Vacuum Casting Services
Frigate employs vacuum casting for precise, high-quality prototypes and low-volume production. We achieve optimale material consistency, minimized porosity, and tight dimensional tolerances.
Unsere Kunden





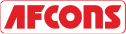

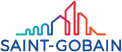


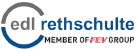

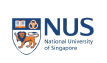
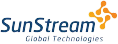

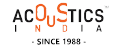




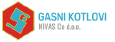
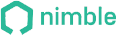
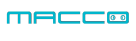













Advantages of Vacuum Casting Services
Enhanced Surface Finish
The process delivers parts with smooth, high-quality surfaces, reducing the need for additional finishing and improving visual appeal.
Faster Turnaround Time
Vacuum casting offers quick production cycles, enabling faster delivery of prototypes and low-volume parts, shortening development timelines.
Material Property Replication
Vacuum casting closely mimics the properties of final production materials, ensuring prototypes function similarly to their mass-produced counterparts.
Low-Volume Production Capability
Ideal for small production runs, vacuum casting provides a flexible solution for manufacturing limited quantities without costly molds or tooling.
Custom Vacuum Casting Services for Precision and Reliability
Custom vacuum casting provides high-precision prototypes and low-volume production with minimal porosity and tight dimensional tolerances. This method accurately replicates complex geometries and fine details, ensuring parts meet design specifications. It supports a variety of materials, including metals, plastics, and elastomers, offering flexibility for diverse applications. Vacuum casting enables rapid production, reducing lead times and accelerating development cycles. With excellent material property replication, parts produced through this process closely resemble their final production counterparts, ensuring functionality and durability in real-world applications.

Holen Sie Sich Ihr Angebot Jetzt
- Instant Zitat
- Auf-Zeit Lieferung
- Erschwingliche Kosten
Our Vacuum Casting Process






To capture the exact design details, a master pattern of the part is made, typically using 3D printing or CNC machining.
The master pattern is placed in a mold box, covered with silicone rubber, and then cured to form the mold.
The silicone mold is placed in a vacuum chamber, and the air is removed to prevent air pockets or bubbles in the mold.
The chosen material, often resin or metal, is heated and poured into the vacuum mold under low pressure, ensuring even flow and minimal defects.
The cast material can cure and solidify in the mold, accurately replicating the pattern’s shape and features.
Once cooled, the cast part is removed from the mold, and any finishing touches, such as sanding or polishing, are applied to achieve the desired surface finish.
Post-Processing Services in Vacuum Casting
Post-processing in vacuum casting enhances Komponente quality and performance for various industries. These services refine surfaces, improve durability, and meet specific technical needs.
Gloss Level: 10 - 90%
Automotive (dashboard panels), Consumer Electronics (casings)
Hardness (Rockwell): 60-80
Medical (device housings), Consumer Goods (custom enclosures)
Hardness (Vickers): 150-300
Aerospace (interior components), Luxury Goods (decorative parts)
Hardness: 200-500 HV
Automotive (grilles, trims), Electronics (connectors)
Color Stability: ≥5 years
Consumer Electronics (buttons, covers), Fashion (accessories)
Time: 1 - 3 hours
Automotive (heat-resistant components), Industrial Equipment
Surface Finish: Ra 0.4 - 1.6 µm
Aerospace (fittings), Medical (precise instrument parts)
Electronics (sensor housings), Marine (control panels)
Laser Power: 20 - 200 W
Branding (logos, serial numbers), Consumer Goods (custom textures)
Assembly Tolerance: ±0.1 mm
Medical (multi-part devices), Automotive (complex assemblies)
Methoding in Vacuum Casting
Automotive (high-strength parts), Aerospace (complex geometries)
Aerospace (thermal-resistant components), Automotive (engine parts)
Automotive (engine blocks), Medical (housings)
Aerospace (defect-free casting), Electronics (smooth finishes)
Automotive (heat-resistant components), Medical (custom devices)
Aerospace (structural parts), Consumer Electronics (casing)
Consumer Electronics (lightweight components), Automotive (heavy-duty parts)
Medical (precision devices), Industrial Equipment (gears, housings)
Automotive (high-volume parts), Aerospace (high-precision components)

