Electronic Manufacturing Services
Frigate offers precision Electronic Manufacturing Services for complex electronic systems. We ensure robust PCB assembly, component sourcing, and thorough testing for high reliability.
Our Clients





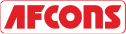

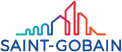


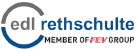

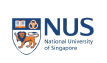
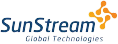

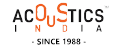




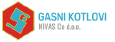
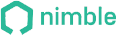
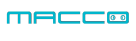












Advantages of Electronic Manufacturing Services
High-Precision PCB Assembly
We provide accurate PCB assembly with tight tolerances, ensuring reliable performance and minimizing defects in complex electronic circuits.
Component Sourcing Efficiency
Our expertise in component sourcing allows for cost-effective procurement of high-quality parts, ensuring product reliability and supply chain efficiency.
Thorough Testing and Quality Control
We perform rigorous testing and quality control, identifying issues early to ensure consistent performance and durability of finished products.
Scalable Production Capabilities
We offer flexible production volumes, allowing for efficient scaling from prototype to high-volume manufacturing while maintaining strict quality standards.
Custom Electronic Manufacturing Services for Precision and Reliability
Custom electronic manufacturing ensures precise, high-quality results tailored to specific project requirements. With PCB assembly, component sourcing, and testing expertise, every production stage is optimized for performance. Scalable production capabilities allow flexibility, supporting low-volume prototypes and high-volume manufacturing. Rigorous quality control procedures ensure reliability, consistency, and adherence to industry standards. This approach guarantees that each electronic system meets exact specifications and delivers optimal functionality across diverse applications.

Get Your Quote Now
- Instant Quotation
- On-Time Delivery
- Affordable Cost
Our Electronic Manufacturing Process






The process begins with a thorough design review to assess functionality, followed by prototype development to validate the design and identify potential issues early.
Critical components are sourced from reliable suppliers based on project specifications, ensuring high quality, compatibility, and cost efficiency.
The printed circuit boards (PCBs) are assembled using advanced techniques, including component placement, soldering, and surface-mount technology (SMT) for optimal performance.
Rigorous testing, including electrical, thermal, and stress tests, is performed to ensure each assembly meets functionality, safety, and compliance standards.
Comprehensive inspection and quality control checks are conducted at every stage to prevent defects and ensure the highest standards of performance and reliability.
After all components are integrated and tested, the final product is assembled, packaged, and prepared for shipping, meeting all client specifications and industry requirements.
Industries We Serve

The process begins with a thorough design review to assess functionality, followed by prototype development to validate the design and identify potential issues early.
Critical components are sourced from reliable suppliers based on project specifications, ensuring high quality, compatibility, and cost efficiency.
The printed circuit boards (PCBs) are assembled using advanced techniques, including component placement, soldering, and surface-mount technology (SMT) for optimal performance.
Rigorous testing, including electrical, thermal, and stress tests, is performed to ensure each assembly meets functionality, safety, and compliance standards.
Comprehensive inspection and quality control checks are conducted at every stage to prevent defects and ensure the highest standards of performance and reliability.
After all components are integrated and tested, the final product is assembled, packaged, and prepared for shipping, meeting all client specifications and industry requirements.
Our Electronic Manufacturing Process
Ensuring Reliable Component Sourcing and Availability
Managing component sourcing involves strategic partnerships with a network of reliable suppliers. Frigate ensures access to various components through advanced supply chain management. Proactive forecasting and constant monitoring of market trends allow for early identification of potential supply disruptions. In cases of component obsolescence, alternative components with equivalent performance are sourced, ensuring production continuity. This approach reduces the risk of delays and ensures that the manufacturing process remains on schedule without compromising quality.

