Low-Pressure Injection Molding Services
Frigate utilizes low-pressure injection molding for precise material flow and minimal defects. This method ensures high-quality, intricate components with improved dimensional accuracy and finishes.
Our Clients





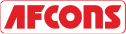

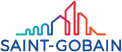


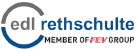

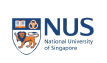
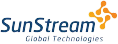

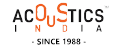




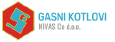
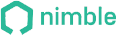
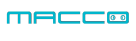












Advantages of Low-Pressure Injection Molding Services
Reduced Cycle Time
Low-pressure injection molding accelerates the production process, reducing cycle times while maintaining high-quality part consistency.
Energy Efficiency
The lower pressure required in this process reduces energy consumption, making it more environmentally friendly and cost-effective for high-volume runs.
Minimized Warping
With reduced internal stresses, parts are less likely to warp or deform during cooling, ensuring dimensional stability.
Improved Tool Life
Lower pressures extend the lifespan of molds and tooling by reducing wear and tear, enhancing long-term cost savings.
Custom Low-Pressure Injection Molding Services
Material waste and dimensional inaccuracies are common challenges in manufacturing. Custom low-pressure injection molding minimizes these issues. It controls material flow precisely, reducing waste and ensuring part consistency. The process improves surface finishes and enhances dimensional accuracy, reducing the need for extra machining. With lower material stress, parts are stronger and more durable. It reduces cycle times, increases energy efficiency, and extends mold life. The result is high-quality, cost-effective molded components with minimal defects.

Get Your Quote Now
- Instant Quotation
- On-Time Delivery
- Affordable Cost
Our Low-Pressure Injection Molding Process






The mold is preheated to ensure uniform material flow and prevent thermal shock during injection.
The material, usually pellets or resin, is loaded into the injection chamber.
Material is injected into the mold cavity under low pressure, ensuring a smooth flow and reducing stress on the material.
The material fills the mold cavity evenly, ensuring that even complex shapes and intricate details are captured accurately.
The injected material cools and solidifies within the mold, forming the desired shape with high dimensional accuracy.
Once cooled, the part is ejected from the mold ready for additional finishing or quality checks.
Low-Pressure Injection Molding Materials
Low-pressure injection molding ensures precise control over complex part geometries. It minimizes material waste while maintaining high strength and dimensional accuracy.
Aluminum alloys like 356 and 380 offer excellent fluidity, strength, and corrosion resistance. These alloys are ideal for complex, lightweight parts in automotive and aerospace, providing fast cycle times and high dimensional accuracy.
Zinc alloys, such as Zamak and ZA-8, are known for superior castability, high surface finish, and dimensional stability. They are ideal for high-precision, corrosion-resistant components in the automotive and electronics industries.
Magnesium alloys are lightweight and have excellent thermal and electrical conductivity. They are used in applications where weight reduction is critical, such as automotive and aerospace, and provide good strength and fatigue resistance.
Brass alloys offer excellent machinability, corrosion resistance, and strength. They are ideal for electrical and decorative components, providing high durability and resistance to stress corrosion cracking.
Stainless steel alloys, like 304 and 316, provide excellent strength, corrosion resistance, and high-temperature performance. These alloys are suitable for parts in harsh environments, such as medical devices and industrial machinery.
Copper alloys, such as C11000, offer exceptional electrical and thermal conductivity. They are ideal for electronics, heat exchangers, and electrical connectors and have excellent corrosion resistance, especially in marine environments.
Nickel alloys like Inconel 718 offer high strength, oxidation resistance, and performance in extreme conditions. They are used in aerospace, power generation, and chemical processing for demanding highly durable applications.
Titanium alloys like Ti-6Al-4V offer high strength-to-weight ratios and corrosion resistance. They are ideal for aerospace & medical applications, producing lightweight, durable components with excellent structural integrity.
Preserve Material Integrity with Low-Pressure Injection Molding
Low-pressure injection molding operates at lower temperatures and pressures, reducing the risk of material degradation. The controlled process preserves material integrity, ensuring mechanical properties remain consistent. It also minimizes defects like warping or discoloration. This method is ideal for high-performance applications where material quality is critical. Frigate’s low-pressure injection molding maintains high part quality with minimal impact on material properties.

