Gas-Assisted Injection Molding Services
Frigate’s Gas-Assisted Injection Molding reduces material use and enhances part strength. We offer precise control over wall thickness and internal cavity formation.
Our Clients





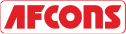

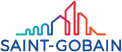


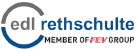

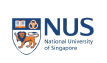
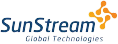

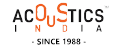




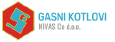
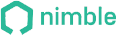
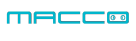












Advantages of Gas-Assisted Injection Molding Services
Reduced Warping and Shrinkage
Gas-assisted injection molding minimizes internal stresses, preventing part warping and shrinkage during cooling.
Enhanced Surface Quality
The controlled gas injection improves the surface finish of parts, reducing defects like sink marks and voids.
Lower Injection Pressure
This method reduces injection pressure, decreasing wear on molds and machinery, thus improving equipment lifespan.
Energy Efficiency
The process requires less energy than traditional injection molding because it reduces material usage and optimizes cycle times.
Precision with Custom Gas-Assisted Injection Molding Services
High material costs and long cycle times are common manufacturing challenges. Gas-Assisted Injection Molding reduces material use and improves efficiency. The process uses controlled gas injection to create hollow sections, reducing weight while maintaining strength. It allows precise control over wall thickness and cavity design, enabling complex geometries. This method also reduces warping and shrinkage and improves surface finish, ensuring consistent results in high-volume production.

Get Your Quote Now
- Instant Quotation
- On-Time Delivery
- Affordable Cost
Our Gas-Assisted Injection Molding Process






The process begins with the injection of molten plastic under high pressure into the mold cavity.
After the material fills the cavity, a controlled gas (usually nitrogen) is injected into the molten plastic, creating hollow sections within the part.
The gas expands, pushing the plastic against the mold walls, helping to form the part's outer shape while reducing material use.
The plastic begins to cool and solidify, with the gas helping to control the cooling rate and reduce internal stresses.
Any excess gas is vented out of the mold cavity to prevent pressure buildup and ensure the part’s integrity.
Once the part has cooled and solidified, it is ejected from the mold ready for further processing or finishing.
Gas-Assisted Injection Molding Materials
Gas-Assisted Injection Molding optimizes part design by reducing material use and weight. This process enhances efficiency, precision, and surface quality while maintaining structural integrity.
PP is lightweight, chemically resistant, and offers high fatigue resistance. Gas-assisted molding ensures uniform wall thickness and reduced cycle times, ideal for automotive and consumer products.
ABS offers high impact resistance and dimensional stability. Gas-assisted molding optimizes flow and reduces defects like sink marks, making it suitable for electronics, automotive, and appliances.
Known for high impact resistance and transparency, PC benefits from gas-assisted molding to maintain consistent wall thickness and improve mechanical properties for applications like safety components and lighting covers.
Nylon provides high tensile strength and wear resistance. Gas-assisted molding enhances strength and surface finish and reduces warpage, making it ideal for automotive and industrial parts.
PLA is biodegradable and has good tensile strength and impact resistance. Gas-assisted molding reduces material use and ensures uniform thickness, making it suitable for eco-friendly products and packaging.
LDPE and HDPE offer excellent chemical resistance and flexibility. Gas-assisted molding optimizes part geometry and reduces warping, ideal for medical devices, packaging, and fluid systems.
High-performance plastics like PEEK and PPS offer superior strength, thermal stability, and chemical resistance. Gas-assisted molding improves part density and surface finish, making them ideal for aerospace and industrial applications.
TPE combines rubber flexibility with plastic processing ease. Gas-assisted molding ensures precise part geometry and soft-touch surfaces, and it is used in seals, gaskets, and flexible consumer products.
Ensure Even Wall Thickness for Complex Part Designs
Gas-assisted injection molding ensures even material distribution by injecting gas into the mold cavity during injection. This gas forms a hollow core, which reduces the material volume and allows for more consistent flow. The technique helps prevent common defects such as sink marks or warping by maintaining uniform thickness across complex geometries or varying wall sections. By reducing internal stresses and promoting material uniformity, Frigate’s expertise improves the overall structural integrity of the part.