Electronic Manufacturing Materials
The success of electronic manufacturing relies on precise design and accurate assembly. Every step, from initial prototyping to final testing, ensures the highest quality standards.
Copper is used in PCB fabrication for its high electrical conductivity, which is essential for reducing signal loss and power dissipation in high-frequency circuits and high-speed data transmission.
In heat sinks and housings, aluminum's low thermal resistance and light weight are ideal for efficiently managing heat in power electronics, preventing thermal damage to sensitive components.
Gold is used in connectors and contacts because of its low contact resistance and excellent corrosion resistance. This ensures long-term reliability in critical connections in high-reliability applications like aerospace and telecommunications.
Silicon is the base material for semiconductors. It is used in integrated circuits (ICs), transistors, and diodes, offering optimized performance for signal processing, switching, and power regulation in digital and analog devices.
FR4 is the standard laminate material for PCBs. It combines high mechanical strength with electrical insulation properties, providing stable performance in diverse environments and at high frequencies.
Tantalum capacitors are used in circuits requiring high capacitance and stable performance over a wide temperature range. They are often found in space, military, and medical devices where reliability is critical.
Nickel plating is utilized for its excellent hardness, corrosion resistance, and solderability. It is ideal for protecting connectors and terminals in industrial, automotive, and consumer electronics exposed to environmental stressors.
Precision Engineering for Aerospace & Defense through Electronic Manufacturing
Frigate’s Electronic Manufacturing Services (EMS) delivers robust solutions leveraging advanced PCB design, high-precision assembly processes, and rigorous testing. Automated assembly systems, real-time quality control, and statistical process monitoring ensure consistency across every unit produced. Using cutting-edge materials and manufacturing techniques, EMS minimizes component failure, reduces lead times, and ensures critical systems operate reliably in demanding environments.
- Solid Progress
Our Manufacturing Metrics
Frigate brings stability, control, and predictable performance to your sourcing operations through a structured multi-vendor system.
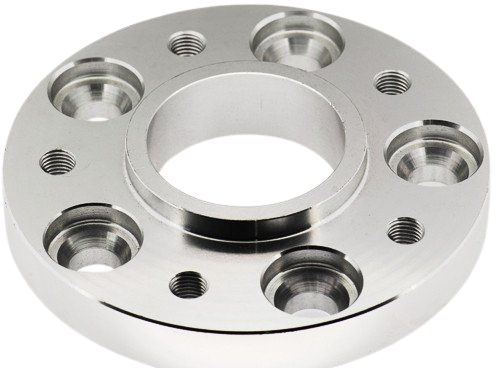
2.8X
Sourcing Cycle Speed
Frigate’s pre-qualified network shortens decision time between RFQ and PO placement.
94%
On-Time Delivery Rate
Structured planning windows and logistics-linked schedules improve project-level delivery reliability.
4X
Multi-Part Consolidation
We enable part family batching across suppliers to reduce fragmentation.
22%
Quality Rejection Rate
Multi-level quality checks and fixed inspection plans lower non-conformities.
30%
Procurement Costs
Optimized supplier negotiations and bulk order strategies reduce your overall sourcing expenses.
20%
Manual Processing Time
Automation of sourcing and supplier management significantly reduces time spent on manual tasks.
Optimizing Quality Assurance for Scalable Production
Achieving consistent quality in high-volume production requires strict control over every aspect of the process. Frigate utilizes automated assembly systems and real-time monitoring to ensure uniformity. Statistical process control (SPC) tracks and maintains quality throughout the production cycle. Additionally, advanced inspection methods, including X-ray and optical inspection, detect defects that may not be visible to the naked eye. This systematic approach ensures that all units meet the required specifications, reducing defects and enhancing product reliability.

