Pneumatic Metal Forming Services
Frigate uses pneumatic pressure to achieve controlled metal flow in forming processes. The method enhances part consistency and reduces cycle time in high-volume production.
Our Clients





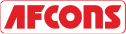

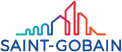


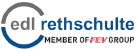

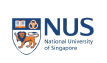
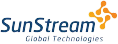

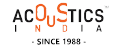




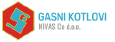
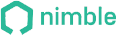
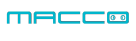












Advantages of Pneumatic Metal Forming Services
Reduced Tooling Costs
Pneumatic forming requires fewer specialized tools than other forming methods, lowering overall tooling and setup costs.
Minimal Heat Generation
Unlike traditional forging, pneumatic metal forming services generates less heat, reducing the risk of material degradation and thermal distortion.
Improved Cycle Time Control
Pneumatic systems can be finely tuned for precise cycle times, optimizing throughput while maintaining high-quality part consistency.
Flexibility in Materials
Pneumatic forming works well with a wide range of metals, from soft alloys to harder, high-strength materials, offering broad application.
Custom Pneumatic Metal Forming for Precision and Efficiency
Custom pneumatic metal forming services offers a highly controlled method for shaping metals with precision, addressing common challenges such as dimensional inconsistency and extended production times. By applying compressed air for deformation, this technique enables tight control over material flow, ensuring parts meet strict tolerance requirements. It is particularly effective for producing complex geometries, as it minimizes material waste and reduces the need for costly tooling. The process also generates minimal heat, preserving the structural integrity of metals and preventing distortion.

Get Your Quote Now
- Instant Quotation
- On-Time Delivery
- Affordable Cost
Our Pneumatic Metal Forming Process






Depending on the material type, the metal to be formed is prepped by heating or cutting it to the desired size.
A forming die is installed to match the final part shape. The die ensures the metal takes on the precise geometry during shaping.
Compressed air is directed into the system, and controlled pressure is applied to the metal. This pressure causes the metal to flow and form into the shape of the die.
The air pressure is carefully controlled to achieve the desired material flow and ensure the part's uniform thickness and dimensional accuracy.
After forming, the part is cooled, allowing it to solidify in its new shape. Depending on the material, the cooling process may be natural or accelerated.
The formed part undergoes inspection for dimensional accuracy and quality. Any necessary finishing processes, such as trimming or surface treatment, are performed to meet final specifications.
Pneumatic Metal Forming Materials
Pneumatic metal forming uses compressed air for precise metal shaping. It ensures uniform material flow and tight dimensional accuracy for complex parts.
Aluminum alloys like 6061 and 7075 are lightweight, corrosion-resistant, and easy to form at low temperatures. Their high strength-to-weight ratio makes them ideal for aerospace and automotive applications, where minimal heat input is critical to avoid distortion.
Steel alloys offer exceptional strength and toughness, including carbon steels (AISI 1045) and stainless steels (304, 316). Pneumatic forming of steel requires precise control to prevent thermal stress and ensure high-quality components for automotive and industrial use.
Copper and alloys like brass (C36000) and bronze (C51000) are known for excellent electrical conductivity and corrosion resistance. The pneumatic forming of these materials ensures smooth, precise shaping and is ideal for electrical connectors, plumbing, and decorative applications.
Titanium alloys such as Ti-6Al-4V provide high strength and corrosion resistance at elevated temperatures. Pneumatic forming allows precise shaping while maintaining material properties, and it is commonly used in aerospace and medical industries for lightweight, durable components.
Magnesium alloys, like AZ91D, are the lightest structural metals used in automotive and aerospace industries. Pneumatic forming minimizes oxidation and ensures consistent material flow, making them ideal for weight-sensitive applications requiring strength and performance.
Tool steels like D2 and S7 are used for high-wear applications. Pneumatic forming enables precise shaping of these hard steels while maintaining their toughness and hardness, making them ideal for cutting, stamping, and forming tools.
Nickel alloys, such as Inconel 718, offer high resistance to heat and corrosion. Pneumatic forming ensures the precise shaping of these materials for critical aerospace and power generation applications, maintaining their structural integrity under extreme conditions.
Enhancing Alloy Durability with Stable Temperature Control
Certain alloys, like titanium, require strict temperature control in pneumatic metal forming. Frigate uses precise temperature management systems to ensure stable forming conditions. Deviations from optimal temperatures can alter the material’s microstructure, compromising key properties such as strength, fatigue resistance, and corrosion resistance. Maintaining accurate temperatures is essential to prevent performance degradation in these sensitive materials.

