Thermoset Injection Molding Services
Frigate’s Thermoset Injection Molding ensures high thermal stability and precision. This process creates durable, dimensionally stable parts with excellent mechanical strength.
Our Clients





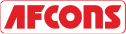

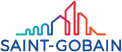


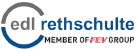

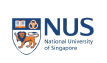
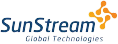

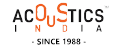




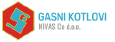
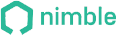
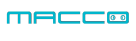












Advantages of Thermoset Injection Molding Services
Enhanced Chemical Resistance
Thermoset injection molding produces parts that resist corrosion, solvents, and acids, making them suitable for harsh chemical environments.
Low Shrinkage
Thermoset molding minimizes post-production shrinkage, ensuring consistent part sizes and reducing the need for rework or adjustments.
Better Heat Resistance
Unlike thermoplastics, thermoset parts maintain structural integrity under high heat, making them ideal for engine components and electrical housings.
Improved Surface Finish
Thermoset materials allow for a smooth, glossy finish on molded parts, reducing the need for additional finishing processes.
Custom Thermoset Injection Molding for Precision Components
Industries often struggle with parts that can’t withstand high temperatures or harsh environments. Custom thermoset injection molding offers a solution by creating durable, high-performance components. These parts provide excellent thermal stability, chemical resistance, and mechanical strength. The process ensures precise, consistent results with minimal shrinkage. Thermoset materials are ideal for applications needing wear resistance, electrical insulation, and long-term reliability. Frigate’s thermoset injection molding delivers efficient, high-quality solutions for demanding industrial applications.

Get Your Quote Now
- Instant Quotation
- On-Time Delivery
- Affordable Cost
Our Thermoset Injection Molding Process






Thermoset resins are mixed with curing agents and other additives to prepare a uniform, flowable material for molding.
The prepared thermoset material is injected into a heated mold cavity under high pressure, filling the mold’s shape.
The mold is maintained at a specific temperature to initiate a chemical reaction, curing the thermoset material into a rigid, durable form.
After curing, the mold is cooled to solidify the part and maintain its shape and structural integrity.
Once it has cooled and hardened, the molded part is removed from the mold using mechanical ejectors.
Any excess material or flash is trimmed, and the part is inspected for quality, fit, and finish.
Thermoset Injection Molding Materials
Pneumatic metal forming shapes metal components with high precision under pressure. It’s essential for producing durable, high-performance parts for demanding industries.
These alloys offer high strength, low weight, and excellent corrosion resistance. They maintain good formability under high pressure, making them ideal for automotive and aerospace components that require precision and durability.
HSLA steels like 304 and 4340 provide high yield and tensile strength. They resist deformation under high pressures, making them suitable for heavy-duty applications like automotive suspension and structural parts.
Known for high strength, thermal conductivity, and wear resistance, beryllium copper alloys excel in aerospace and military applications. They offer excellent fatigue resistance and are ideal for high-stress components like electrical connectors and bearings.
Titanium alloys are lightweight yet strong, with exceptional resistance to heat and corrosion. These properties make them ideal for aerospace and medical parts, especially when complex shapes and high performance are required.
Magnesium alloys offer excellent formability and low density. They are used in the automotive and aerospace industries for lightweight components, but due to their sensitivity to oxidation, they require precise control during forming.
Nickel alloys resist extreme temperatures and corrosion. They are ideal for high-performance applications, such as gas turbines and aerospace components, where reliability under thermal and mechanical stress is critical.
Copper alloys, like beryllium copper and phosphor bronze, provide excellent electrical conductivity and corrosion resistance. These alloys are commonly used for electrical contacts and heat exchangers that require high-performance forming under pressure.
Superalloys offer superior creep, fatigue, and oxidation resistance. They are used in extreme conditions, such as jet engines and gas turbines, where high thermal and mechanical stresses are present.
Optimizing Energy Efficiency in Pneumatic Metal Forming
Pneumatic metal forming requires significant energy, especially during large-scale production. If energy use isn’t controlled, this results in higher operational costs. Frigate minimizes energy consumption by utilizing energy-efficient machines and systems. Advanced process controls ensure that power is used only when needed. Equipment is regularly maintained to avoid energy wastage from malfunctions. These measures ensure consistent performance while keeping operational costs lower. Optimizing energy usage improves cost-effectiveness over extended production runs.