Compliance for Low-Pressure Injection Molding Services
Frigate’s Low-Pressure Injection Molding ensures precision with controlled temperature, pressure, and cycle times for efficient, high-quality production. Advanced monitoring systems track every phase, optimizing material flow and minimizing waste. Custom injection pressures and carefully selected materials ensure uniform filling and long-term performance. Continuous environmental monitoring guarantees compliance with industry standards and reduces energy consumption.
Establishes a quality management system for consistent product quality and process improvement.
Confirms materials are free from hazardous substances, meeting European Union environmental and safety directives.
Ensures all materials and processes meet U.S. Food and Drug Administration safety standards for medical applications.
Verifies products meet stringent safety standards for electrical applications and components use.
Demonstrates a commitment to reducing environmental impact through efficient waste management and energy-saving practices.
Meets the automotive industry’s high standards for product quality and continuous improvement in manufacturing.
Ensures products meet European Union safety, health, and environmental protection requirements for manufacturing.

Tolerance for Low-Pressure Injection Molding Services
Precision in mold cavity to ensure tight tolerance for complex features.
Pressure control to optimize material flow while minimizing voids and defects.
Adjustable speed to control material flow and ensure uniform cavity filling.
Variability in material shot size to achieve consistent part weight and dimension.
Critical for controlling material viscosity and ensuring uniform part characteristics.
Precise cooling control to prevent warping and ensure part stability.
Shrinkage control to ensure parts remain within required dimensions post-molding.
Hold time precision to ensure proper packing of the mold and part uniformity.
Maintains optimal flow pressure to avoid incomplete filling or flash.
Tolerance on flash removal to maintain clean edges and reduce post-processing.
Precision in surface finish to ensure minimal defects and improve part aesthetics.
Ensures tight parting line with no misalignment between mold halves.
Control over gate vestige size to avoid unwanted material buildup in parts.
Minimizing internal voids to maintain structural integrity and part strength.

Quality Testing Standards for Low-Pressure Injection Molding Services
Monitors uniformity of cavity pressure during the filling process to ensure consistent part quality.
Measures mold deflection during injection to ensure dimensional accuracy and prevent part warping.
Assesses the viscosity of the material to optimize injection conditions and minimize defects.
Evaluates the material’s resistance to thermal and mechanical cycling for durability and longevity.
Measures the time taken to fill the mold cavity, ensuring proper material flow and timing.
Evaluates the strength, elongation, and impact resistance of the molded parts.
Measures the temperature at which the material deforms under a specified load, indicating thermal stability.
Ensures consistency in part weight by analyzing variations and optimizing the molding process.
Measures heat transfer characteristics of the molded part, crucial for high-performance applications.
Ensures the surface quality of the mold cavity, checking for wear or damage that could affect part finish.
Tracks fluctuations in injection time, ensuring stable and repeatable molding cycles.
Measures the release of gases during molding, ensuring part cleanliness and material stability.
Monitors the dimensional stability of parts post-cooling to prevent warping or shrinkage.
Measures the material’s resistance to elastic deformation under stress, ensuring structural integrity.
Optimizing Automotive Parts with Low-Pressure Injection Molding
Multi-material injection molding enables the integration of different materials, such as rigid plastics and flexible elastomers, into a single part. This process ensures strong material bonding and precise dimensional accuracy, eliminating the need for secondary assembly. By optimizing performance, reducing production time, and lowering costs, multi-material molding improves the efficiency of automotive component manufacturing.







Industries We Serve
- Solid Progress
Our Manufacturing Metrics
Frigate brings stability, control, and predictable performance to your sourcing operations through a structured multi-vendor system.
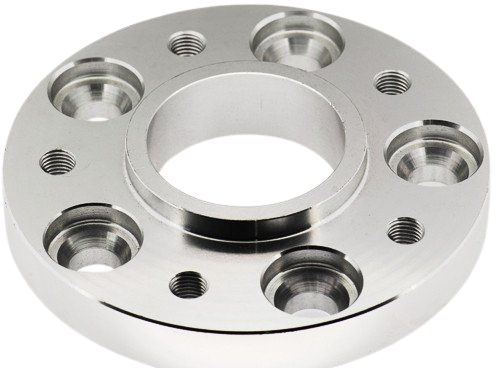
2.8X
Sourcing Cycle Speed
Frigate’s pre-qualified network shortens decision time between RFQ and PO placement.
94%
On-Time Delivery Rate
Structured planning windows and logistics-linked schedules improve project-level delivery reliability.
4X
Multi-Part Consolidation
We enable part family batching across suppliers to reduce fragmentation.
22%
Quality Rejection Rate
Multi-level quality checks and fixed inspection plans lower non-conformities.
30%
Procurement Costs
Optimized supplier negotiations and bulk order strategies reduce your overall sourcing expenses.
20%
Manual Processing Time
Automation of sourcing and supplier management significantly reduces time spent on manual tasks.
Reduce Tooling Costs and Extend Mold Life with Low-Pressure Injection Molding
Low-pressure injection molding applies lower pressure, reducing strain on tooling. This results in extended mold life and fewer maintenance needs. The controlled pressure optimizes material flow, increasing efficiency. Frigate’s approach improves material yield, reducing the need for expensive tooling. It lowers overall production costs, especially for complex parts made with specialized materials.