Compliance for Gas-Assisted Injection Molding Services
Gas-assisted injection Molding (GAIM) at a Frigate uses nitrogen or other gases to create hollow sections in injection-molded parts. The process reduces material usage, weight, and cycle times while maintaining part strength. Gases are injected into the molten plastic before it fills the mold, creating internal cavities without compromising the exterior surface. This technology is ideal for parts with complex geometries and thinner walls.
Ensures effective quality management and consistency across all stages of the GAIM process.
Governs medical device production, ensuring products meet stringent safety and quality controls.
Sets standards for gas-assisted injection molding materials, ensuring correct mechanical properties and performance.
Restricts the use of hazardous substances in electronics, ensuring safety and compliance with global regulations.
Standard for flammability of plastic materials, crucial for parts requiring fire resistance and electrical safety.
Focuses on environmental management, ensuring sustainable practices and reducing environmental impact in GAIM processes.

Tolerance for Gas-Assisted Injection Molding Services
Tolerance for precise control of gate seal to prevent gas leakage during injection.
Variance in pressure distribution within the mold cavity, impacting part uniformity.
Control of gas penetration depth into the molten plastic to avoid premature solidification.
Tolerance on the speed of the advancing melt front during injection, affecting cavity fill.
Variation in injection speed, which can influence the flow rate of molten plastic and gas mix.
Temperature variation of the flow front as the plastic enters the mold cavity, ensuring optimal filling.
Control of pressure within the hollow core to manage the formation of internal cavities.
Precision in the time taken to fill the mold, affecting part consistency and gas expansion.
Tolerance on the effectiveness of venting systems to ensure proper gas release and prevent defects.
Tolerance on the rate of shear experienced by the material as it moves through the mold cavity.
Precision in cooling rates after injection to minimize thermal gradients and warping.
Tolerance in compression of the molten plastic due to gas injection, influencing cavity formation.
Variance in the pressure applied during the injection process, affecting part density and surface finish.
Control of the force used to eject the molded part, ensuring no deformation or part damage.

Quality Testing Standards for Gas-Assisted Injection Molding Services
Measures the rate of gas injected into the cavity, ensuring proper cavity expansion.
Assesses the shrinkage of the part as it cools, ensuring dimensional stability and accuracy.
Monitors and verifies the uniformity of gas pressure throughout the mold cavity during the injection phase.
Measures the viscosity of the molten plastic to ensure consistent flow and proper gas injection.
Simulates and analyzes the flow of material and gas to identify any issues with cavity filling or void formation.
Measures the mechanical stiffness of the molded part to confirm it meets structural requirements.
Monitors the time taken for each cycle, ensuring consistent, repeatable production cycles.
Measures the precise timing of gas injection relative to plastic injection to optimize part quality.
Analyzes residual gas left inside the part after injection, ensuring no excess gas is trapped.
Detects distortion or warping of the part after cooling, verifying that the part maintains its shape.
Assesses the temperature distribution within the mold and part, ensuring uniform cooling to avoid thermal distortion.
Records the pressure change over time within the cavity to verify that gas pressure is maintained for optimal part formation.
Measures the time taken for the gate to freeze, preventing flash or overfill in the mold.
Assesses the efficiency of the cooling system to ensure uniform part cooling and prevent defects.
Measures the tensile strength of the molded part to ensure it meets the required material properties.
Drive Precision and Efficiency in Automotive Component Molding
Achieving precision and efficiency in automotive component manufacturing is challenging, especially with complex geometries and tight tolerances. Gas-assisted injection molding addresses these issues by introducing gas into the mold cavity to form a hollow core. This ensures uniform wall thickness, improves material distribution, and reduces defects like sink marks and warping. The process also speeds up cooling, reducing cycle times and enhancing production efficiency. Gas-assisted molding optimizes automotive component manufacturing with high precision by improving part quality and accelerating production.