Compliance for Thermoset Injection Molding Services
Frigate’s thermoset injection molding complies with critical industry standards to ensure top-tier performance and precision in complex applications. Adherence to these regulations is vital for optimizing efficiency, reliability, and environmental sustainability in high-demand sectors.
Establishes a robust quality management system, driving consistent performance, traceability, and process optimization for thermoset parts.
Integrates sustainable practices in production, reducing energy consumption and ensuring eco-friendly waste management in thermoset molding.
Certifies thermoset materials' flame retardancy, which is crucial for high-risk electrical and electronic components to prevent fire hazards.
Guarantees compliance with European chemical safety regulations, ensuring thermoset products are free of restricted substances.
Limits the presence of hazardous substances in thermoset parts, ensuring compliance for electronics and medical device industries.
Verifies that thermoset materials are non-toxic and safe for direct contact with food and pharmaceuticals.
Focuses on automotive-specific quality standards, ensuring thermoset injection molding components meet rigorous durability and precision criteria.

Tolerance for Thermoset Injection Molding Services
Accounts for dimensional changes during cooling, essential for high-precision components.
Ensures uniform pressure across the mold cavity to prevent defects and ensure consistent part quality.
Controls the rate at which material enters the mold, crucial for minimizing defects like short shots.
Defines the distance the material travels before solidifying; ensures uniform fill in complex geometries.
Time control for injecting thermoset material, directly affecting part density and surface finish.
Critical for cross-linking efficiency and optimal mechanical properties of thermoset components.
Measures the material’s ability to withstand tensile forces after curing, ensuring high strength in critical applications.
Monitors material expansion during temperature shifts, crucial for maintaining dimensional integrity under heat.
Evaluates the ability of thermoset materials to retain shape after compression, ensuring long-term performance.
Indicates material resistance to indentation; essential for applications requiring high durability.
Critical for defining temperature stability and dimensional stability during thermal cycles.
Describes the flowability of thermoset material under injection pressure, affecting part consistency and quality.
Defines the temperature at which the material softens under a load, ensuring resistance to deformation under operational conditions.

Quality Testing Standards for Thermoset Injection Molding Services
Measures the viscosity of the molten thermoset material, which helps in assessing processability during injection molding.
Determines the flow resistance of thermoset material at elevated temperatures, essential for optimizing injection molding parameters.
Measures the material's ability to resist electrical breakdown under stress, ensuring electrical safety in insulating applications.
Evaluates the material’s weight loss at high temperatures, indicating stability and suitability for high-heat applications.
Tests the material’s ability to resist brittle fracture under low temperatures, critical for parts exposed to extreme cold environments.
Measures the absorption of moisture by the material, which can impact dimensional stability and mechanical properties.
Tests the material's electrical conductivity on the surface, ensuring suitability for applications requiring insulative properties.
Assesses the material’s ability to withstand repeated loading and unloading, ensuring durability in dynamic applications.
Evaluates material shrinkage characteristics under varying pressure and temperature conditions during curing, essential for part accuracy.
Measures the material’s expansion or contraction with temperature fluctuations, crucial for components used in high-temperature environments.
Assesses the material's resistance to burning in an oxygen-rich atmosphere, important for safety-critical applications in aerospace or automotive sectors.
Tests the temperature at which the material becomes brittle and fails, critical for low-temperature performance.
Simulates aging under environmental stress conditions like UV exposure, heat, and humidity, assessing long-term durability.
Improving Heat Resistance for Long-lasting Electrical Parts
Electrical component manufacturers often face insulation, heat resistance, and dimensional stability challenges. Thermoset injection molding addresses these issues by providing components with superior durability and thermal stability. This molding process offers precise control over material properties, ensuring reliable performance in high-temperature environments. Thermoset materials are ideal for electrical parts, offering excellent resistance to electrical conductivity, moisture, and chemicals. With high precision, the process ensures consistent, defect-free parts, reducing scrap and increasing production efficiency. This allows for reliable, long-lasting electrical components that meet stringent industry standards.