Get Clarity with Our Manufacturing Insights
- Real Impact
Words from Clients
See how global OEMs and sourcing heads describe their experience with our scalable execution.
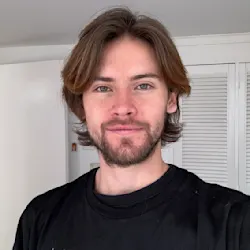
“Quick turnaround and solid quality.”
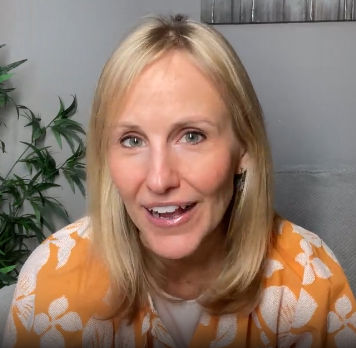
“The instant quote tool saved us time, and the parts were spot-on. Highly recommend Frigate!”
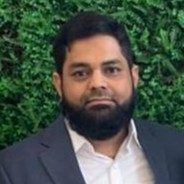
“I would strongly recommend Frigate to anyone who wants to do Rapid Prototyping, and take their ideas to manufacturing. One firm doing all kinds of Product Development!”
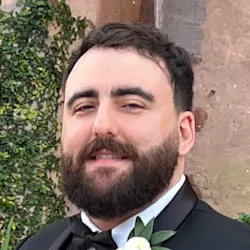
“Great service, fair price, and the parts worked perfectly in our assembly.”
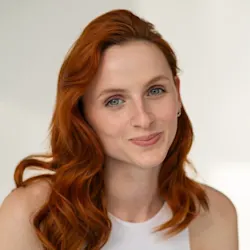
“Top-notch machining and fast shipping. Very satisfied with the results.”
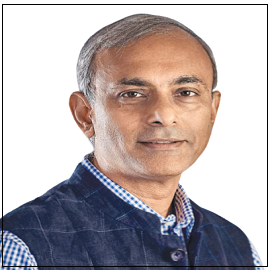
“The next disruption is happening in Prototyping & Manufacturing on-demand and Frigate is leading the way! I personally believe the Frigate's way of IIOT enabled cloud platform with Al.”
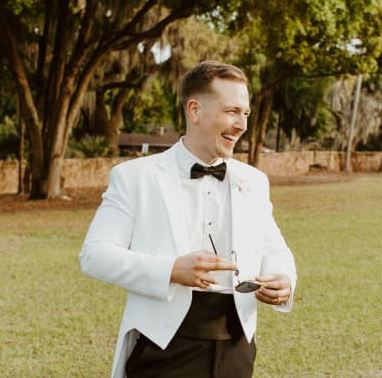
“Frigate delivered high-quality parts at a competitive price. The instant quote tool is a huge plus for us!”

“We appreciate the precision and quality of the machined components in the recent delivery—they meet our specifications perfectly and demonstrate Frigate’s capability for excellent workmanship.”
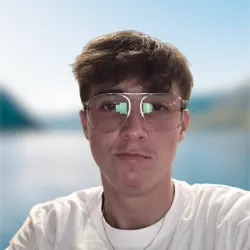
“Flawless execution from quote to delivery.”

