- Leak Prevention
Valves
Frigate valves use advanced multi-layer seal technology to ensure near-zero leakage. Our proprietary materials and precise engineering maintain seal integrity under extreme pressure and temperature, protecting your systems from costly leaks and downtime.

- Modular Service Design
Modular design enables quick maintenance with easy access, reducing downtime and interruptions. Integrated diagnostics predict issues before failure.
- Standards Compliance Assured
Valves comply with API, ANSI, ISO, and ASME standards, ensuring full regulatory compliance and confidence during audits and inspections.
- Custom Engineering Solutions
Customizable valves with flexible materials and actuators tailored to specific needs, delivering superior integration and performance in complex systems.
Our Clients
Trusted by Engineers and Purchasing Leaders
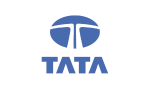
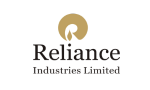


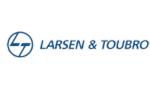
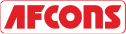


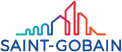

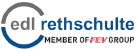

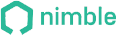
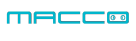









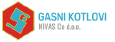
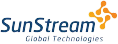

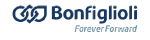


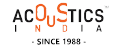
- Versatile Offerings
Our Valves Products
Explore our high-quality Valves solutions today



- Surge Protection
Reliable Protection Against Pressure Surges
Our valves are engineered to prevent damage caused by pressure surges and water hammers, ensuring system stability and longevity. With controlled closure speeds and robust materials, they withstand transient spikes exceeding 1500 psi.
- Valve actuators provide controlled closure times between 5 and 15 seconds to minimize sudden flow stoppage.
- Valve bodies and internals are constructed from ASTM A182 Grade F316 stainless steel or equivalent, ensuring tensile strength above 75 ksi for pressure surge resistance.
- Designed to withstand transient pressure spikes exceeding 1500 psi, safeguarding against mechanical fatigue and deformation.
- Incorporates integrated pressure relief ports or compatibility with external surge arrestors rated for pressures up to 2000 psi.
- Flow paths are engineered using Computational Fluid Dynamics (CFD) to optimize velocity profiles and reduce turbulent flow-induced shock.
- Sealing systems use resilient, high-temperature elastomers rated for up to 250°C to maintain integrity during rapid pressure changes.
- Real Impact
Words from Clients
See how global OEMs and sourcing heads describe their experience with our scalable execution.
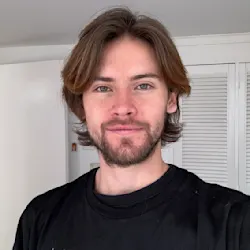
“Quick turnaround and solid quality.”
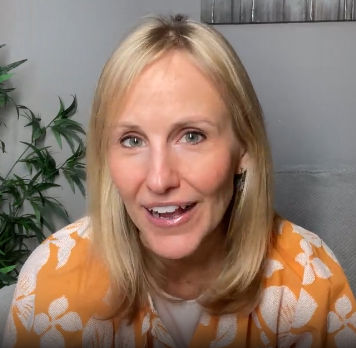
“The instant quote tool saved us time, and the parts were spot-on. Highly recommend Frigate!”
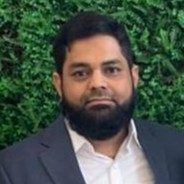
“I would strongly recommend Frigate to anyone who wants to do Rapid Prototyping, and take their ideas to manufacturing. One firm doing all kinds of Product Development!”
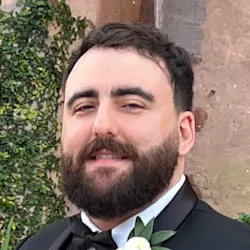
“Great service, fair price, and the parts worked perfectly in our assembly.”
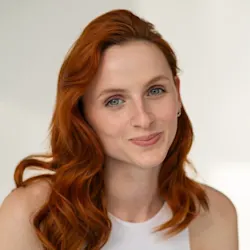
“Top-notch machining and fast shipping. Very satisfied with the results.”
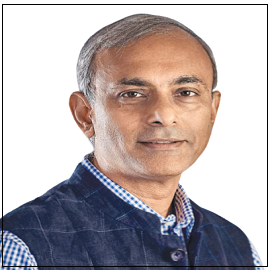
“The next disruption is happening in Prototyping & Manufacturing on-demand and Frigate is leading the way! I personally believe the Frigate's way of IIOT enabled cloud platform with Al.”
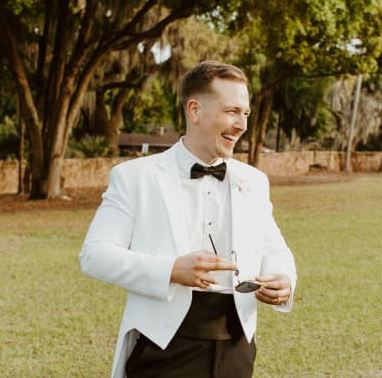
“Frigate delivered high-quality parts at a competitive price. The instant quote tool is a huge plus for us!”