Compliance for Pneumatic Metal Forming Services
Frigate’s Pneumatic Metal Forming services fully comply with critical industry standards to maintain precision, reliability, and safety. We rigorously follow regulations that ensure quality control and minimize risks during pneumatic forming operations. Our focus on compliance guarantees high-quality, durable metal components that meet or exceed customer specifications.
Compliance Requirements for Pneumatic Metal Forming
Ensures consistent quality management and continuous improvement in production and operational processes.
Automotive industry-specific standard ensuring reliable manufacturing of metal components with strict quality and process control.
Establishes safety guidelines for the operation of pneumatic machinery, ensuring a safe working environment.
Defines safety requirements for forming and stamping presses, including pneumatic systems, to prevent workplace accidents.
Restricts the use of hazardous substances in electrical and electronic equipment for environmental and health safety.
Regulates chemicals used in production, ensuring materials are safe and environmentally compliant.
Ensures functional safety of electrical and electronic systems in pneumatic machinery, minimizing operational risks.

Tolerance for Pneumatic Metal Forming Services
Deviation in material shape after forming due to elastic recovery of the metal.
Variation in the force applied by the punch during forming, affecting accuracy.
The amount of material deformation due to applied forces during the forming process.
Tolerance in part dimensions due to wear of the forming die over time.
Deviation in the depth of the punch stroke, affecting part consistency.
Variation in the material’s tensile strength after forming, indicating material consistency.
Uniformity in the radii of formed corners, essential for component fit and function.
Consistency of material thickness after forming, particularly in deep-drawn parts.
Deviation in the parallelism of formed flanges relative to the part's base surface.
Influence of forming speed on material properties and dimensional accuracy.
Deviation from a straight line after forming, especially in long, thin parts.
Tolerance in the gap between die halves during the forming cycle, affecting part consistency.

Quality Testing Standards for Pneumatic Metal Forming Services
Monitors the consistency of pneumatic forming speed and its impact on part quality.
Measures material hardness to evaluate the effect of work hardening during the forming process.
Detects heat distribution and its impact on material properties during forming.
Measures the uniformity of pneumatic pressure applied during the forming process.
Ensures precise alignment of die components to minimize dimensional errors in the final product.
Tests the lubrication between die and material to reduce friction and wear, ensuring part quality.
Analyzes internal stresses within the material after forming that can affect its performance.
Identifies the presence and size of burrs formed at the edges, ensuring smooth finishes.
Measures the time it takes for the material to completely fill the die cavity, affecting production efficiency.
Evaluates how well the material flows during forming, optimizing die design and process parameters.
Measures the strength of bonded materials, crucial for composite or layered forming processes.
Measures any unintended distortion or shape change in the part during or after the forming process.
Shaping the Future of Aerospace with Precision Pneumatic Forming
Aerospace components require precision, strength, and lightweight design, but traditional methods often fall short. Pneumatic metal forming services meets these demands using controlled air pressure to accurately shape complex, high-tolerance parts. This technique ensures lightweight durability and is ideal for intricate designs and thin-walled structures. Frigate’s pneumatic forming services enhance production efficiency and material integrity, effectively meeting aerospace standards.






Industries We Serve
- Solid Progress
Our Manufacturing Metrics
Frigate brings stability, control, and predictable performance to your sourcing operations through a structured multi-vendor system.
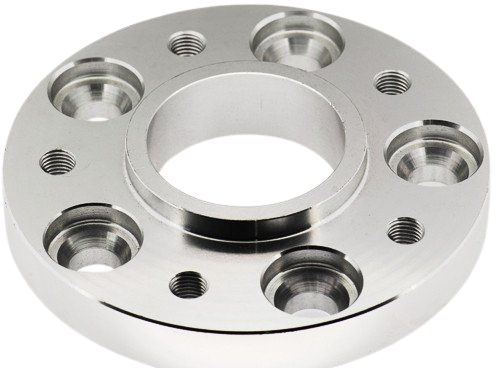
2.8X
Sourcing Cycle Speed
Frigate’s pre-qualified network shortens decision time between RFQ and PO placement.
94%
On-Time Delivery Rate
Structured planning windows and logistics-linked schedules improve project-level delivery reliability.
4X
Multi-Part Consolidation
We enable part family batching across suppliers to reduce fragmentation.
22%
Quality Rejection Rate
Multi-level quality checks and fixed inspection plans lower non-conformities.
30%
Procurement Costs
Optimized supplier negotiations and bulk order strategies reduce your overall sourcing expenses.
20%
Manual Processing Time
Automation of sourcing and supplier management significantly reduces time spent on manual tasks.
Reliable Alignment in Multi-Stage Forming Processes
Forming multi-stage components with tight tolerances is technically challenging, especially for complex geometries. Frigate’s pneumatic forming process uses carefully regulated parameters at each stage. This approach ensures alignment across stages to prevent misalignment or material failure. By maintaining dimensional accuracy throughout, Frigate enables the production of intricate, high-performance parts. This precision is vital for meeting stringent demands in advanced applications.