Industries We Serve
- Solid Progress
Our Manufacturing Metrics
Frigate brings stability, control, and predictable performance to your sourcing operations through a structured multi-vendor system.
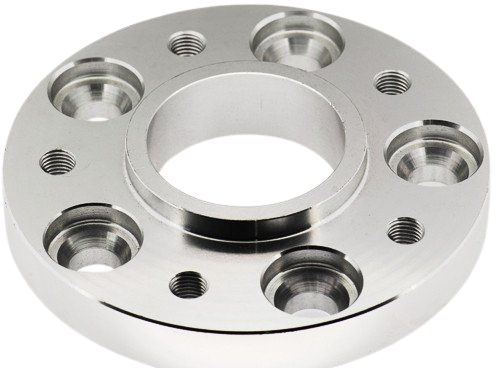
2.8X
Sourcing Cycle Speed
Frigate’s pre-qualified network shortens decision time between RFQ and PO placement.
94%
On-Time Delivery Rate
Structured planning windows and logistics-linked schedules improve project-level delivery reliability.
4X
Multi-Part Consolidation
We enable part family batching across suppliers to reduce fragmentation.
22%
Quality Rejection Rate
Multi-level quality checks and fixed inspection plans lower non-conformities.
30%
Procurement Costs
Optimized supplier negotiations and bulk order strategies reduce your overall sourcing expenses.
20%
Manual Processing Time
Automation of sourcing and supplier management significantly reduces time spent on manual tasks.
Ensuring Precise Cooling to Prevent Defects in Metal Parts
Post-forming cooling is critical to part quality. If cooling is not properly controlled, internal stresses can develop, leading to warping, cracking, or dimensional inaccuracy. Frigate uses controlled cooling systems to manage the cooling rate precisely. The cooling rate is adjusted to match material properties and part geometry. Advanced cooling technology ensures uniform temperature distribution across the part. This reduces the risk of defects and ensures parts maintain their strength and dimensional integrity.

Get Clarity with Our Manufacturing Insights
- Real Impact
Words from Clients
See how global OEMs and sourcing heads describe their experience with our scalable execution.
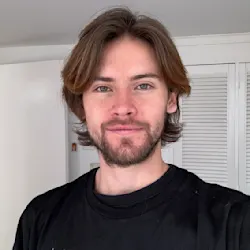
“Quick turnaround and solid quality.”
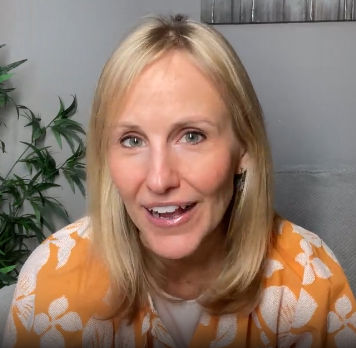
“The instant quote tool saved us time, and the parts were spot-on. Highly recommend Frigate!”
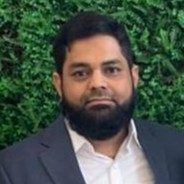
“I would strongly recommend Frigate to anyone who wants to do Rapid Prototyping, and take their ideas to manufacturing. One firm doing all kinds of Product Development!”
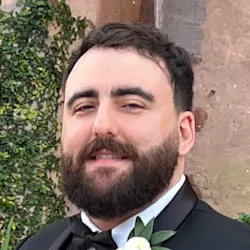
“Great service, fair price, and the parts worked perfectly in our assembly.”
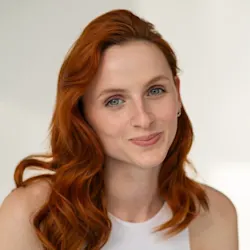
“Top-notch machining and fast shipping. Very satisfied with the results.”
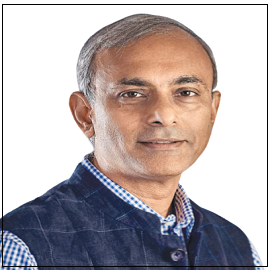
“The next disruption is happening in Prototyping & Manufacturing on-demand and Frigate is leading the way! I personally believe the Frigate's way of IIOT enabled cloud platform with Al.”
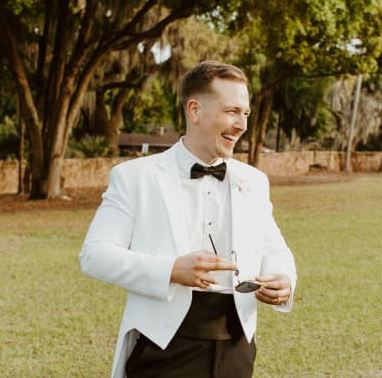
“Frigate delivered high-quality parts at a competitive price. The instant quote tool is a huge plus for us!”

“We appreciate the precision and quality of the machined components in the recent delivery—they meet our specifications perfectly and demonstrate Frigate’s capability for excellent workmanship.”
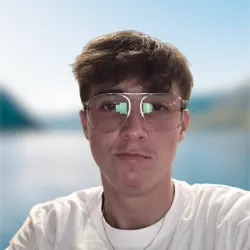
“Flawless execution from quote to delivery.”