Industries We Serve
- Solid Progress
Our Manufacturing Metrics
Frigate brings stability, control, and predictable performance to your sourcing operations through a structured multi-vendor system.
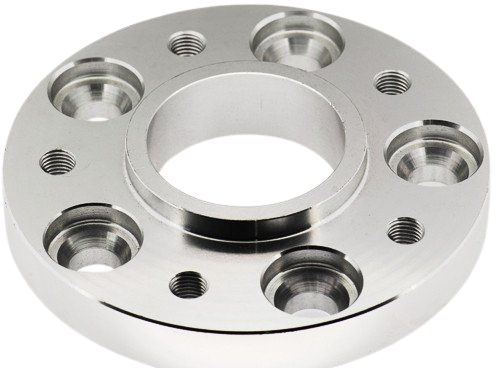
2.8X
Sourcing Cycle Speed
Frigate’s pre-qualified network shortens decision time between RFQ and PO placement.
94%
On-Time Delivery Rate
Structured planning windows and logistics-linked schedules improve project-level delivery reliability.
4X
Multi-Part Consolidation
We enable part family batching across suppliers to reduce fragmentation.
22%
Quality Rejection Rate
Multi-level quality checks and fixed inspection plans lower non-conformities.
30%
Procurement Costs
Optimized supplier negotiations and bulk order strategies reduce your overall sourcing expenses.
20%
Manual Processing Time
Automation of sourcing and supplier management significantly reduces time spent on manual tasks.
Streamline High-Volume Manufacturing with Reduced Cycle Times
Gas-assisted molding reduces cooling time by introducing gas into the mold cavity, creating voids that decrease the material that needs to cool. This results in faster cooling rates and reduced cycle times. The process allows for faster solidification of parts, leading to higher throughput in high-volume production. Additionally, optimizing the gas injection and cooling rate minimizes cycle times without compromising part quality, making this method ideal for efficient, large-scale manufacturing.

Get Clarity with Our Manufacturing Insights
- Real Impact
Words from Clients
See how global OEMs and sourcing heads describe their experience with our scalable execution.
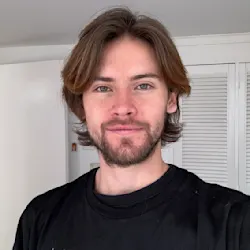
“Quick turnaround and solid quality.”
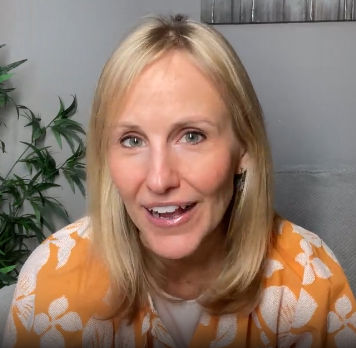
“The instant quote tool saved us time, and the parts were spot-on. Highly recommend Frigate!”
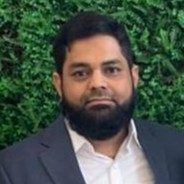
“I would strongly recommend Frigate to anyone who wants to do Rapid Prototyping, and take their ideas to manufacturing. One firm doing all kinds of Product Development!”
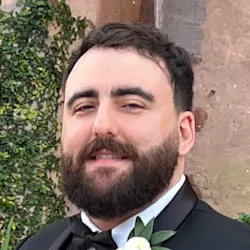
“Great service, fair price, and the parts worked perfectly in our assembly.”
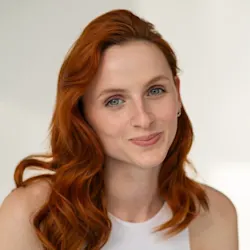
“Top-notch machining and fast shipping. Very satisfied with the results.”
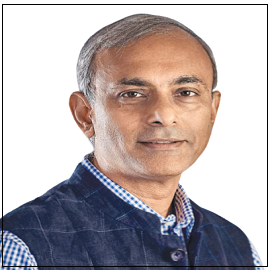
“The next disruption is happening in Prototyping & Manufacturing on-demand and Frigate is leading the way! I personally believe the Frigate's way of IIOT enabled cloud platform with Al.”
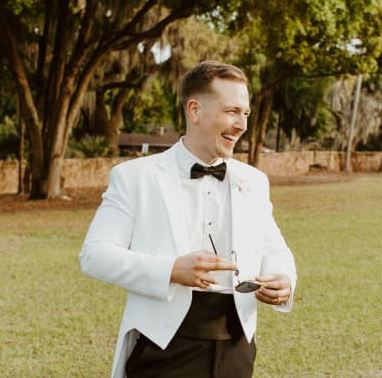
“Frigate delivered high-quality parts at a competitive price. The instant quote tool is a huge plus for us!”

“We appreciate the precision and quality of the machined components in the recent delivery—they meet our specifications perfectly and demonstrate Frigate’s capability for excellent workmanship.”
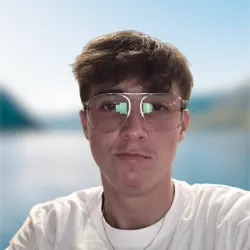
“Flawless execution from quote to delivery.”