Get Clarity with Our Manufacturing Insights
- Real Impact
Words from Clients
See how global OEMs and sourcing heads describe their experience with our scalable execution.
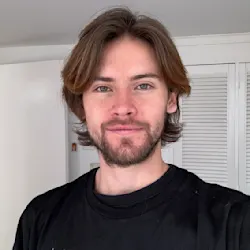
“Quick turnaround and solid quality.”
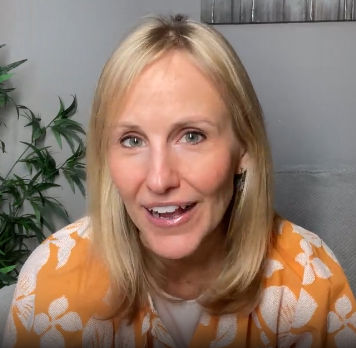
“The instant quote tool saved us time, and the parts were spot-on. Highly recommend Frigate!”
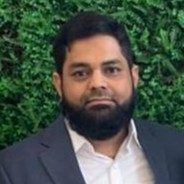
“I would strongly recommend Frigate to anyone who wants to do Rapid Prototyping, and take their ideas to manufacturing. One firm doing all kinds of Product Development!”
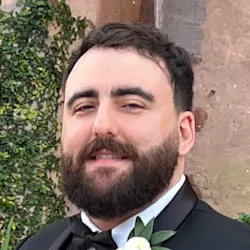
“Great service, fair price, and the parts worked perfectly in our assembly.”
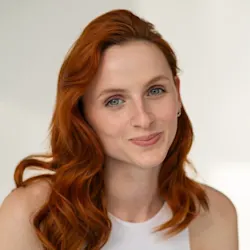
“Top-notch machining and fast shipping. Very satisfied with the results.”
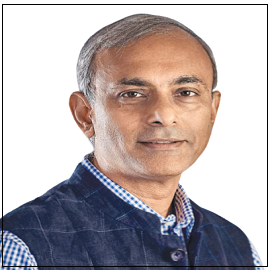
“The next disruption is happening in Prototyping & Manufacturing on-demand and Frigate is leading the way! I personally believe the Frigate's way of IIOT enabled cloud platform with Al.”
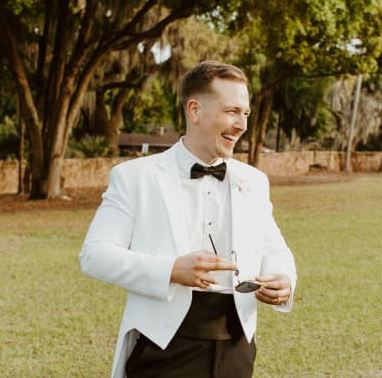
“Frigate delivered high-quality parts at a competitive price. The instant quote tool is a huge plus for us!”

“We appreciate the precision and quality of the machined components in the recent delivery—they meet our specifications perfectly and demonstrate Frigate’s capability for excellent workmanship.”
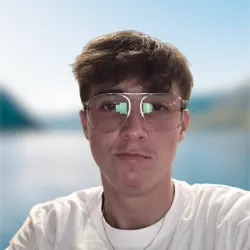
“Flawless execution from quote to delivery.”