Vacuum Casting Materials
Vacuum casting provides high-precision, low-volume production with excellent detail replication. This process ensures tight tolerances and smooth surfaces for functional prototypes.
Polyurethane Resins are ideal for creating durable, high-fidelity prototypes with excellent surface finish. They are available in various hardness levels, from soft to rigid, offering versatility for both functional and aesthetic parts.
Silicone rubber is used for producing flexible components. It has high tear resistance and can endure extreme temperatures. It’s commonly chosen for parts that require elasticity, such as seals, gaskets, and soft-touch products.
Epoxies are known for their high mechanical strength, low shrinkage, and superior adhesion. They are suitable for parts requiring dimensional stability and resistance to wear and are often used in aerospace, automotive, and industrial applications.
Aluminum-based alloys provide lightweight, high-strength parts with excellent thermal conductivity. Vacuum casting with aluminum alloys is ideal for producing components that need good corrosion resistance and heat dissipation, and it is often used in automotive and aerospace.
Zinc alloys offer good casting fluidity, high strength, and resistance to corrosion. They are commonly used for precision parts requiring tight tolerances and are frequently employed in electronics, automotive, and hardware applications.
Copper-based alloys, such as bronze and brass, are selected for their high thermal and electrical conductivity. They are often used in parts that handle electrical currents or high temperatures, such as connectors, heatsinks, and industrial components.
These transparent materials provide high-impact resistance and optical clarity. Polycarbonates, in particular, offer superior strength and heat resistance, making them ideal for components used in lighting, displays, and protective covers.
Cost-Effective Solution for Small-Batch Production
Vacuum casting provides a precise and cost-effective solution for small-batch production. Unlike traditional methods that require costly tooling for low-volume runs, this technique efficiently produces high-quality parts in smaller quantities. Frigate’s vacuum casting services utilize quick-turnaround silicone molds, significantly reducing setup costs and lead times. This makes it ideal for prototypes, short production runs, and customized components while maintaining high precision and performance.

Compliance for Vacuum Casting Services
Frigate adheres to stringent industry standards for Vacuum Casting services, ensuring high precision, safety, and environmental compliance. We follow rigorous protocols to guarantee the highest product quality. Our processes align with global regulations, ensuring reliable and consistent results. Each Komponente is manufactured with strict attention to detail, meeting performance and safety benchmarks.
Quality management system ensuring product consistency and continuous process improvement.
Environmental management system focusing on sustainable practices and reducing ecological impact.
Restriction of hazardous substances, ensuring components are free from dangerous materials.
European regulation for the safe use of chemicals, ensuring chemical safety in materials.
Aerospace standard ensuring the highest quality control and traceability for critical aerospace components.
Medical device regulation ensuring compliance with safety and performance requirements for medical-grade components.
Tonnage / Capacity in Vacuum Casting
Tonnage and capacity are critical factors in vacuum casting, influencing the precision, speed, and quality of the final components. The right parameters ensure that parts are produced efficiently, with optimale material properties and minimal defects.
Automotive (large moldings), Aerospace (high-strength parts)
Consumer Electronics (small components), Industrial Equipment (medium parts)
Medical Devices (precise parts), Aerospace (complex geometries)
Automotive (high-volume production), Consumer Goods (small enclosures)
Automotive (lightweight parts), Electronics (fine detail parts)
Aerospace (high-temperature resistant parts), Automotive (thermal components)
Medical (soft-touch components), Consumer Electronics (high-precision molds)
Aerospace (defect-free casting), Electronics (smooth finishes)
Dimensions in Vacuum Casting
Dimensions play a crucial role in vacuum casting, affecting the precision and functionality of the final components. Accurate dimensional control ensures that parts meet strict design specifications, with minimal deviations.
Aerospace (fittings), Automotive (precision parts)
Automotive (exterior trims), Consumer Electronics (buttons)
Medical Devices (housing), Industrial Equipment (components)
Electronics (small enclosures), Aerospace (thin-walled parts)
Automotive (interior parts), Consumer Electronics (housing)
Aerospace (structural components), Automotive (complex shapes)
Consumer Electronics (lightweight parts), Automotive (heavy components)