Get Clarity with Our Manufacturing Insights
- Real Impact
Words from Clients
See how global OEMs and sourcing heads describe their experience with our scalable execution.
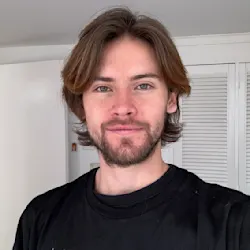
“Quick turnaround and solid quality.”
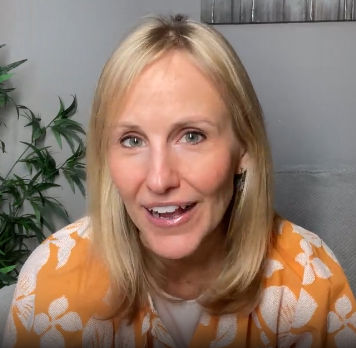
“The instant quote tool saved us time, and the parts were spot-on. Highly recommend Frigate!”
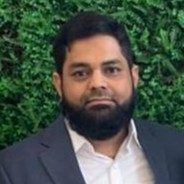
“I would strongly recommend Frigate to anyone who wants to do Rapid Prototyping, and take their ideas to manufacturing. One firm doing all kinds of Product Development!”
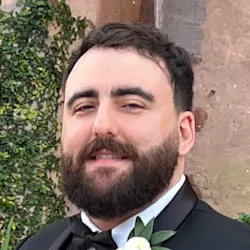
“Great service, fair price, and the parts worked perfectly in our assembly.”
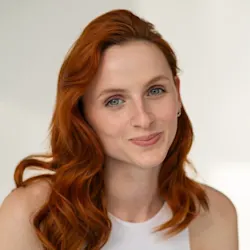
“Top-notch machining and fast shipping. Very satisfied with the results.”
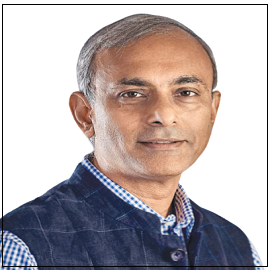
“The next disruption is happening in Prototyping & Manufacturing on-demand and Frigate is leading the way! I personally believe the Frigate's way of IIOT enabled cloud platform with Al.”
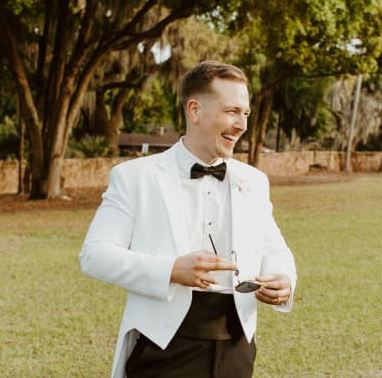
“Frigate delivered high-quality parts at a competitive price. The instant quote tool is a huge plus for us!”

“We appreciate the precision and quality of the machined components in the recent delivery—they meet our specifications perfectly and demonstrate Frigate’s capability for excellent workmanship.”
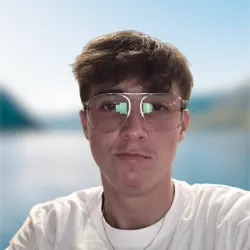
“Flawless execution from quote to delivery.”