“I am absolutely happy to work with supplier like Frigate who were quite proactive & result oriented . Frigate has high willingness team who has strong know how & their passion towards the products & process were absolutely thrilling.”
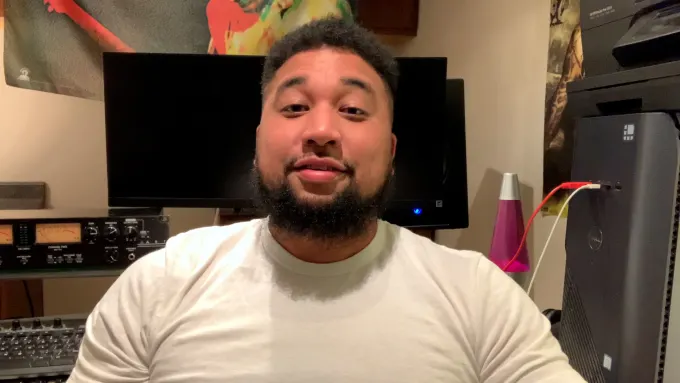
“The precision on these parts is impressive, and they arrived ahead of schedule. Frigate’s process really stands out!”
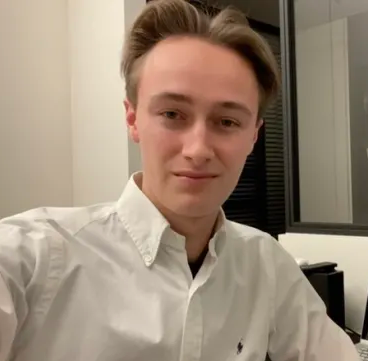
“Parts were exactly as spec’d, and the instant quote made budgeting a breeze.”
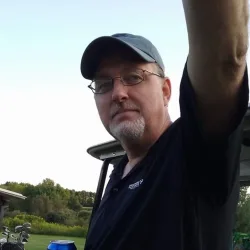
“Good value for the money.”
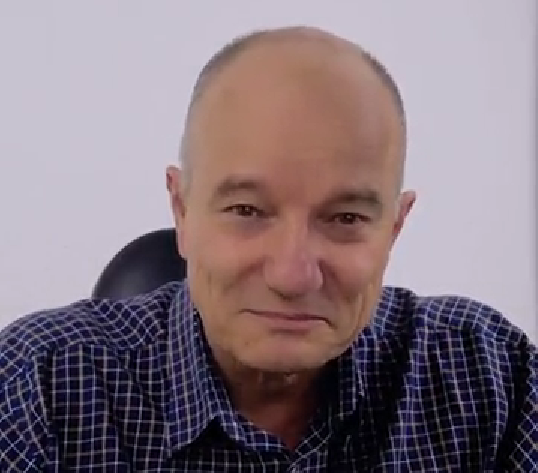
“The finish was perfect, and the team was easy to work with.”

“Working with Frigate has been great. Their proactive, results-driven approach and expertise shine through in every project. It's been a pleasure collaborating with them.”

"We are highly satisfied with the timely delivery and quality of the MIG Welding Cable from Frigate. Their attention to detail, secure packaging, and quick responsiveness stood out. We confidently recommend Frigate Engineering Services Pvt. Ltd. as a reliable manufacturing partner."
Having Doubts? Our FAQ
Check all our Frequently Asked Question
The controlled gas injection helps reduce the viscosity of high-melt polymers by creating a gas core, allowing for better flow and uniform filling of complex geometries.
Gas-assisted molding can help control the cooling rate, reducing internal stress and promoting uniform crystallization. This leads to improved mechanical properties and dimensional stability in semi-crystalline polymers.
Creating a uniform internal gas cavity mitigates uneven cooling, reduces residual stresses, and significantly lowers the risk of warpage in parts with complex geometries.
Yes, the gas pressure assists in maintaining uniform wall thickness and minimizing material shrinkage, allowing for the production of parts with tight tolerances even in regions with varying wall thickness.
The balance between injection and gas pressure is critical to achieving optimal fill, uniform wall thickness, and proper cavity formation. Improper pressure ratios can lead to defects such as voids, inconsistent surface finish, or incomplete part fill.
We'd love to Manufacture for you!
Submit the form below and our representative will be in touch shortly.
LOCATIONS
Registered Office
10-A, First Floor, V.V Complex, Prakash Nagar, Thiruverumbur, Trichy-620013, Tamil Nadu, India.
Operations Office
9/1, Poonthottam Nagar, Ramanandha Nagar, Saravanampatti, Coimbatore-641035, Tamil Nadu, India. ㅤ
Other Locations
- Bhilai
- Chennai
- USA
- Germany