Tolerance for Vacuum Casting Services
Tolerance on the uniformity of part wall thickness.
Deviation from a perfect circle on cylindrical features.
Deviation between a surface and a reference surface, ensuring 90° angles.
Tolerance on the location of features relative to other features.
Deviation from a perfect circular cross-section in round features.
Tolerance on the location of holes, slots, and features.
Variation in thickness across the surface or wall of the part.
Deviation in angles between surfaces or features.
Deviation in the parallelism between two reference faces.
Deviation from the design model, ensuring the part matches the CAD file closely.

Quality Testing Standards for Vacuum Casting Services
Measures the part’s dimensions with high precision against CAD specifications.
Inspects surface for defects such as cracks, voids, or inconsistencies in texture.
Assesses the material's strength under tension and its ability to deform before breaking.
Evaluates material hardness to ensure durability and wear resistance.
Detects internal voids or bubbles that can affect part integrity and strength.
Measures heat flow and phase transitions to determine material stability at different temperatures.
Evaluates the material’s resistance to cyclic loading and its lifespan under stress.
Analyzes material to ensure compliance with alloy specifications and regulatory standards.
Determines the material’s ability to absorb impact energy without fracturing.
Determines the material's density and checks for internal voids or inconsistencies.
Measures how material dimensions change under temperature fluctuations, ensuring stability in varying environments.
Ensures the Komponente maintains its structural integrity under pressure or vacuum conditions, without leaks.
Inspection Techniques in Vacuum Casting
Surface roughness (Ra): 0.1 - 2 µm
Gloss: 10 - 90%
Aerospace (interior panels), Automotive (exterior parts)
Tolerance: ±0.05 mm to ±0.2 mm
Medical Devices (housings), Industrial Equipment (brackets)
Resolution: 0.1 - 1 mm
Penetration Depth: 20 - 50 mm
Aerospace (structural components), Automotive (engine parts)
Frequency: 0.5 - 10 MHz
Thickness: 1 - 50 mm
Medical (implantable devices), Aerospace (critical components)
Accuracy: ±0.01 mm
Range: 500 x 500 x 500 mm
Automotive (complex geometries), Electronics (connectors)
Temperature Range: -20°C to 500°C
Electronics (power components), Aerospace (insulation parts)
Hardness (Rockwell): 60 - 80, Vickers: 150-300 HV
Automotive (machinery components), Aerospace (wear-resistant parts)
Pressure: 1 - 10 bar
Time: 1 - 10 minutes
Medical (airtight enclosures), Automotive (sensor housings)


Industry Applications of Vacuum Casting
Engine blocks, Turbocharger components, Lighting housings
Aircraft brackets, Landing gear parts, Engine housings
Smartphone casings, Wearable device components, Remote controls
Prosthetic parts, Diagnostic devices, Implantable components
Hydraulic parts, Valve bodies, Pump components
Watch cases, Eyewear frames, Belt buckles
Boat fittings, Marine electronics, Hull components
Armor plating, Tactical equipment housings, Sensor covers
Wind turbine components, Generator housings, Battery casings
Robotic arms, Precision gears, Actuators
Antenna casings, Signal boosters, Base station housings
Optimizing Consumer Product Manufacturing with Vacuum Casting Technology
Balancing production efficiency and part quality can challenge consumer product manufacturing. Vacuum casting eliminates this issue by enabling the precise, low-volume production of complex components with reduced lead times. This process allows for creating detailed and genaue prototypes that simulate real-world performance, reducing the need for time-consuming post-processing. With the ability to handle a wide variety of materials, vacuum casting ensures that every Komponente produced meets both functional and aesthetic requirements.






