- Fluid Management
Safety & Relief Valves
Frigate’s optimized valve designs feature balanced blowdown and tight seating to minimize fluid venting during pressure relief. This reduces waste, lowers emissions, and helps maintain compliance with environmental standards.

Our Clients
Trusted by Engineers and Purchasing Leaders
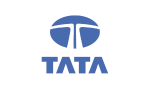
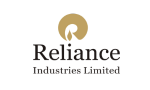


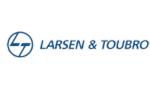
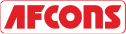


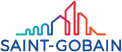

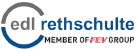

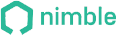
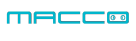









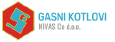
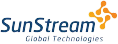

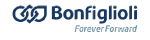


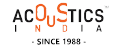
- Versatile Offerings
Our Safety & Relief Valves Products
Explore our range of high-quality Safety & Relief Valves today.
- Real Impact
Words from Clients
See how global OEMs and sourcing heads describe their experience with our scalable execution.
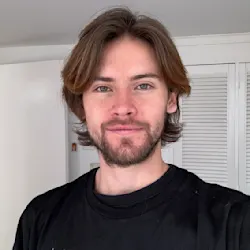
“Quick turnaround and solid quality.”
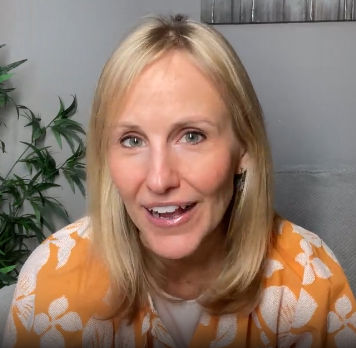
“The instant quote tool saved us time, and the parts were spot-on. Highly recommend Frigate!”
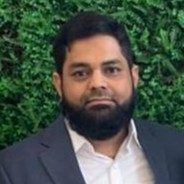
“I would strongly recommend Frigate to anyone who wants to do Rapid Prototyping, and take their ideas to manufacturing. One firm doing all kinds of Product Development!”
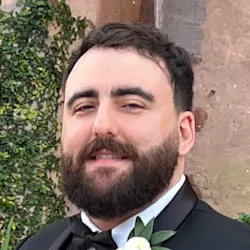
“Great service, fair price, and the parts worked perfectly in our assembly.”
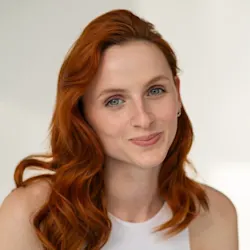
“Top-notch machining and fast shipping. Very satisfied with the results.”
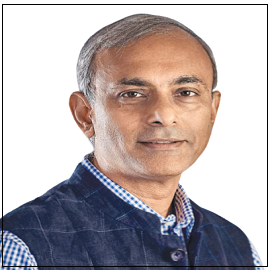
“The next disruption is happening in Prototyping & Manufacturing on-demand and Frigate is leading the way! I personally believe the Frigate's way of IIOT enabled cloud platform with Al.”
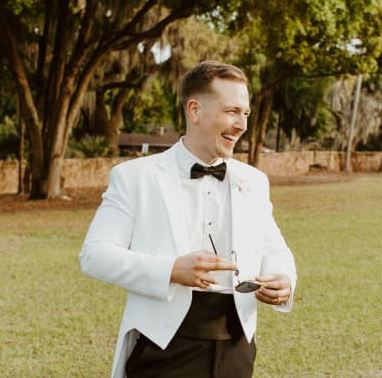
“Frigate delivered high-quality parts at a competitive price. The instant quote tool is a huge plus for us!”

“We appreciate the precision and quality of the machined components in the recent delivery—they meet our specifications perfectly and demonstrate Frigate’s capability for excellent workmanship.”
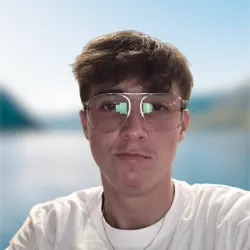
“Flawless execution from quote to delivery.”

“I am absolutely happy to work with supplier like Frigate who were quite proactive & result oriented . Frigate has high willingness team who has strong know how & their passion towards the products & process were absolutely thrilling.”
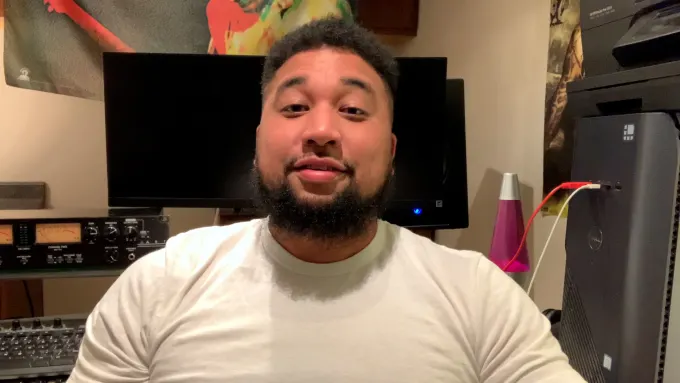
“The precision on these parts is impressive, and they arrived ahead of schedule. Frigate’s process really stands out!”
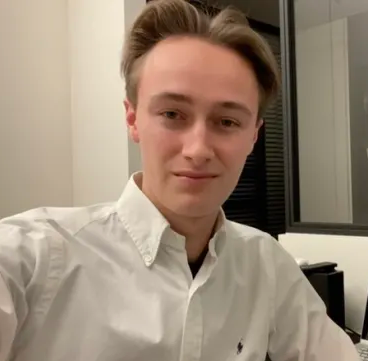
“Parts were exactly as spec’d, and the instant quote made budgeting a breeze.”
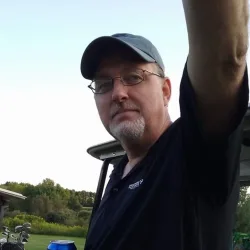
“Good value for the money.”
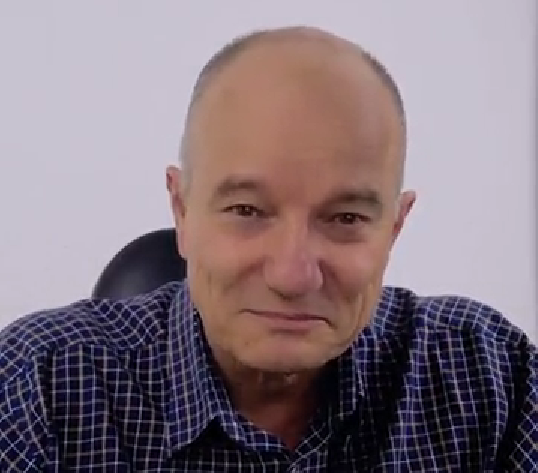
“The finish was perfect, and the team was easy to work with.”