“I am absolutely happy to work with supplier like Frigate who were quite proactive & result oriented . Frigate has high willingness team who has strong know how & their passion towards the products & process were absolutely thrilling.”
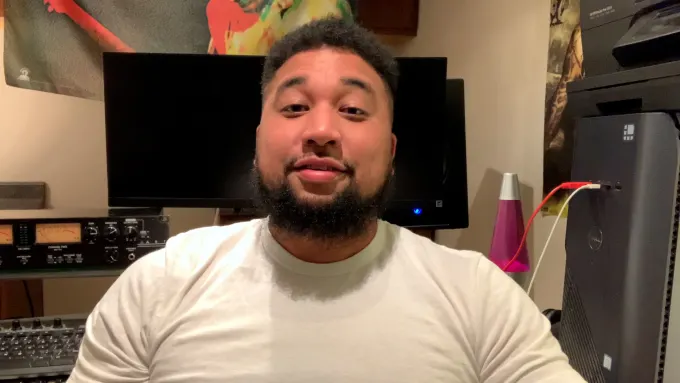
“The precision on these parts is impressive, and they arrived ahead of schedule. Frigate’s process really stands out!”
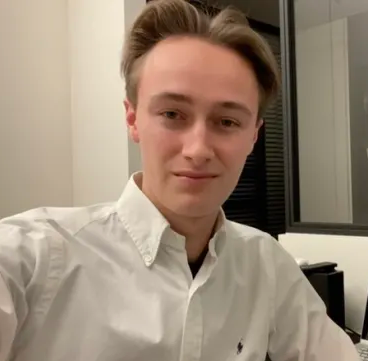
“Parts were exactly as spec’d, and the instant quote made budgeting a breeze.”
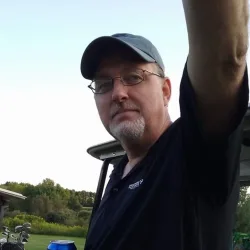
“Good value for the money.”
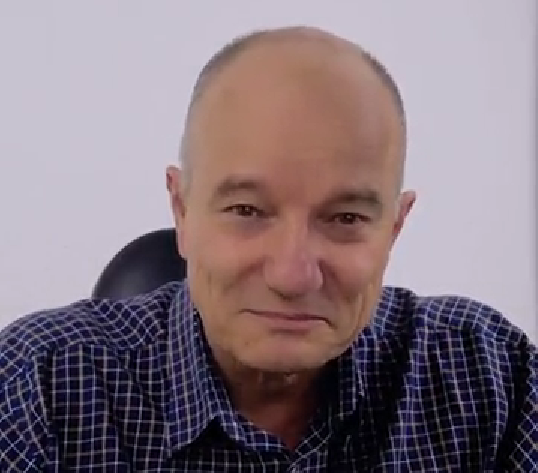
“The finish was perfect, and the team was easy to work with.”

“Working with Frigate has been great. Their proactive, results-driven approach and expertise shine through in every project. It's been a pleasure collaborating with them.”

"We are highly satisfied with the timely delivery and quality of the MIG Welding Cable from Frigate. Their attention to detail, secure packaging, and quick responsiveness stood out. We confidently recommend Frigate Engineering Services Pvt. Ltd. as a reliable manufacturing partner."
Having Doubts? Our FAQ
Check all our Frequently Asked Question
Frigate uses advanced temperature and pressure monitoring systems to control the curing process precisely. This ensures consistent material properties and dimensional accuracy across all parts, minimizing defects and variations.
Frigate uses temperature-controlled injection systems and optimized cycle times to avoid material degradation. This prevents the thermal breakdown of thermoset materials, ensuring the parts maintain their structural integrity and performance.
Frigate’s precision tooling and advanced molding techniques allow for producing intricate and complex shapes. The carefully controlled molding process ensures that even challenging geometries are formed with high accuracy and minimal material waste.
Frigate utilizes automated systems for mold monitoring, material mixing, and process adjustments. This guarantees consistent part quality, even during high-volume production runs, reducing variability and scrap rates.
Frigate employs a controlled post-molding curing process to complete the cross-linking of thermoset materials. Coupled with a precise cooling phase, this ensures optimal hardness, strength, and thermal stability in the final molded parts.
We'd love to Manufacture for you!
Submit the form below and our representative will be in touch shortly.
LOCATIONS
Registered Office
10-A, First Floor, V.V Complex, Prakash Nagar, Thiruverumbur, Trichy-620013, Tamil Nadu, India.
Operations Office
9/1, Poonthottam Nagar, Ramanandha Nagar, Saravanampatti, Coimbatore-641035, Tamil Nadu, India. ㅤ
Other Locations
- Bhilai
- Chennai
- USA
- Germany