Industrien, Die Wir Dienen
- Solide Fortschritte
Unser Fertigungs-Metriken
Fregatte bringt Stabilität, Kontrolle und zuverlässige Leistung, um Ihren sourcing-Operationen durch eine strukturierte multi-vendor-system.
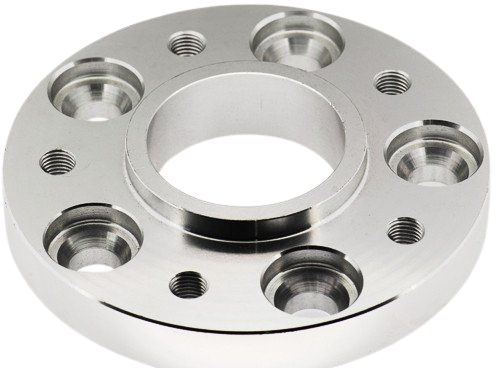
2,8 X
Sourcing Cycle Speed
Fregatte ' s pre-qualified network verkürzt die Zeit der Entscheidung zwischen RFQ-und PO-Platzierung.
94%
Auf-Zeit Lieferung Rate
Strukturierte planen von windows-und Logistik-linked Zeitpläne Verbesserung der Projekt-Ebene der Lieferung Zuverlässigkeit.
4X
Mehrteilige Konsolidierung
Wir aktivieren Sie Teil der Familie Dosierung über Lieferanten, die Fragmentierung zu verringern.
22%
Qualität Rejection Rate
Multi-level quality checks Inspektion und Feste Pläne unteren nicht-Konformitäten.
30%
Beschaffungskosten
Optimiert Verhandlungen mit Zulieferern und bulk-order-Strategien reduzieren Sie Ihre gesamten sourcing-Kosten.
20%
Manuelle Bearbeitung Zeit
Automatisierung von Beschaffungs-und Lieferanten-management erheblich reduziert die Zeit verbrachte auf manuelle Aufgaben.
Achieving Consistent, High-Quality Surface Finishes
Achieving consistent surface quality without extensive post-processing is a common challenge with conventional casting. Vacuum casting, however, delivers superior surface finishes due to the controlled vacuum environment that eliminates air bubbles and other defects. This results in parts with minimal surface imperfections, reducing the need for additional finishing work. Frigate’s vacuum casting process ensures high-quality surfaces, even for complex geometries, allowing parts to meet exacting standards with minimal additional effort or time spent on post-production.