“Working with Frigate has been great. Their proactive, results-driven approach and expertise shine through in every project. It's been a pleasure collaborating with them.”

"We are highly satisfied with the timely delivery and quality of the MIG Welding Cable from Frigate. Their attention to detail, secure packaging, and quick responsiveness stood out. We confidently recommend Frigate Engineering Services Pvt. Ltd. as a reliable manufacturing partner."
We export to 10+ countries
Frigate’s Global Presence
Frigate takes pride in facilitating “Make in India for the globe“. As our global network of Frigaters provides virtually limitless capacity, and through our IoT enabled platform your parts go directly into production. By digitally and technologically enabling “the silent pillars of the economy” MSME and SME manufacturing industries, we are able to tap the huge potential for manufacturing to bring the best results for our clients.

100,000+
Parts Manufactured
250+
Frigaters
2000+
Machines
450+
Materials
25+
Manufacturing Process
Industry Applications
Prevent catastrophic failures by controlling pressure in fractionation columns, storage tanks, and heat exchangers under variable operating conditions.
Protect compressors and piping networks by venting excess pressure during sudden load changes or system malfunctions.
Maintain safe pressure levels in liquefied gas tanks, preventing overpressure from thermal expansion or system faults.
Regulate pressure in fuel, hydraulic, and pneumatic systems to ensure operational safety during flight conditions.
Control pressure in gas cylinders and pipelines, ensuring containment integrity and safe handling of high-pressure gases.
Protect slurry pumps and pressurized vessels from pressure spikes caused by process variations and equipment cycles.




- Proactive Upkeep
Easy Maintenance for Maximum Uptime
Our valves are designed to reduce maintenance time and effort, even in tight or hard-to-reach spaces. Modular components and tool-less servicing simplify repairs and adjustments, minimizing downtime.
- Cartridge-style assembly allows spring and seat replacement without full valve removal, reducing downtime by 60%.
- Precision-machined components enable repeatable calibration adjustments with ±1% set pressure accuracy.
- Tool-less bonnet design uses quick-release clamps for fast access in confined installations.
- Corrosion-resistant stainless steel (316L) and hardened seats extend valve life in aggressive environments by 40%.
- Integrated position indicators with magnetic sensors provide real-time valve status for predictive maintenance.
The spring material must have excellent fatigue resistance to maintain consistent force after thousands of pressure cycles. Materials like Inconel X750 are commonly used because they resist relaxation and corrosion, preserving set pressure accuracy. Poor material choice leads to spring creep, causing set pressure drift and premature valve failure. Selecting the right spring alloy ensures the valve reliably opens at the designated pressure throughout its service life.
To prevent structural failure, FEA helps engineers assess mechanical stresses on valve components under extreme pressure and temperature conditions. CFD simulations analyze fluid flow patterns inside the valve to minimize turbulence, pressure drops, and noise during operation. Combining these tools optimizes material use and ensures reliable performance under varying process conditions. This approach reduces the need for physical prototyping and accelerates product development.
Valve trims made from hardened alloys or coated with tungsten carbide reduce surface wear caused by abrasive particles in the flow stream. The trim geometry is designed to reduce velocity hotspots and direct flow paths to minimize erosion. These design choices prevent premature thinning of critical parts, extending valve lifespan significantly. Proper trim design is essential for maintaining valve integrity in harsh industrial environments.
Hysteresis—the difference between opening and closing pressures—must be minimized to ensure precise pressure control. It is controlled by using high-quality, low-friction materials for seals and poppet guides and optimized spring preload settings. Minimizing hysteresis prevents pressure fluctuations and reduces wear on valve components. This ensures stable and repeatable valve operation over millions of cycles.
Dynamic pressure changes and flow-induced vibrations can cause valve seats to deform or loosen, leading to leaks. To counter this, engineers use highly resilient flexible seat materials and apply precision machining to ensure tight tolerances. Additionally, valve bodies may incorporate damping features to absorb vibrations and maintain seal integrity. These engineering solutions help maintain leak-tight performance even under rapidly changing pressures.
We'd love to Manufacture for you!
Submit the form below and our representative will be in touch shortly.
LOCATIONS
Registered Office
10-A, First Floor, V.V Complex, Prakash Nagar, Thiruverumbur, Trichy-620013, Tamil Nadu, India.
Operations Office
9/1, Poonthottam Nagar, Ramanandha Nagar, Saravanampatti, Coimbatore-641035, Tamil Nadu, India. ㅤ
Other Locations
- Bhilai
- Chennai
- USA
- Germany