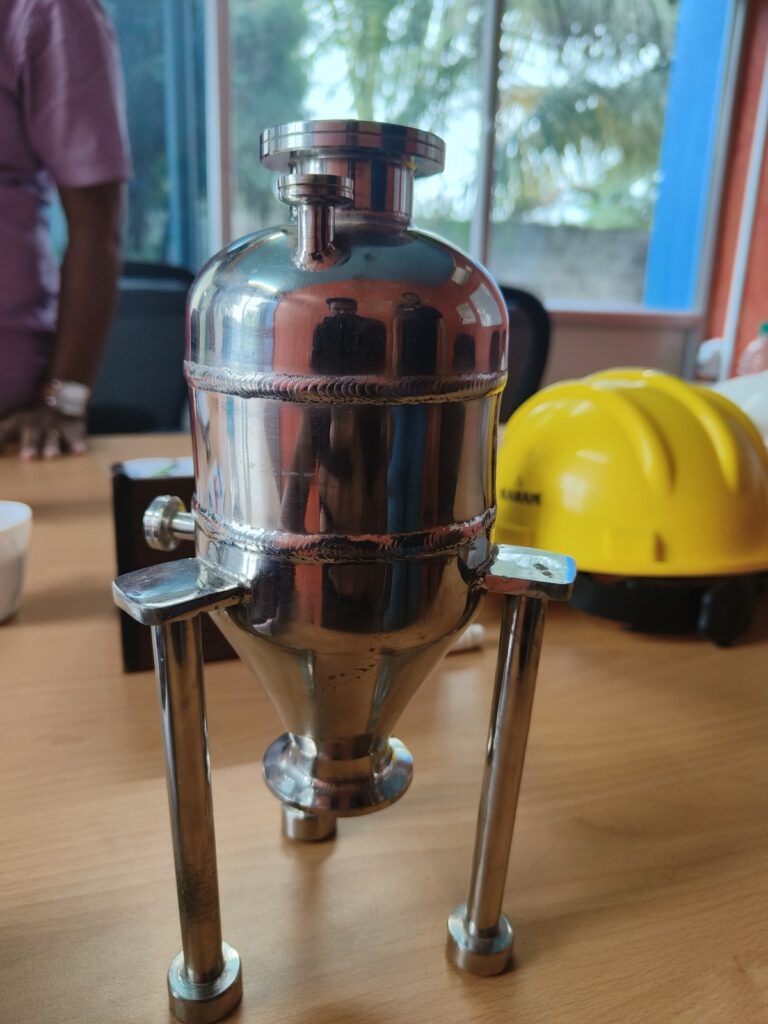
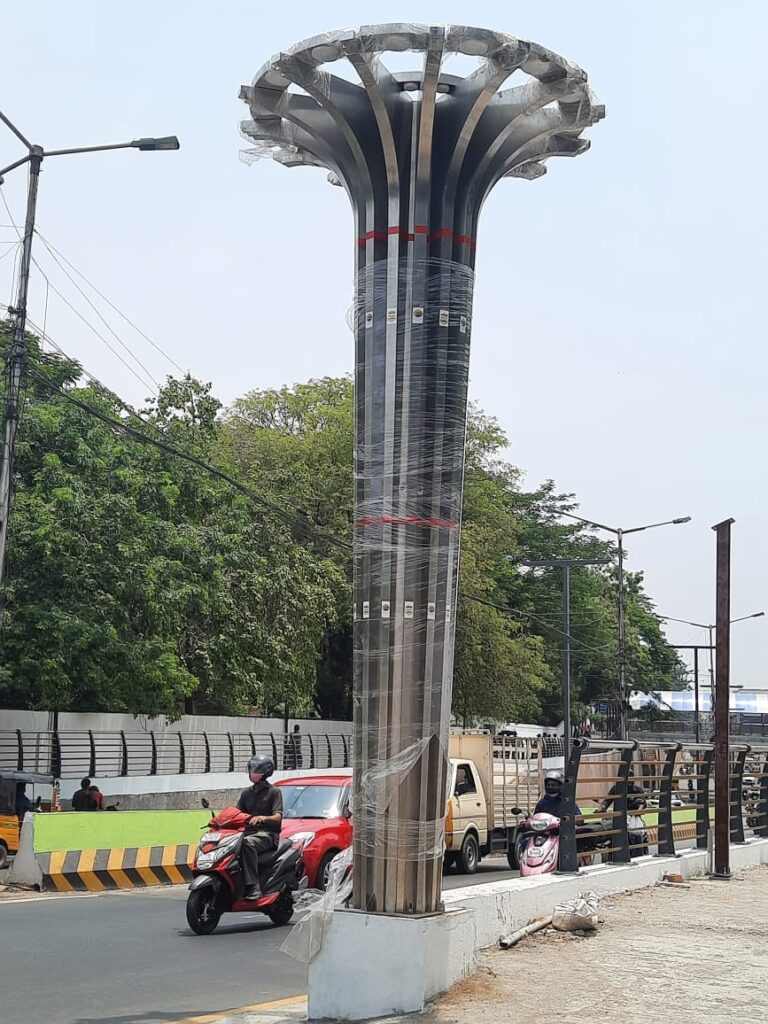
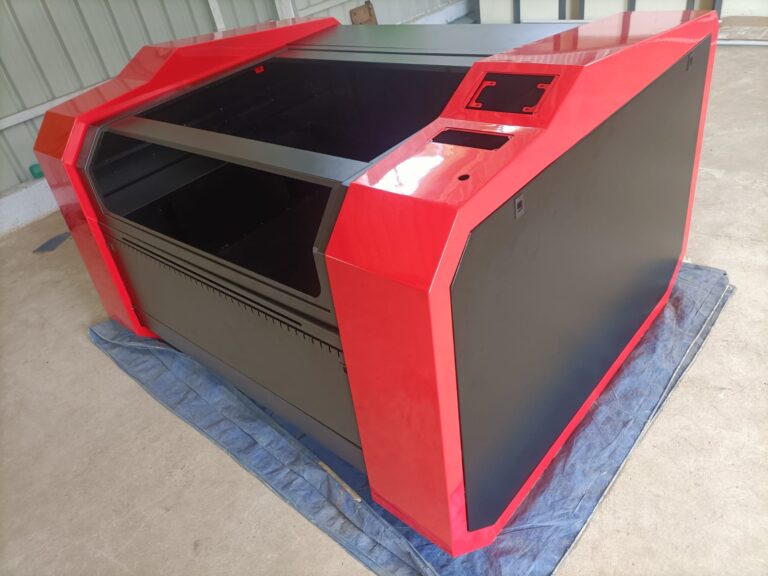
We'd love to Manufacture for you!
Submit the form below and our representative will be in touch shortly.
LOCATIONS
Registered Office
10-A, First Floor, V.V Complex, Prakash Nagar, Thiruverumbur, Trichy-620013, Tamil Nadu, India.
Operations Office
9/1, Poonthottam Nagar, Ramanandha Nagar, Saravanampatti, Coimbatore-641035, Tamil Nadu, India. ㅤ
Other Locations
- Bhilai
- Chennai
- USA
- Germany