“I am absolutely happy to work with supplier like Frigate who were quite proactive & result oriented . Frigate has high willingness team who has strong know how & their passion towards the products & process were absolutely thrilling.”
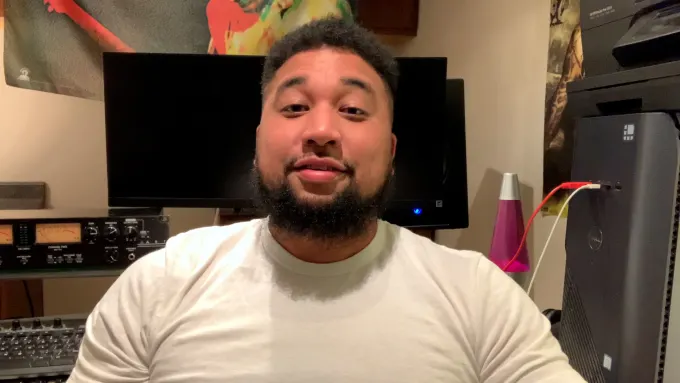
“The precision on these parts is impressive, and they arrived ahead of schedule. Frigate’s process really stands out!”
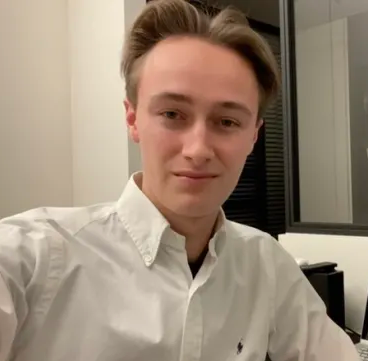
“Parts were exactly as spec’d, and the instant quote made budgeting a breeze.”
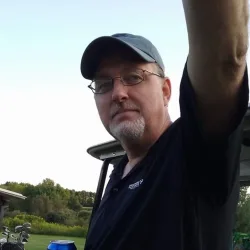
“Good value for the money.”
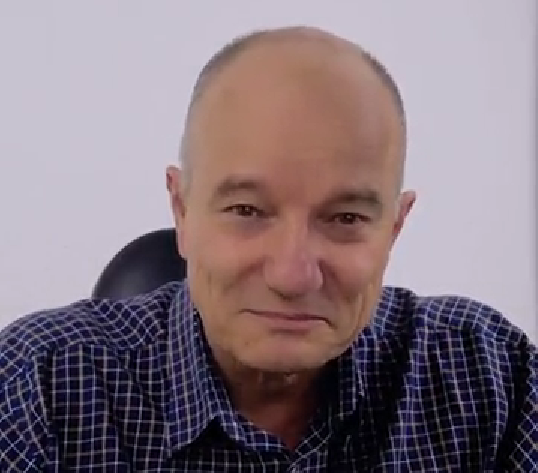
“The finish was perfect, and the team was easy to work with.”

“Working with Frigate has been great. Their proactive, results-driven approach and expertise shine through in every project. It's been a pleasure collaborating with them.”

"We are highly satisfied with the timely delivery and quality of the MIG Welding Cable from Frigate. Their attention to detail, secure packaging, and quick responsiveness stood out. We confidently recommend Frigate Engineering Services Pvt. Ltd. as a reliable manufacturing partner."
Having Doubts? Our FAQ
Check all our Frequently Asked Question
Multi-layer PCBs are designed with precise layer stack-up and controlled impedance. Advanced CAD tools and simulation software verify electrical characteristics, while meticulous attention is paid to placement and layer-to-layer alignment during manufacturing.
We reduce interference by using EMI shielding, controlled impedance routing, and differential signal design. Additionally, grounding strategies and proper layer separation are implemented to ensure minimal signal disruption in sensitive electronic systems.
High-frequency RF circuit assemblies are designed with optimized trace geometry and minimized signal path lengths. We use high-frequency materials, precise impedance matching, and signal integrity testing to ensure reliable performance in demanding RF applications.
Failure analysis uses advanced techniques like X-ray inspection, optical microscopy, and thermal imaging. We use these methods alongside accelerated life testing (ALT) and failure mode effects analysis (FMEA) to identify root causes and prevent future defects.
Solder joint reliability is ensured through controlled soldering processes, such as reflow and wave soldering, combined with precise thermal profiling. Advanced X-ray inspection detects hidden solder defects, ensuring robust connections in fine-pitch and BGA components.
We'd love to Manufacture for you!
Submit the form below and our representative will be in touch shortly.
LOCATIONS
Registered Office
10-A, First Floor, V.V Complex, Prakash Nagar, Thiruverumbur, Trichy-620013, Tamil Nadu, India.
Operations Office
9/1, Poonthottam Nagar, Ramanandha Nagar, Saravanampatti, Coimbatore-641035, Tamil Nadu, India. ㅤ
Other Locations
- Bhilai
- Chennai
- USA
- Germany