“I am absolutely happy to work with supplier like Frigate who were quite proactive & result oriented . Frigate has high willingness team who has strong know how & their passion towards the products & process were absolutely thrilling.”
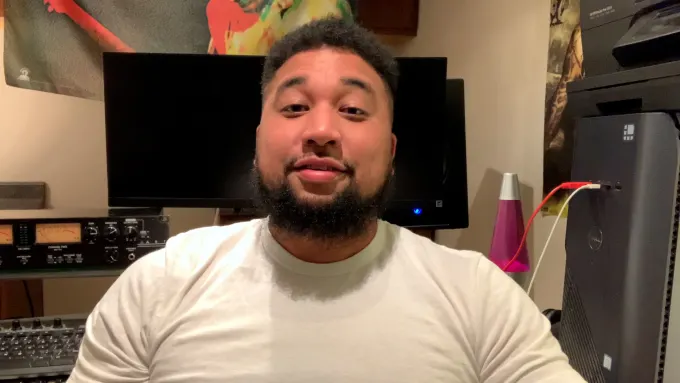
“The precision on these parts is impressive, and they arrived ahead of schedule. Frigate’s process really stands out!”
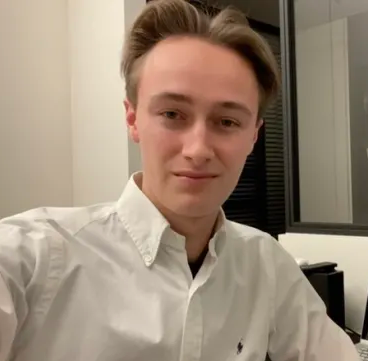
“Parts were exactly as spec’d, and the instant quote made budgeting a breeze.”
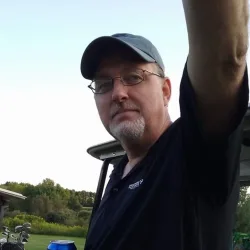
“Good value for the money.”
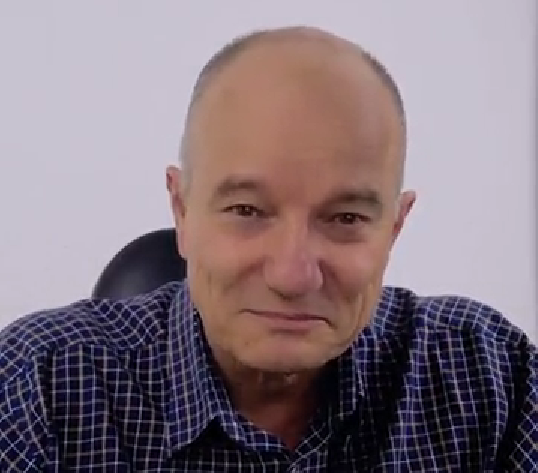
“The finish was perfect, and the team was easy to work with.”

“Working with Frigate has been great. Their proactive, results-driven approach and expertise shine through in every project. It's been a pleasure collaborating with them.”

"We are highly satisfied with the timely delivery and quality of the MIG Welding Cable from Frigate. Their attention to detail, secure packaging, and quick responsiveness stood out. We confidently recommend Frigate Engineering Services Pvt. Ltd. as a reliable manufacturing partner."
Having Doubts? Our FAQ
Check all our Frequently Asked Question
Low-pressure injection molding applies less stress to the mold than traditional high-pressure processes. This reduces wear and tear, leading to longer mold life and fewer maintenance intervals, ultimately reducing costs.
Lower injection pressure makes the material flow more smoothly into thin or complex mold cavities without creating defects like short shots or flash. This improves the consistency of detailed parts, especially in high-precision applications.
Yes, low-pressure injection molding is ideal for high-viscosity materials. It allows them to flow evenly into molds at reduced speeds. The controlled pressure helps maintain part integrity and prevents issues like incomplete fills or overpacking.
The process operates at lower temperatures and pressures, reducing the thermal stress applied to the material. This minimizes the risk of material degradation, ensuring that the final product retains optimal mechanical properties and surface finish.
The slower injection speed and reduced pressure allow the material to solidify more evenly, compensating for varying shrinkage rates. This ensures uniform part dimensions, which is particularly important for complex, multi-cavity molds.
We'd love to Manufacture for you!
Submit the form below and our representative will be in touch shortly.
LOCATIONS
Registered Office
10-A, First Floor, V.V Complex, Prakash Nagar, Thiruverumbur, Trichy-620013, Tamil Nadu, India.
Operations Office
9/1, Poonthottam Nagar, Ramanandha Nagar, Saravanampatti, Coimbatore-641035, Tamil Nadu, India. ㅤ
Other Locations
- Bhilai
- Chennai
- USA
- Germany