“We appreciate the precision and quality of the machined components in the recent delivery—they meet our specifications perfectly and demonstrate Frigate’s capability for excellent workmanship.”
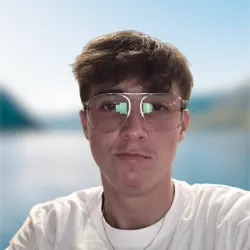
“Flawless execution from quote to delivery.”

“I am absolutely happy to work with supplier like Frigate who were quite proactive & result oriented . Frigate has high willingness team who has strong know how & their passion towards the products & process were absolutely thrilling.”
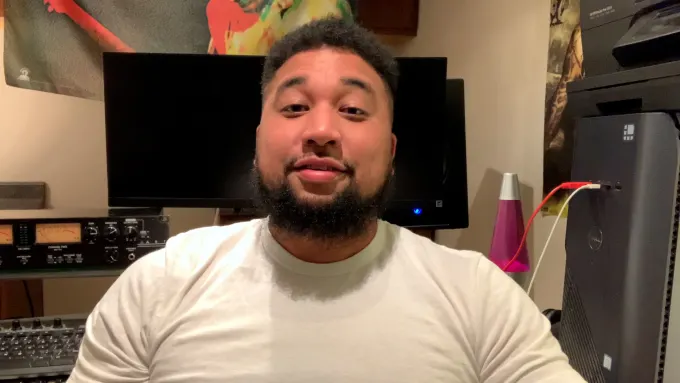
“The precision on these parts is impressive, and they arrived ahead of schedule. Frigate’s process really stands out!”
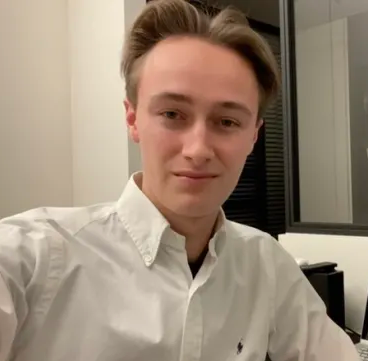
“Parts were exactly as spec’d, and the instant quote made budgeting a breeze.”
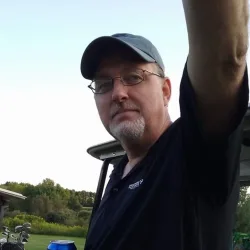
“Good value for the money.”
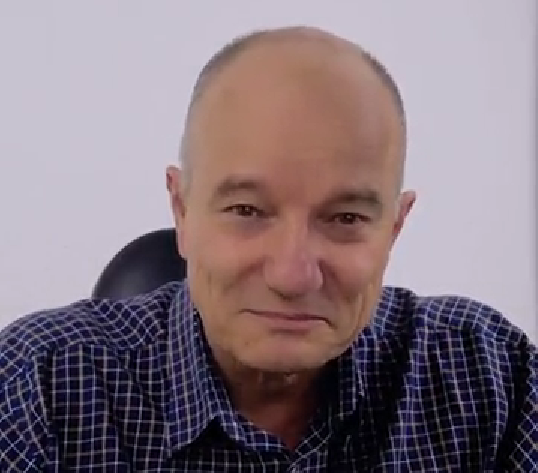
“The finish was perfect, and the team was easy to work with.”

“Working with Frigate has been great. Their proactive, results-driven approach and expertise shine through in every project. It's been a pleasure collaborating with them.”