Holen Sie sich Klarheit mit Unserem Manufacturing Insights
- Echte Wirkung
Wörter von Kunden
Sehen Sie, wie Globale OEMs und sourcing-Köpfe beschreiben Sie Ihre Erfahrung mit unseren skalierbaren Ausführung.
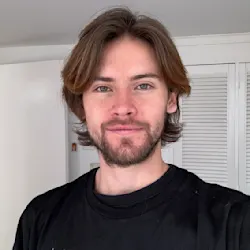
"Schnelle Bearbeitung und solide Qualität."
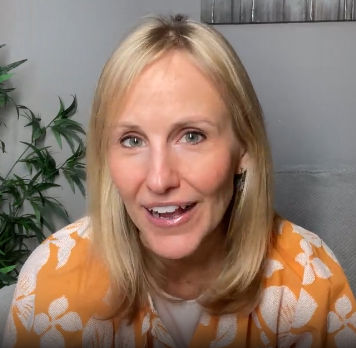
“Der instant quote tool hat uns gerettet-Zeit, und die Teile waren auf den Punkt. Empfehlen Fregatte!"
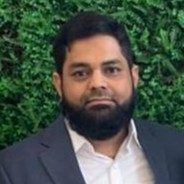
“Ich würde dringend empfehlen Fregatte wer will zu tun, Rapid Prototyping, und Ihre Ideen in die Fertigung. Eine Firma tun alle Arten von Produkt Entwicklung!"
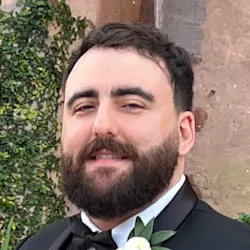
"Great service, fair Preise, und die Teile perfekt gearbeitet, in unserer Versammlung."
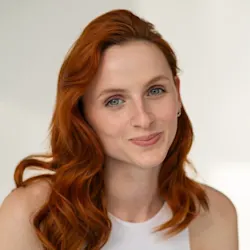
“Top-notch Bearbeitung und schnelle Lieferung. Mit den Ergebnissen sehr zufrieden."
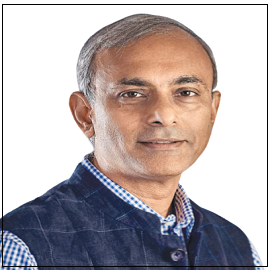
“Die nächste Störung geschieht in Prototyping & Manufacturing on-demand-und Fregatte den Weg! Ich persönlich glaube, daß die Fregatte die Möglichkeit, IIOT-fähigen cloud-Plattform mit Al."
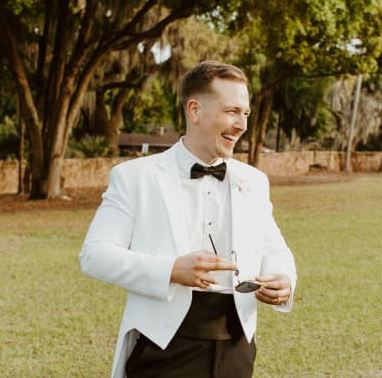
“Fregatte geliefert hochwertige Teile zu einem wettbewerbsfähigen Preis. Instant quote tool ist ein großes plus für uns!"

"Wir schätzen die Präzision und Qualität der bearbeiteten Komponenten in der jüngsten Lieferung—Sie erfüllen unsere Vorgaben perfekt und zeigen Fregatte, die diese Fähigkeit für die hervorragende Verarbeitung."
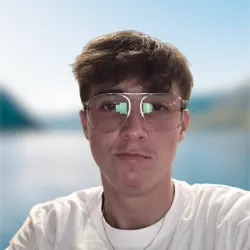
"Reibungslose Abwicklung vom Angebot bis zur Lieferung."