“I am absolutely happy to work with supplier like Frigate who were quite proactive & result oriented . Frigate has high willingness team who has strong know how & their passion towards the products & process were absolutely thrilling.”
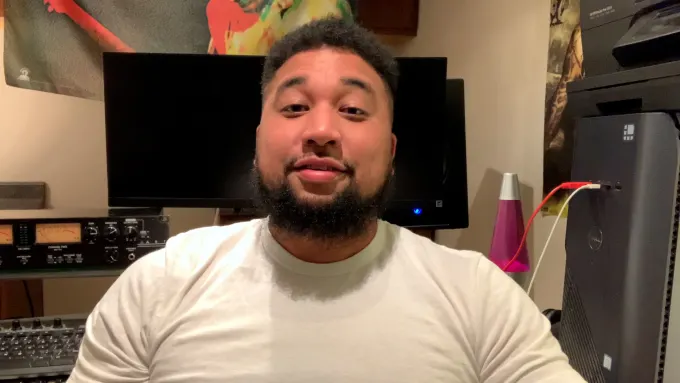
“The precision on these parts is impressive, and they arrived ahead of schedule. Frigate’s process really stands out!”
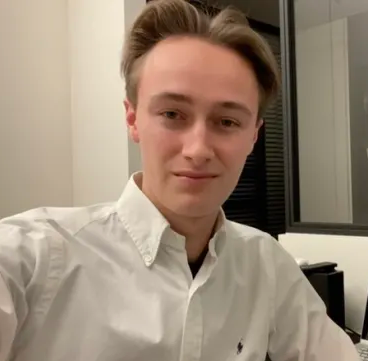
“Parts were exactly as spec’d, and the instant quote made budgeting a breeze.”
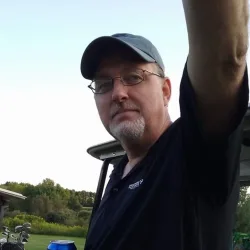
“Good value for the money.”
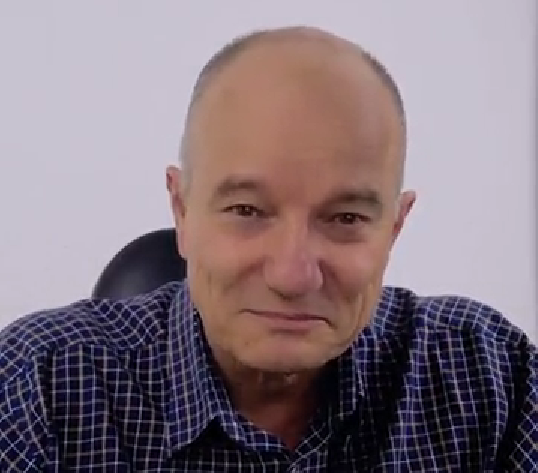
“The finish was perfect, and the team was easy to work with.”

“Working with Frigate has been great. Their proactive, results-driven approach and expertise shine through in every project. It's been a pleasure collaborating with them.”

"We are highly satisfied with the timely delivery and quality of the MIG Welding Cable from Frigate. Their attention to detail, secure packaging, and quick responsiveness stood out. We confidently recommend Frigate Engineering Services Pvt. Ltd. as a reliable manufacturing partner."
Having Doubts? Our FAQ
Check all our Frequently Asked Question
Frigate uses advanced pressure-regulation systems to control the compressed air, ensuring uniform material flow. This eliminates issues like uneven thickness and dimensional inaccuracies in complex parts.
Frigate applies controlled pressure and maintains optimal cooling rates, minimizing heat generation. This prevents warping or distortion in high-strength materials such as steel and titanium during forming.
Frigate’s pneumatic forming technology allows precise shaping of intricate geometries with tight tolerances. The ability to adjust air pressure ensures accurate deformation of complex parts without compromising material integrity.
Yes, Frigate’s pneumatic metal forming process is optimized for high-volume production. Advanced automation and pressure control systems ensure consistent quality and high throughput, even for large-scale manufacturing runs.
Frigate uses pneumatic forming to control material flow precisely, reducing scrap and optimizing material usage. The efficient deformation process ensures minimal material is wasted, enhancing cost-effectiveness for custom parts.
We'd love to Manufacture for you!
Submit the form below and our representative will be in touch shortly.
LOCATIONS
Registered Office
10-A, First Floor, V.V Complex, Prakash Nagar, Thiruverumbur, Trichy-620013, Tamil Nadu, India.
Operations Office
9/1, Poonthottam Nagar, Ramanandha Nagar, Saravanampatti, Coimbatore-641035, Tamil Nadu, India. ㅤ
Other Locations
- Bhilai
- Chennai
- USA
- Germany