"We are highly satisfied with the timely delivery and quality of the MIG Welding Cable from Frigate. Their attention to detail, secure packaging, and quick responsiveness stood out. We confidently recommend Frigate Engineering Services Pvt. Ltd. as a reliable manufacturing partner."
We export to 10+ countries
Frigate’s Global Presence
Frigate takes pride in facilitating “Make in India for the globe“. As our global network of Frigaters provides virtually limitless capacity, and through our IoT enabled platform your parts go directly into production. By digitally and technologically enabling “the silent pillars of the economy” MSME and SME manufacturing industries, we are able to tap the huge potential for manufacturing to bring the best results for our clients.

100,000+
Parts Manufactured
250+
Frigaters
2000+
Machines
450+
Materials
25+
Manufacturing Process
- Solid Progress
Our Manufacturing Metrics
Frigate brings stability, control, and predictable performance to your sourcing operations through a structured multi-vendor system.
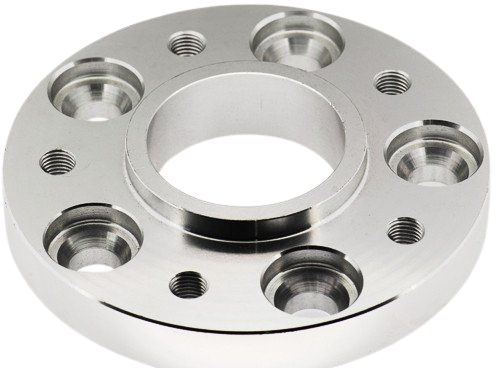
2.8X
Sourcing Cycle Speed
Frigate’s pre-qualified network shortens decision time between RFQ and PO placement.
94%
On-Time Delivery Rate
Structured planning windows and logistics-linked schedules improve project-level delivery reliability.
4X
Multi-Part Consolidation
We enable part family batching across suppliers to reduce fragmentation.
22%
Quality Rejection Rate
Multi-level quality checks and fixed inspection plans lower non-conformities.
30%
Procurement Costs
Optimized supplier negotiations and bulk order strategies reduce your overall sourcing expenses.
20%
Manual Processing Time
Automation of sourcing and supplier management significantly reduces time spent on manual tasks.
Valve trim geometry directly affects fluid velocity gradients and turbulence, primary noise sources. Complex multi-stage or cage-style trims reduce velocity step changes, limiting cavitation and pressure recovery noise. Computational Fluid Dynamics (CFD) simulations optimize these trims to achieve noise levels below 85 dB in industrial environments. Selecting the right trim can prevent damage and meet strict noise emission regulations.
Valves for supercritical fluids must handle highly variable densities and viscosities near the critical point, which causes fluctuating forces on valve internals. Materials must resist embrittlement and erosion due to rapid phase changes and possible corrosion from impurities. Tight sealing surfaces and robust actuators compensate for unpredictable pressure surges. Advanced finite element analysis (FEA) ensures structural integrity under these dynamic conditions.
Stem packing must accommodate thermal expansion and contraction without losing compressive force on the sealing elements. Using multi-component packing with graphite and PTFE layers offers flexibility and chemical resistance. This design maintains a consistent seal despite temperatures between -40°C and 300°C. Proper gland follower adjustments help prevent leakage without increasing friction or wear.
Thicker valve walls increase resistance to stress concentration caused by internal pressure cycles, improving fatigue life exponentially. Reinforcements at nozzle connections and high-stress zones reduce crack initiation points. Material selection with high fatigue strength and toughness and stress-relief heat treatments further extend service life. Fatigue testing per ASTM E466 validates the valve’s endurance for over 10 million cycles.
Dynamic seals incorporate elastomers with high Shore hardness and metal backup rings to maintain shape under pressure pulses. Seal profiles are engineered to flex without permanent deformation during rapid transient events. Finite Element Analysis models stress distribution across the seal during spikes up to 2000 psi. This approach ensures long-lasting leak-tight performance even under harsh cycling conditions.
We'd love to Manufacture for you!
Submit the form below and our representative will be in touch shortly.
LOCATIONS
Registered Office
10-A, First Floor, V.V Complex, Prakash Nagar, Thiruverumbur, Trichy-620013, Tamil Nadu, India.
Operations Office
9/1, Poonthottam Nagar, Ramanandha Nagar, Saravanampatti, Coimbatore-641035, Tamil Nadu, India. ㅤ
Other Locations
- Bhilai
- Chennai
- USA
- Germany