“Ich bin absolut glücklich zu arbeiten mit Lieferanten wie Fregatte, die waren sehr proaktiv & ergebnisorientiert . Fregatte hat eine hohe Bereitschaft team, die hat starke know how und Ihre Leidenschaft zum Produkt & Prozess waren absolut mitreißend."
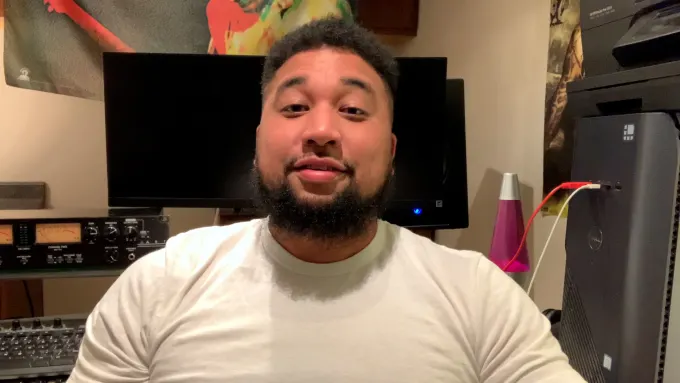
“Die Präzision, die auf diese Teile ist beeindruckend, und Sie kamen vor dem Zeitplan. Fregatte Prozess wirklich herausragend!"
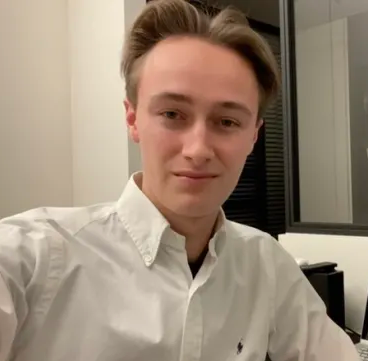
"Die Teile waren genau so, wie geskilled, und die instant-Zitat aus der Budgetierung ein Kinderspiel."
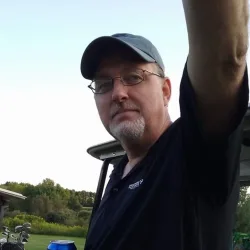
"Good value for the money."
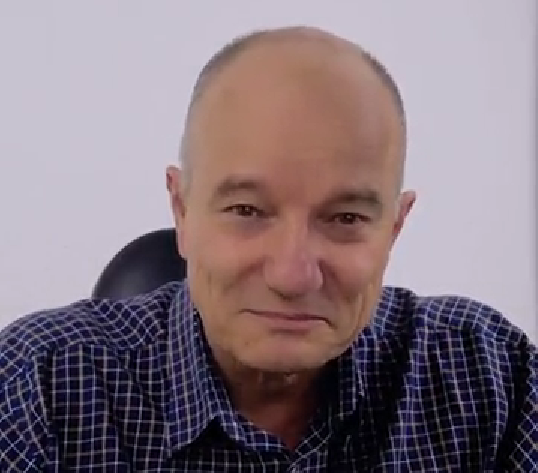
"Das finish war perfekt, und das team war einfach, mit zu arbeiten."

“Arbeiten mit der Fregatte war großartig. Ihre proaktive, ergebnisorientierte Ansatz und know-how durchleuchten, in jedem Projekt. Es war ein Vergnügen, die Zusammenarbeit mit Ihnen."

"Wir sind sehr zufrieden mit die rechtzeitige Lieferung und die Qualität des MIG-Schweißens-Kabel von der Fregatte. Ihre Aufmerksamkeit zum detail, sichere Verpackung und schnelle Reaktionsfähigkeit Stand out. Wir getrost empfehlen Fregatte Engineering Services Pvt. Ltd. als zuverlässiger partner für die Herstellung."
Having Doubts? Our FAQ
Check all our Frequently Asked Question
Vacuum casting maintains consistent material properties using precise temperature control during material pouring and curing. The vacuum environment eliminates air pockets, ensuring uniform density and mechanical characteristics in each batch.
The vacuum environment removes trapped gases, leading to denser, stronger materials with enhanced mechanical properties. This results in improved tensile strength, impact resistance, and reduced brittleness, which is critical for parts subjected to stress.
Yes, vacuum casting can closely replicate metal properties using specialized resins or metal-filled materials. For metals like aluminum or zinc, casting can achieve near-identical strength and thermal conductivity, making prototypes functionally representative of final production parts.
Combining the vacuum chamber and controlled curing ensures minimal shrinkage and precise mold formation. This results in tight tolerances (often within ±0.1mm), making vacuum casting ideal for parts that require perfect fit and functionality.
Material selection is crucial in vacuum casting, directly influencing the part’s strength, flexibility, and durability. Advanced resins and alloys are chosen based on their specific mechanical properties, ensuring the final part meets the performance criteria for each unique application.
Wir freuen uns auf Herstellung für Sie!
Füllen Sie das untenstehende Formular und unser Vertreter wird Sie in Kürze.
LOCATIONS
Sitz
10-A, First Floor, V. V Komplex, Prakash Nagar, Thiruverumbur, Trichy-620013, Tamil Nadu, Indien.
Operations Office
9/1, Poonthottam Nagar, Ramanandha Nagar, Saravanampatti Coimbatore-641035, Tamil Nadu, Indien. ㅤ
Weitere Standorte
- Bhilai
- Chennai
- Texas, USA